During the PCB assembly process, flux is used as a chemical agent to assist in component soldering. However, if not properly cleaned, residual flux can negatively impact circuit performance over time, leading to a decrease in surface insulation resistance and affecting the normal operation of the circuit. Additionally, uncleaned PCBs can accumulate external noise, further affecting the DC performance of the circuit. To address these issues, proper cleaning and drying are essential to ensure the circuit board performs optimally.
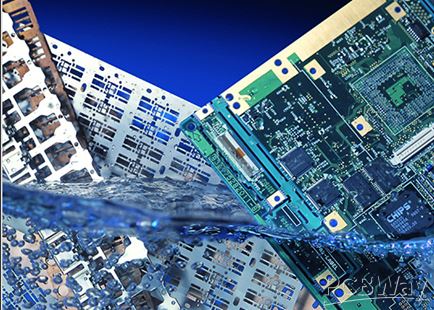
PCB cleaning can be mainly categorized into three types: water-soluble, rosin-based, and no-clean.
- Water Soluble: This type of flux requires cleaning with water (usually deionized water) after soldering to remove residues left from the soldering process.
- Rosin-Based: This type of flux requires cleaning with solvents (such as isopropyl alcohol) to remove rosin and other residues.
- No-Clean: This type of flux is designed not to require cleaning after soldering, as the residues are typically non-corrosive and have minimal impact on electrical performance.
The main cleaning methods include ultrasonic cleaning and alcohol brushing.
- Ultrasonic Cleaning: This method is commonly used for cleaning water-soluble and rosin-based fluxes. It utilizes the cavitation effect produced by ultrasonic vibrations to remove residues.
- Alcohol Brushing: This method is sometimes used for small batches or manual cleaning, especially for rosin-based flux cleaning.
Common steps for ultrasonic cleaning:
- Check for any components prone to detachment or requiring special handling, and select an appropriate cleaning solution based on the type of contaminants.
- Place the loaded PCB into the ultrasonic cleaning tank, ensuring it is fully submerged in the cleaning solution. Set the ultrasonic frequency according to the type of contaminants and the complexity of the PCB.
- After cleaning, place the PCB into a deionized water rinsing tank for multi-stage rinsing to gradually reduce cleaning solution residues. Follow with deionized water rinsing, either by spraying or soaking, to further remove any remaining cleaning agents and contaminants.
- After rinsing, use dry compressed air to blow off water droplets from the PCB, especially in slots, gaps, and beneath components where water tends to accumulate. Then place the PCB in a hot air dryer to ensure complete drying.
- Check the PCB for any remaining cleaning residues, incomplete drying spots, or other contaminants.
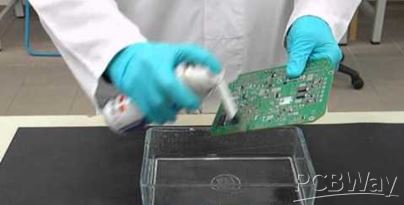
Maintaining PCB cleanliness is crucial for preventing circuit failures and enhancing overall system performance. It is essential to emphasize this aspect during the design and assembly process, ensuring that every detail meets high standards, thereby saving time and resources.