Shrinkage of injection molded parts refers to the phenomenon of dimensional reduction of plastic parts after cooling during the injection molding process. This is due to the volume contraction that occurs when the plastic material changes from a liquid to a solid state during the cooling process.
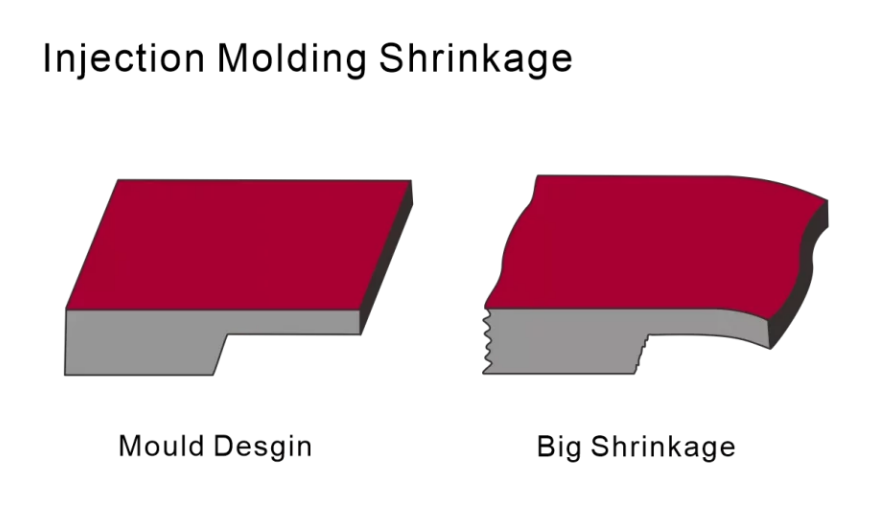
(Images from the web)
The main reasons for shrinkage of injection molded parts:
Material properties
- Crystalline plastics: such as polyethylene (PE), polypropylene (PP), nylon (PA), etc. These materials will form a crystalline structure during the cooling process, resulting in a larger volume change, and thus a higher shrinkage rate.
- Non-crystalline plastics: such as polystyrene (PS), acrylonitrile-butadiene-styrene (ABS), etc., these materials in the cooling process is mainly manifested in the glass transition, shrinkage rate is relatively low.
Injection molding process parameters
- Injection pressure: too low injection pressure will lead to insufficient filling of the mold cavity and large volume shrinkage after cooling; too high injection pressure may lead to increased internal stress, affecting the dimensional stability of the product.
- Injection speed: injection speed is too low, the filling time is prolonged, the cooling rate is not uniform, easy to produce shrinkage and warping; injection speed is too high, it will lead to too much shear heat, so that the material deformation.
- Mold temperature: too low a mold temperature will accelerate the cooling of the material, resulting in insufficient filling and shrinkage; too high a mold temperature will extend the cooling time, affecting production efficiency.
- Melt temperature: too low melt temperature will lead to poor material fluidity, incomplete mold filling and high shrinkage; too high melt temperature will increase the risk of material decomposition, affecting product quality.
- Pressure maintaining time and pressure maintaining pressure: Insufficient pressure maintaining time and pressure maintaining pressure will lead to insufficiently dense products, shrinkage after cooling; pressure maintaining time and pressure maintaining pressure is too long, it will increase the internal stress, resulting in product deformation.
Mold design
- Gate and runner design: unreasonable design of gate and runner will lead to uneven filling, resulting in shrinkage and deformation.
- Mold cooling system: Unreasonable design of cooling system will lead to uneven cooling, resulting in shrinkage and warpage.
- Mold exhaust: poor mold exhaust will lead to gas can not be discharged in time, the formation of gas bubbles or incomplete filling, affecting the size of the product.
Product design
- Wall Thickness: Uneven wall thickness of the product will lead to uneven cooling rate, resulting in different degrees of shrinkage.
- Shape complexity: complex shape of the product in the cooling process is prone to uneven shrinkage and deformation.
- Inserts: Metal inserts etc. inside the plastic will affect cooling and shrinkage, resulting in dimensional changes of the product.
Solution Measures
Optimize process parameters:
- Reasonably adjust the injection pressure, speed, mold temperature and melt temperature.
- Appropriately extend the holding time and increase the holding pressure.
Improve mold design:
- Optimize gate and runner design to ensure uniform filling.
- Improve mold cooling system design to ensure uniform cooling.
- Increase the mold venting holes to improve the venting effect.
Improve product design:
- Optimize wall thickness design to avoid uneven thickness.
- Simplify the product shape to reduce the risk of uneven shrinkage.
- Reasonable arrangement of inserts to reduce their impact on shrinkage.
Through reasonable process parameter adjustment, mold design optimization and product design improvement, the shrinkage phenomenon of injection molded parts can be effectively reduced to improve product quality and dimensional stability.