![]() |
arduino IDEArduino
|
|
![]() |
Processing |
|
![]() |
Soldering iron |
Drawing Robot Board (Polargraph - Plotter)
Hi friends! I will show you how to build and use a plotter to draw vector or polar plotter images in this project. A polar graph machine uses two centered coordinates to generate drawings using a pen suspended on belts attached to two pulleys above the drawing surface.
I will start this project by first printing the necessary 3D parts and building the structure of the plotter, and then I will continue with the electronics and software part later in the project.
Due to the large size of the source code, we will use an Arduino UNO board based on Atmega328P and a ULN2003 motor driver for the stepper motors. You can build the circuit on a breadboard, but as you know I prefer to design a printed circuit board for a more professional prototype.
I share my printed circuit board designs as open source on PCBWay's project sharing page, where you can easily order the printed circuit boards I use in my projects, both assembled and empty PCBs. You can choose PCBWay for low-budget and high-quality printed circuit boards.
After soldering, I checked that the circuit board was working smoothly by uploading a simple stepper motor code at this stage. Then we continue the project by mounting the circuit board on the panel.
Our panel is almost ready, but first I printed 4 legs using a 3D printer and assembled them to make the panel stand.
At this stage, I add a paperclip to the servo motor arm for the control of the pen. Then, by uploading a simple servo motor code, I obtain the minimum and maximum angle of the servo arm. Thus, we have obtained the required angle range for the pen to touch down and up to the panel surface.
Before the programming step, I added a few more nuts to both belts and bearings to the gondola to make the pen more stable. Finally, I attached a drawing page to the panel surface.
In the source code section, first download and install the previous version of the Arduino code editor, 1-8-5. Polar graph code is more stable and without errors in this version.
When you first run the Arduino code editor, you will see that the Sketchbook section is still empty. First, go to the preferences, and keep your Sketchbook location in mind, then exit the code editor. After that, download the shared source code folder and copy the Arduino libraries inside it, go to your Sketchbook location and paste them into the Arduino libraries folder. Then go back to the shared source code folder and copy and paste the Arduino Polar Graph Server folder into the Arduino folder in your Sketchbook location. When you re-open the Arduino code editor, you will now see the Polar Graph Server code in the Sketchbook section. Open the Polar Graph server code, the important point here is that I have updated the “Configuration” section according to the current project components and shared the updated code with you.
I do not recommend making changes, but you can update the stepper motor direction pins if your motors move in the opposite direction. Now we can upload the code to the board, select the board type and the port it is connected to, and then press the upload button.
Once the upload is complete, open the Serial Monitor and update the Baud Rate to see if the code is executing correctly, if everything is okay you will get a “ready” message as shown on the screen. That's it for the Arduino source code, now let's move on to the Polar Graph software.
The Processing editor is required to run the Polar Graph software. Go to Processing and download version 2-2-1, then move the downloaded Processing folder to your “My Documents” location and run Processing, you will be given a message to “Create a Sketchbook folder”, and click “Done” to complete the installation.
When the editor opens you will again see that the Sketchbook section is empty, go to properties find your Sketchbook location, and exit the editor. Then go to the shared source code folder and copy the Processing libraries, then go to Processing's Sketchbook location and paste them into the libraries folder. Turn to the shared source code folder and copy the Polar Graph controller folder, then paste it into your Processing Sketchbook location. Run the Processing editor, go to the Sketchbook section, and open the Polar Graph code. You don't need to make any changes, just run the code, you may get a warning message, but after giving the necessary permissions the Polar Graph software will run.
Polar Graph opens with default properties and contains three main elements in the interface. The control panel with all buttons on the far left, the middle part, the gray rectangle representing the machine itself, and the command queue on the right side of the machine. You can zoom in and out of the machine surface using the scroll wheel of the mouse and you can “grab” and move the machine surface using the middle mouse button.
The setup section is used to define the machine configuration. I'm uploading my already-defined setup file for this project, and I've shared this configuration file with you. As you can see, when I uploaded the file, the dimensions of the machine and the page area changed.
There is a Home Point on the machine, this represents the starting point of the pen. This is also the starting point of the page. The Page and Home position of the project is approximately 120 millimeters. To find this value, place a horizontal line between the two motor gears and a vertical line 120 millimeters down from the midpoint of this line, the point where the vertical line ends is where you will place the pen. After placing the pen and updating the value, don't forget to press the Center Page and Center Home point buttons.
Here we update the Servo motor angles we obtained earlier for pen down and pen up movement. Then we make the serial connection of the board. If the connection is successful, you will see that the Connection message turns green and the machine is ready. Then I start the command queue by clicking on it so that every change I make will be sent to the machine directly. Now, to test that the servo positions are working correctly, I first send the lift range to the machine, then press the Test Lift Range button and observe that the servo motor and pen movement are working correctly. If you have built a different machine, you can update the required values via these buttons. If you make changes, send the machine settings to the machine and save your settings.
We are in the Input section, the purple circle on the screen symbolizes the pen, the point where the pen is located is defined to the machine by pressing the Set Home and Set Pen Position buttons.
If you want to test that the motors are moving in the correct direction, you can use the Move Pen to Point button. By selecting the point on the page surface where you want the pen to move, you can observe the motor and pen movements.
Using the Return to Home button, you can move the pen back to the Home point. This will confirm that the pen has correctly reached the home point.
The machine is working correctly and properly on the hardware side. Now let's look at the drawing side, you can upload an image file and enter Polar Graph settings to create Polar Graph images. However, creating a Polar Graph image is a bit complicated and requires some knowledge. For now, I will show you how to create a vector drawing.
Load the image with the Load Vector button, then move the image to the drawing area with the Move Vector button. Adjust the image size with the Resize Vector button, then select the drawing area with the Select Area button and define the drawing area with the Set Frame to Area tool.
Finally, click the Draw Vector button, and when you look at the command queue, you will see that the drawing has started. We have come to the end of another project, I hope it was a useful project for you.
Drawing Robot Board (Polargraph - Plotter)
*PCBWay community is a sharing platform. We are not responsible for any design issues and parameter issues (board thickness, surface finish, etc.) you choose.
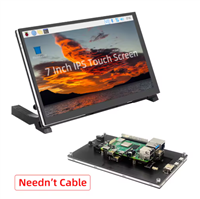
Raspberry Pi 5 7 Inch Touch Screen IPS 1024x600 HD LCD HDMI-compatible Display for RPI 4B 3B+ OPI 5 AIDA64 PC Secondary Screen(Without Speaker)
BUY NOW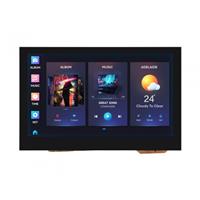
ESP32-S3 4.3inch Capacitive Touch Display Development Board, 800×480, 5-point Touch, 32-bit LX7 Dual-core Processor
BUY NOW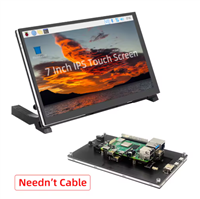
Raspberry Pi 5 7 Inch Touch Screen IPS 1024x600 HD LCD HDMI-compatible Display for RPI 4B 3B+ OPI 5 AIDA64 PC Secondary Screen(Without Speaker)
BUY NOW- Comments(2)
- Likes(10)

- EngineerApr 19,20250 CommentsReply
- EngineerJul 03,20240 CommentsReply
-
Electronic Adam Apr 13,2025
-
Anthony Pedotto Feb 22,2025
-
lightjunkie Dec 22,2024
-
Jason Bonitas Oct 03,2024
-
Engineer Sep 29,2024
-
Engineer Sep 19,2024
-
Andre Almeida Pinto Sep 16,2024
-
Engineer Aug 24,2024
-
Nik Jun 03,2024
-
Engineer May 31,2024
- 0 USER VOTES
- YOUR VOTE 0.00 0.00
- 1
- 2
- 3
- 4
- 5
- 6
- 7
- 8
- 9
- 10
- 1
- 2
- 3
- 4
- 5
- 6
- 7
- 8
- 9
- 10
- 1
- 2
- 3
- 4
- 5
- 6
- 7
- 8
- 9
- 10
- 1
- 2
- 3
- 4
- 5
- 6
- 7
- 8
- 9
- 10
More by MERT KILIC
-
How To Make DIY Remote Control Hoverboat at Home In this video, I showed you how to make your own hoverboat from materials available at home and chea...
-
How to Make DIY Arduino Gesture Control Robot at Home Parts Required for Receiver (Tank):1) Robot Tank Chassis - https://bit.ly/3j8y2Q52) Arduino Nano V3 ...
-
DIY Circuit Activty Board with Paperclips | MAKER | STEM You can be creative and design your own circuit and add different sensors (other LEDs...). The idea ...
-
ATtiny85 Wearable Activity Tracking Watch How to make the wearable activity tracking watch? This is a wearable gadget designed to vibrate when...
-
How to Build a Motorized 3D Scanning Turntable for Your Phone In this project, I’ll show you how to make a simple motorized turntable for 3D scanning. It has thre...
-
DIY Motorized 3D Scanning Turntable In this project, I’ll show you how to make a simple motorized turntable for 3D scanning. It has thre...
-
3D Printed Theo Jansen Style Octopod Robot (Arduino Based) Hi everyone! In this project, I will show you an amazing eight-legged robot in the Octopod style! It...
-
Creative Modular LED Lighting with Magnetic Pogo Pins & Wi-Fi Control Hi everyone! Welcome to my latest project: a modular, plug-in LED lighting system that is as fun as ...
-
Build a simple 3D printed CNC plotter machine Hi friends, do you remember this Mini CNC Plotter machine that uses hobby stepper motors and a few 3...
-
Circuit Activity Board - Educational Electronics Circuit Activity Board – A Hands-On Project to Learn Basic ElectronicsIn this project, we're going t...
-
Build a Simple 3D Wall Lighting Hi friends, this project shows how to make and control 3D hexagonal LED lighting panels. The project...
-
Robot Sumo Board Robot-sumo, or pepe-sumo, is a sport in which two robots attempt to push each other out of a circle ...
-
ESP32 Mecanum Wheels Robot and Bluetooth Gamepad Controller In this project we will see how to make an ESP32 Mecanum Wheels Robot which is capable of moving in ...
-
DIY Motorized WiFi Roller Blind - ESP8266 & Blynk In this project we will see how to control a roller blind via a smartphone application. The reason w...
-
Pet Feeder Controlled Via WiFi - ESP8266 How It Works?As you can see, a 3D design was used for the pet feeder. ESP8266-based Wemos D1 Mini bo...
-
ESP8266 Two Wheel Robot (NodeMCU and Stepper Motor) Generally, robot cars are built on a chassis with 2 DC motor wheels and a bovine wheel. While surfin...
-
3D Printed Rotating Table Board with Arduino Nano and 28BYJ-48 Stepper Motor This project shows how to make a 3D printed Rotating Table using Arduino and a hobby stepper motor. ...
-
Hand Gesture Controller for Robotic Hand Gesture Controller for RoboticThe hand gesture controller makes it possible to control applicat...
-
How To Make DIY Remote Control Hoverboat at Home In this video, I showed you how to make your own hoverboat from materials available at home and chea...
-
How to Make DIY Arduino Gesture Control Robot at Home Parts Required for Receiver (Tank):1) Robot Tank Chassis - https://bit.ly/3j8y2Q52) Arduino Nano V3 ...
-
DIY Circuit Activty Board with Paperclips | MAKER | STEM You can be creative and design your own circuit and add different sensors (other LEDs...). The idea ...
-
ATtiny85 Wearable Activity Tracking Watch How to make the wearable activity tracking watch? This is a wearable gadget designed to vibrate when...
-
How to Build a Motorized 3D Scanning Turntable for Your Phone In this project, I’ll show you how to make a simple motorized turntable for 3D scanning. It has thre...
-
DIY Motorized 3D Scanning Turntable In this project, I’ll show you how to make a simple motorized turntable for 3D scanning. It has thre...
-
3D Printed Theo Jansen Style Octopod Robot (Arduino Based) Hi everyone! In this project, I will show you an amazing eight-legged robot in the Octopod style! It...
-
Creative Modular LED Lighting with Magnetic Pogo Pins & Wi-Fi Control Hi everyone! Welcome to my latest project: a modular, plug-in LED lighting system that is as fun as ...
-
Build a simple 3D printed CNC plotter machine Hi friends, do you remember this Mini CNC Plotter machine that uses hobby stepper motors and a few 3...
-
Circuit Activity Board - Educational Electronics Circuit Activity Board – A Hands-On Project to Learn Basic ElectronicsIn this project, we're going t...
-
Build a Simple 3D Wall Lighting Hi friends, this project shows how to make and control 3D hexagonal LED lighting panels. The project...
-
Robot Sumo Board Robot-sumo, or pepe-sumo, is a sport in which two robots attempt to push each other out of a circle ...
-
Commodore 64 1541-II 1581 Floppy Disk Drive C64 Power Supply Unit USB-C 5V 12V DIN connector 5.25
163 1 3 -
Easy to print simple stacking organizer with drawers
87 0 0 -
-
-
-
Modifying a Hotplate to a Reflow Solder Station
1136 1 6 -
MPL3115A2 Barometric Pressure, Altitude, and Temperature Sensor
638 0 1 -
-
Nintendo 64DD Replacement Shell
494 0 2 -
V2 Commodore AMIGA USB-C Power Sink Delivery High Efficiency Supply Triple Output 5V ±12V OLED display ATARI compatible shark 100W
1438 4 3