![]() |
OnShapeOnShape
|
|
![]() |
Autodesk Fusion 360Autodesk
|
|
|
BLHeli_32 ConfiguratorBLHeli
|
|
![]() |
Soldering iron (generic) |
|
![]() |
Bambu Lab A1 mini 3D printerBambu Lab
|
|
![]() |
Google Sheets |
12lb RC Hockey and Combat Robot
Designed to be a cost-effective entry to the 12lb "hobbyweight" combat robot weightclass, it uses the best bang-for-buck internals I could find housed inside an affordable and durable chassis. The total bot costs only $213.66, all tracked on a BoM.
The robot uses differential drive to move: two brushless motors typically used on RC airplanes go through a 14:1 planetary gearbox, mating with custom flexible hubs to absorb shock. Torque is transferred through captured square nuts, and axial play is reduced through the use of set screws and by preloading the opposite bearings with a flange on the end of the hub. The two 4" wheels are interchangeable between a durometer of 40A to 80A, depending on the surface of the arena.
Controlling these two brushless motors are FLYCOLOR Francy2 50A electronic speed controllers, custom configured to have aggressive timing, high start-up torque, and reduced current protection. The battery is a 850mAh 4S Lithium Polymer battery that goes first through a custom screw-switch containing an intermediary high-impedance connection, meant to slowly charge the capacitors attached to both ESCs. These capacitors resist the flyback experienced when brushless motors suddenly stop or brake.
The two ESCs received PWM signals from a receiver speaking a modified AFHDS-2A protocol, with commands coming from my personal transmitter. Along with the screw switch in the robot, I have a manual and automatic failsafe programmed into my transmitter in case of on-board failure or loss of connection.
The chassis of the robot was cut on a friend's CNC router out of 0.5" UHMW using a upcut 2 flute square nose endmill. The paths were created in Fusion 360. All intersections were designed to be friction-fit, to ensure that any shock is propagated through the tabs connection each piece rather than the eight shoulderbolts that secure the whole stack. Additionally, to reduce cost, these eight shoulderbolts (excluding the hardware used to mount the gearboxes) are the only fasteners in the entire system. All other pieces are secured solely through mechanical locking.
This robot competed at the Orange County Maker Faire on September 14th and 15th as both a hockey bot on a team of three, and solo as a hobbyweight combat robot.
12lb RC Hockey and Combat Robot
*PCBWay community is a sharing platform. We are not responsible for any design issues and parameter issues (board thickness, surface finish, etc.) you choose.
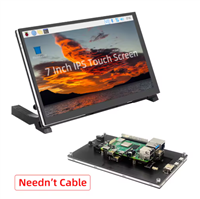
Raspberry Pi 5 7 Inch Touch Screen IPS 1024x600 HD LCD HDMI-compatible Display for RPI 4B 3B+ OPI 5 AIDA64 PC Secondary Screen(Without Speaker)
BUY NOW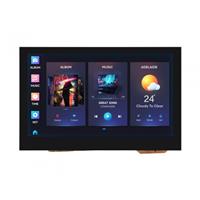
ESP32-S3 4.3inch Capacitive Touch Display Development Board, 800×480, 5-point Touch, 32-bit LX7 Dual-core Processor
BUY NOW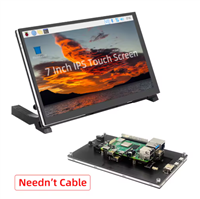
Raspberry Pi 5 7 Inch Touch Screen IPS 1024x600 HD LCD HDMI-compatible Display for RPI 4B 3B+ OPI 5 AIDA64 PC Secondary Screen(Without Speaker)
BUY NOW- Comments(0)
- Likes(3)

- 1 USER VOTES
- YOUR VOTE 0.00 0.00
- 1
- 2
- 3
- 4
- 5
- 6
- 7
- 8
- 9
- 10
- 1
- 2
- 3
- 4
- 5
- 6
- 7
- 8
- 9
- 10
- 1
- 2
- 3
- 4
- 5
- 6
- 7
- 8
- 9
- 10
- 1
- 2
- 3
- 4
- 5
- 6
- 7
- 8
- 9
- 10
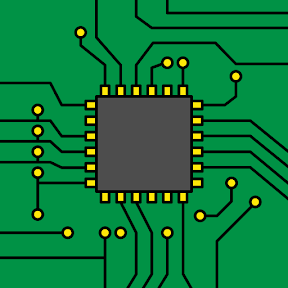
-
5design
-
2usability
-
4creativity
-
3content
More by Latedawn
-
Modifying a Hotplate to a Reflow Solder Station
176 0 2 -
MPL3115A2 Barometric Pressure, Altitude, and Temperature Sensor
131 0 1 -
-
Nintendo 64DD Replacement Shell
184 0 1 -
V2 Commodore AMIGA USB-C Power Sink Delivery High Efficiency Supply Triple Output 5V ±12V OLED display ATARI compatible shark 100W
377 4 1 -
How to measure weight with Load Cell and HX711
423 0 3 -
-
Instrumentation Input, high impedance with 16 bit 1MSPS ADC for SPI
531 0 0