|
Pickit3Microchip
|
MashtunController
This is a digital temperature controller with ability to connect to either a MCU9808 sensor or a DS18B20 sensor ( selectable vi a a jumper), It can display data via 1 of 2 types of I2C to LCD Display adaptors which can also be selected on board.
Its primary goal is to control a mashtun for home brewing ales etc. and is used on a stainless steel boiler to control the mashing temperature of the malt to a tight band, the mash is generally between 62 and 70 degrees C and is then followed by a boil with hops selected by a switch.
The control setpoint is adjustable via a rotary encoder (from 0 to 125 degrees C in increments of 0.0625 degrees C) and has an adjustable hysteresis (3 way dip switch from 1 to 8 x 0.0625 degrees C).
The micro-controller is programmed via a 6 pin header from a PICKIT3 Debugger.
The display gives information on the Temperature setting on the top line followed by the Sensor temperature current value, the bottom line contains the Details of whether the unit is in Mash mode or Heat mode followed by H=1 or 0 indicating the state of the heater relay, followed by the current hysteresis value.
There are 2 switches on the board, 1 for the selection of mash or boil and the other to switch off the heater.
The heater is switched on and off by a 40A solid state relay.
The state of the controller is also indicated by 4 LED's
The top LED is Blue and indicates the the unit is in operation by flashing
The next LED is Green and indicates the unit has been selected for Mash
The next LED is Red and indicates the unit is selected for Boil
The bottom LED is Yellow and indicates the heater is on (not influenced by the heater on/off switch)
The original project used a LM35 analog sensor which has since been discarded from this project in favor of digital sensors so all devices pertaining to the analog unit are no longer needed and should be omitted from the project build.
3 resistors were added after the original board was completed R20, R21 and R22, the first two are hard wired from R18 on the +5V side and run to RE1 (rotary encoder) pins 1 and 3. R22 runs from U1 pin 18 to C2 on the +5V side. a connection is required from U1 pin 18 to PS1 pin 10 for the DS18B20 sensor if used, the sensor connects to pins 8(+5V),9(0V) and 10(Signal) of PS1 connector. a stereo jack plug and panel mount socket was used to connect the sensor to the box
The 3 pin connector for U2 has been replaced by a 3 pin jumper for device selection and requires a link between pins 5 and 7 of the pads for U4 to complete.
RE1 and LED1 to 4 need mounting on the bottom layer as these pass through the face plate of whichever housing is used.
The DS18B20 was sealed in a copper tube with epoxy resin with the end soldered closed, this was soldered onto a coupler which was passed through the boiler wall, the MPU9808 sensor was epoxied to the bottom of the boiler and was the first sensor i used but suffered from lag.
Some form of re-circulation is essential to maintain uniform temperatures, My method was to fit a 30 RPM motor to the top of the lid and hang a bag or basket containing the grain from it to agitate the wort. other methods involve a false bottom and a recirculating pump.
MashtunController
*PCBWay community is a sharing platform. We are not responsible for any design issues and parameter issues (board thickness, surface finish, etc.) you choose.
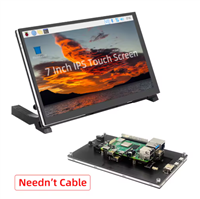
Raspberry Pi 5 7 Inch Touch Screen IPS 1024x600 HD LCD HDMI-compatible Display for RPI 4B 3B+ OPI 5 AIDA64 PC Secondary Screen(Without Speaker)
BUY NOW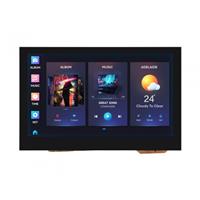
ESP32-S3 4.3inch Capacitive Touch Display Development Board, 800×480, 5-point Touch, 32-bit LX7 Dual-core Processor
BUY NOW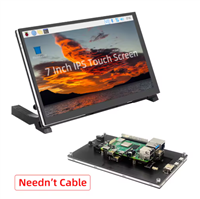
Raspberry Pi 5 7 Inch Touch Screen IPS 1024x600 HD LCD HDMI-compatible Display for RPI 4B 3B+ OPI 5 AIDA64 PC Secondary Screen(Without Speaker)
BUY NOW- Comments(0)
- Likes(0)

- 0 USER VOTES
- YOUR VOTE 0.00 0.00
- 1
- 2
- 3
- 4
- 5
- 6
- 7
- 8
- 9
- 10
- 1
- 2
- 3
- 4
- 5
- 6
- 7
- 8
- 9
- 10
- 1
- 2
- 3
- 4
- 5
- 6
- 7
- 8
- 9
- 10
- 1
- 2
- 3
- 4
- 5
- 6
- 7
- 8
- 9
- 10
More by David Ashmore
-
-
Commodore 64 1541-II 1581 Floppy Disk Drive C64 Power Supply Unit USB-C 5V 12V DIN connector 5.25
239 1 3 -
Easy to print simple stacking organizer with drawers
101 0 0 -
-
-
-
-
-
-
Modifying a Hotplate to a Reflow Solder Station
1180 1 6 -
MPL3115A2 Barometric Pressure, Altitude, and Temperature Sensor
666 0 1 -