![]() |
Autodesk Fusion 360Autodesk
|
Mechanical Mask
Introduction
This project is the design of a smart mechanical mask that can close or open autonomously. I got the idea to make this during the pandemic and it works fairly simple. The outer shields of the mask are moveable and when someone comes near within a certain distant from the mask it closes and alternately opens up when no one is in the proximity. To achieve this I used a Proximity Sensor and a Passive Infrared Sensor (PIR Sensor) where the proximity comes into action once a moving body is detected. In addition to this three push buttons are used on the left side of the mask. A button to activate auto mode and deactivate and the other two for opening and closing the mask. In addition to this the outer moveable shields house a filtering cloth embedded inside a Humidity Sensor which can detect when the filtering cloth (material) is wet.
LEDs are places on the front of the shield to indicate the condition of the filtering material ( red and green indicating wetness from highest to lowest respectively). The moveable shield use lead screws on either side to move them to their respective positions. The mask is controlled with an Arduino Nano as it is small in size and has the necessary amount of GPIO pins required for this project.
The main challenge I found in this project is to design the structure as light as possible and ergonomically pleasing since it is to be worn. On that note its also important to mention that a 5V small cooling fan is enclosed on the front of the shield which activates when the mask is in closed position. This would allow for some cooling.
Parts Description
1 - Arduino Nano
The Arduino Nano microcontroller is the heart of the control system and was used in both prototype designs of the face mask. The microcontroller is based on the ATmega328 microchip. The ATmega328 is a high-performance microchip comes with 32 KB ISP flash memory with read-while-write capabilities and 1KB EEPROM. The Arduino Nano is small and breadboard friendly which is useful in testing phases of different components with the microcontroller. It can be easily powered up via the mini-B USB (Universal Serial Bus) port or the V-IN pin or the 5V pin accessible on the microcontroller board. The mini-B USB port can be connected to a computer via a cable.
2 - Passive Infrared (PIR) Sensor
Passive Infrared Sensors are used to detect human motion within the sensor’s field of range. They are small, inexpensive and easy to use and are commonly found in many applications. They are referred to as PIR, Pyroelectric or IR motion sensors. The sensor in a motion detector is split into two halves. Since everything emits some low levels of infrared radiation, the hotter something is the more radiation it emits. The sensor detects motion by measuring the levels of radiation on each half and then if one half sees more radiation than the other, the two halves are wired so that the output will change to a high signal or a low signal.
3 - DHT22 Humidity Sensor
The DHT-22 is a low-cost digital humidity and temperature sensor. It utilizes a capacitor-based humidity sensor combined with a temperature sensor component to measure the surrounding air. The output of the sensor is a digital signal that is transferred to the appropriate digital pin. This sensor is perfect and accurate with working in a broad range if humidity and temperature. There are readily available libraries for accessing the relevant data and interpreting them to get useful information about the humidity and temperature.
4 - TF-LUNA Lidar Sensor
TF-LUNA is a proximity sensor based on LIDAR technology. It works on the TOF (Time of Flight) principle and is widely used in many applications due its precision and high frame-rate range detection. This module is used in the latter prototype for triggering the face mask to open or close depending on the proximity of a person. It is compact in size, consumes very little power and is light weight. It supports two interfaces for communication namely UART and IIC also known as I2C.
The LIDAR sensor emits near infrared rays and measure the phase difference between the emitting ray and the reflected ray to calculate the distance using the principle of TOF. Although it is hard to get an accurate distance between transparent objects like water or glass, its produces reasonably accurate distance readings between moving objects and stationary objects in real time.
5 - Lead Screw Linear Actuator
Linear actuators are, as the name suggest, mechanical devices that use energy to develop force and motion in a linear manner as opposed to rotational motion in with motors. This type of actuator offers several advantages including a simple design with minimum moving parts. They are self contained and can perform tasks that require relatively good speeds with identical behavior extending and retracting their mover.
One of the main functions of the face mask design is for it to be able to open and close upon trigger by either the user or a sensor. In order to achieve this motion both sides of the face mask covering the nose and mouth area of the user needs to be moveable and has to be attached to the main frame of the mask by integrating a linear actuator. This concept of design was chosen for its simplicity in achieving the desired result and after giving much consideration into the limitations and restrictions that might pose using other alternatives.
The linear actuator used for the opening and closing motion of the face mask comprises of a 6V DC motor which rotates the threaded output shaft lead screw. This is a compact and light weight linear actuator which is suitable for use in the face mask. It has an integrated M4x55mm threaded rod as output shaft which serves the purpose of the linear actuator. The speed reduction metal gears ensure a longer service life allowing higher torques and less noise.
6 - TB6612FNG DC Motor Driver
The TB6612FNG is a DC motor driver that is compact in size. The dual motor driver drives both motors which allows acceleration in forward or backward direction. In addition to this the TB6612FNG also allows short braking of the motor before reversing direction of rotation. The motor driver controls the current flow to the two motors. It can control up to two DC motors at a constant current of 1.2A (3.2A peak). Two input signals (IN1 and IN2) can be used to control the motor in one if the four function modes, that is: CW (Clockwise), CCW (Counter Clockwise), short-brake, and stop. The input voltage limit of this module is 2.2V – 13.5V and it is well within the range for this application as the linear actuator motor voltage rating is 6V.
- Pin Function Description
VM - (Motor Voltage) The power for the motors(2.2 to 13.5V)
VCC - (Logic Voltage) Voltage to power the chip and communications (2.7 to 5V)
GND - (Ground) Common Ground for both motor and logic voltage
STBY - (Standby) Active 'high' for it to work
AIN1/BIN1 - (Input1/channels(A,B)) Input for Direction of motor
AIN2/BIN2 - (Input2/channels(A,B)) Input for Direction of motor
PWMA/PWMB - (PWM input(A,B)) Input to control Speed of motor
A01/B01 - (Output1/channels(A,B)) Output to connect to motor
A02/B02 - (Output2/channels(A,B)) Output to connect to motor
In order to control the motors, the specific logic states have to be communicated to the motor driver module from the microcontroller for it to send the instructions to the specific motors. The logic states of the pins on the motor driver for each individual operation is shown below.
- [in1/HIGH, in2/HIGH, out1/LOW, out2/LOW] - COUNTER CLOCKWISE
- [in1/LOW, in2/HIGH, out1/LOW, out2/HIGH] - SHORT BRAKE
- [in1/HIGH, in2/LOW, out1/HIGH, out2/LOW] - CLOCKWISE
- [in1/HIGH, in2/LOW, out1/LOW, out2/LOW] - SHORT BRAKE
- [in1/LOW, in2/LOW, out1/OFF, out2/OFF] - STOP
Prototype Design
All the parts of the mechanical mask were designed using Fusion360 and then 3D Printed and assembled. The design of this prototype influenced a lot on the dimensions of the components used in addition to factors such as ergonomics and functionality. Furthermore, the components that compose the face mask needed to be placed in a balanced manner so that once the face mask is worn the wearer would experience minimum discomfort. The mask is designed so that it can be worn and kept in place by two straps with one going over the head and another going behind the head. This would give sufficient support and force to keep a tight fit to face. In addition to this rubber padding material is used around the ear holes on the left and right plates of the mask for comfort.
The mask was created in one size as a prototype several measurements of the head and face were required to proceed in the design of the prototype using CAD software. After coming up with a sketch of how the mask would look like, the next step was to identify the individual parts that would comprise the full assembly. Single rigid parts were designed as one whole part unless there were no limitations posed on the manufacturing front. The two main pieces that held the linear actuators for the movement of the face shield was designed initially as it formed the base for building on the other parts that were to be assembled in the future.
After designing the left and right plates, they were joined as one piece with the required distance between them for accommodating the face of the user. Two pieces are used at the nose and chin sections to join the two plates and bolted together after applying a coat of glue for added bonding strength. The bottom plate that goes under the two side plates also allow for extra rigidity of the mask and is bolted to the left and right plates. For holding the strap that goes over the head an addition part is used as a strap holder on top of both the left and right plates and bolted with M2.5 Hex bolts. Just below the left ear hole the main control push buttons holder is placed and is mounted on top of the linear actuator motor driver case.
Once the mask structural frame was assembled with all the parts giving it a rigid form, the next step was to design the support structures and holders for fixing the sensors. The front area of the side plates has structures on the top inside the mask. These structures are used to fix the flexible rubber element which takes on the shape of the face and nose area when the mask is worn giving it a much better fit to face and improving the overall comfort aspect of wearing the mask. The shields which opens and closes are on the outside of the mask. The linear actuator is fixed on the inside and the shields are on the outside of the mask.
The buttons used in this design are easier to press as it is bigger in size. The placement had to be made by adjusting the side plate of the face mask. They are placed in slots designed on the left plate of the mask. From an ergonomic perspective it is much easier to access the buttons and press when placed on the side. The mask has a hinged end piece with the cut-outs made in it for the strap that goes behind the head. This is clearly more ergonomic in terms of achieving a better grip on the head when strapped on as it would turn to take the shape of the back of the head who is wearing the mask. The earholes have a groove around them to fit the soft sponge more precisely for better comfort.
Both left and right shields are attached by the Nose Attachment Piece and the Bottom Plate. They are secured in place with bolts and glue. The Nose Attachment Piece has the housing area for the TF-LUNA proximity sensor at the center. This position allows for better reading of data from the sensor in most orientations as it is in line with the nose and mouth area. The front of the Bottom Plate houses the PIR sensor and it is also aligned in a central position. The Nose clip on the top of the Nose Attachment provides a grip on the nose for better stability of the mask when worn. Each side plate has areas that protrude which house the motors of the linear actuators on either side. The Guide rails run on the top and bottom of the linear actuator parallel to the lead screw of the linear actuator. The guide rails are fixed by placing them in a constrained position by running them through holes and a cover is fixed to restrict its movement in the parallel direction when the linear actuator is active.
The underside of the Bottom Plate houses the battery compartment and the microcontroller with the main PCB. The TB6612FNG Motor Driver, the Arduino Nano and the Logic Level Convertor are all soldered onto to the assigned slots of the PCB. All the electronic wires from the sensors and the motors and directed to the microcontroller though a cut-out in the Bottom Plate from inside of the mask. This allows for better management of wires in order to avoid any accidental loose connections when handling the mask. The power switch is fixed right below the PIR sensor which can be easily accessible.
The linear actuator assemblies of this prototype are fixed on the inner side of the left and right plates. The moveable shields are on the outside. The motor which drives the lead screw is housed in the side plates itself removing the need for an additional part to fix the motor. This also gives more stability when the motor rotates the lead screw of the linear actuator. The end of the lead screw is fitted to the Motor End Stop sub assembly. The Motor End Stop sub assembly consists of an M4 nut fitted into a cut-out on one side of a cylindrical block. The end of the lead screw goes in this nut and is fixed so that when the lead screw rotates this sub assembly rotates as well. The other end of the cylindrical block has a hole where an aluminum hollow shaft piece is pushed in with some amount of the shaft left protruding out. The shaft is glued into place in the cylindrical block so that when the lead screw rotates the whole sub assembly rotates. The protruding part of the shaft of the Motor End Stop sub assembly goes into the bearing bracket which houses a bearing and is bolted to the opposite end of the motor on the side plate.
The Guide Rails of the linear actuator assembly are aluminum hollow rods that goes through brackets with holes which are part of the side plates. The holes are sealed off with caps on the outer sides and filled with plastic filament on the inside to restrict any parallel movement of the Guide Rails when the linear actuator is active.
The base of the moveable structure of the linear actuator has the nut fixed inside and moves when the lead screw rotates. It has holes for fixing linear bearings that move the structure along the Guide Rails. This structure goes through the cut-outs on the side plates and are bolted to the shied which actually open and close the mask. The linear actuator is mounted in a wall mount configuration and the shield is designed so that when it moves it covers the parts that are exposed to the surrounding. The motor of the linear actuator is kept in place by a cover piece that screws onto the inner side.
The Left Moveable Shield houses the cooling and air regulating fan and the two indicative LEDs (red and green LEDs) for indicating the user of the moisture levels in the filtering element. The Easy access cut-out is used for maintenance and easy access to the indicating LEDs and the cooling fan. It is covered up with a panel that screws on top. The Right Moveable Shield houses the humidity sensor and the filtering element. It has cut-outs where the filtering element is placed for air to pass though the filter. The filtering element is held in place with the help of magnets and the magnets can be pushed to release the filtering element when replacing it.
Both shields house an inner and outer limit switch holder which attached the limit switches. These switched are triggered by Switch Pushers which are fixed to the outer side of the left and right plates of the mask. They are fixed precisely so that when the actuator moves the left and right shields and reaches the limits they are pushed and a “high” signal sent to the microcontroller.
The bottom side of the Base plate houses all the electronics and the battery compartment. It also has the main power switch holder which sits right below the PIR sensor. The battery compartment is part of the Base plate and covered off with the Battery Case Cover. The Power Connector beside the Battery Compartment connects the battery terminals to the main PCB with 1.5mm copper wires. The electrical wires coming from the sensors and right motor of the Linear Actuator are guided through the Wire Guide. The main PCB is bolted to the bottom side of Bottom Plate with the Outer and Inner Support structures. The secondary PCB support structure is fixed to the bottom side of the Bottom Plate and holds the TB6612FNG Motor Driver and the Logic Level Convertor PCBs. The Logic Level Convertor converts the 5V logic from the microcontroller to 3.3V logic which is required by the TF-LUNA module and vice versa. An Electronic Panel is used to cover the electronics with the use of the Electronic Support Bracket.
Working Principle
The TF-LUNA proximity sensor is mounted in the Nose Attachment which joins the two side plates of the mask. The TF-LUNA communicates using the UART protocol to the Arduino Nano to transmit data. Since there is no requirement for the sensor to receive any data, only transmission of data from the sensor to the microcontroller happens. It used the principle of Time of Flight (TOF) to get the distance between an object. A modulated wave of infrared light is emitted from the light source and received by the photosensor and the difference in phase angle and time it took to reach is used to calculate the distance using specific algorithms. The PIR sensor is similar to the one used in Prototype I and the limit switches also function in the same way with some modifications brought to the position of them in the design. Prototype II uses a DHT-22 Humidity sensor to measure the moisture and has two indicative LEDs (red and green) to indicate the moisture levels in the filtering element.
The microcontroller receives data from the TF-LUNA (Proximity Sensor) and the Passive Infrared Sensor (PIR Sensor) and send the appropriate signal to the TB6612FNG Motor Drivers to either rotate the motors of the linear actuator clockwise, anticlockwise or halt. If any of the limit switches are pushed while opening or closing of the shields, a signal is sent to the microcontroller to indicate it has reached its limit of movement while closing or opening of the shield. Based on the feedback from the limit switches the motor is rotated. The DHT-22 humidity sensor also sends humidity data to the microcontroller and the appropriate indicative LED is lit to indicate the moisture levels in the filtering element to know if it should be replaced. The microcontroller turns on the cooling fan whenever the shields are in a closed position and turns off the fan when the shields are in an open position. This is done with a BD681 Bipolar Junction Transistor. The control buttons also have back LEDs which can be controlled. These LEDs are turned on whenever the manual mode is active and the back LEDs are turned off when it is auto mode. This too is controlled using a BD681 BJT transistor.
Component Wiring
PCB Design
Since creating one single PCB seemed more cost effective, the main and secondary PCB are both printed as one and then later sawed off when mounting them on mask. The main PCB contains the Arduino Nano, the resistors for the control buttons and limit switches, the capacitors for the voltage regulator, the voltage regulator, the main power connection pads, the two transistors for switching the cooling fan and the back LEDs of the control buttons, and the linear actuator motor pads for both motors. The secondary PCB contains the connection pads for the TB6612FNG motor driver and the Logic Level Convertor.
3D Printed Prototype
Conclusion
To further improve this prototype additional functionality can be added such as adding a real time clock module such as DS3231 to accurately measure the elapsed time between readings of the sensors to activate the linear actuators, but this would also mean that there would be a need for more GPIO pins and would have to replace the current microcontroller with one which has more GPIO pins let alone restrictions in size. With the growing number of compact microcontroller boards and sensors integrated with multiple functions the final prototype can further be enhanced in design and functionality while reducing the overall weight. In addition to this the linear actuators move the shield at a slower rate compared to what is desired, hence to remedy this problem the linear actuators can be swapped to something with a higher RPM via gear ratio manipulation. Last but not least I hope you benefitted in someway by reading my post and welcome all comments. Thanks!
Watch on YouTube - Mechanical_Mask
Mechanical Mask
*PCBWay community is a sharing platform. We are not responsible for any design issues and parameter issues (board thickness, surface finish, etc.) you choose.
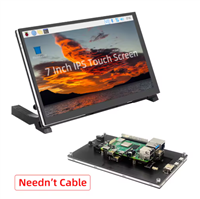
Raspberry Pi 5 7 Inch Touch Screen IPS 1024x600 HD LCD HDMI-compatible Display for RPI 4B 3B+ OPI 5 AIDA64 PC Secondary Screen(Without Speaker)
BUY NOW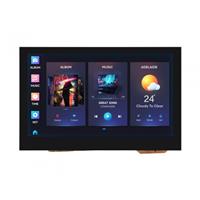
ESP32-S3 4.3inch Capacitive Touch Display Development Board, 800×480, 5-point Touch, 32-bit LX7 Dual-core Processor
BUY NOW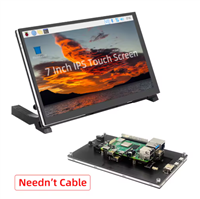
Raspberry Pi 5 7 Inch Touch Screen IPS 1024x600 HD LCD HDMI-compatible Display for RPI 4B 3B+ OPI 5 AIDA64 PC Secondary Screen(Without Speaker)
BUY NOW- 3 USER VOTES
- YOUR VOTE 0.00 0.00
- 1
- 2
- 3
- 4
- 5
- 6
- 7
- 8
- 9
- 10
- 1
- 2
- 3
- 4
- 5
- 6
- 7
- 8
- 9
- 10
- 1
- 2
- 3
- 4
- 5
- 6
- 7
- 8
- 9
- 10
- 1
- 2
- 3
- 4
- 5
- 6
- 7
- 8
- 9
- 10
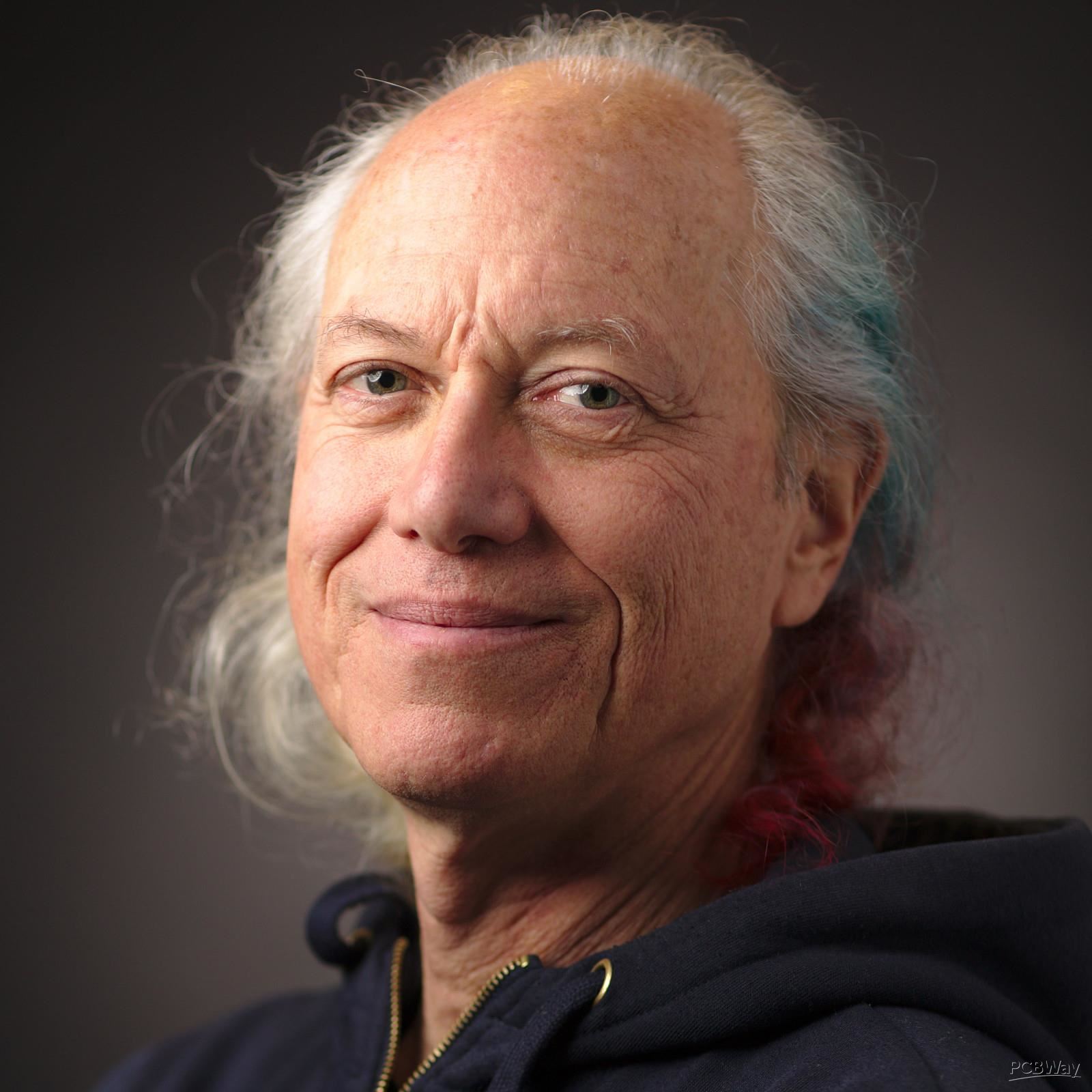
-
9design
-
8usability
-
8creativity
-
5content
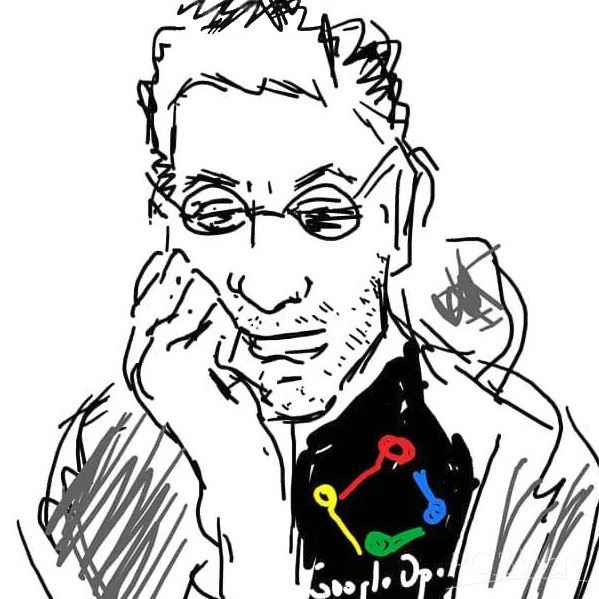
-
9design
-
8usability
-
8creativity
-
7content

-
10design
-
10usability
-
10creativity
-
10content
More by Hanoon Malik
-
Modifying a Hotplate to a Reflow Solder Station
464 0 4 -
MPL3115A2 Barometric Pressure, Altitude, and Temperature Sensor
277 0 1 -
-
Nintendo 64DD Replacement Shell
279 0 1 -
V2 Commodore AMIGA USB-C Power Sink Delivery High Efficiency Supply Triple Output 5V ±12V OLED display ATARI compatible shark 100W
715 4 2 -
How to measure weight with Load Cell and HX711
530 0 3 -
-
Instrumentation Input, high impedance with 16 bit 1MSPS ADC for SPI
610 1 0
Thanks. Here is the link for the code -> https://github.com/hannu-hell/Mechanical_Mask_Main_Code. As for the design files the link is under custom parts and enclosures section of this article. :)