![]() |
KiCADKicad
|
Motor drive model
A motor drive model using a DC motor involves a detailed understanding of several components and concepts. The model aims to simulate the behavior of a DC motor under various conditions and control strategies. Here’s an in-depth explanation of such a project:
Introduction to DC Motors
DC motors are widely used in various applications due to their simplicity, reliability, and ease of control. They convert electrical energy into mechanical energy through the interaction of magnetic fields. The basic components of a DC motor include the stator (which produces a magnetic field), the rotor (or armature, which rotates within the magnetic field), commutator, brushes, and the power supply.
Key Components of the Motor Drive Model
1. DC Motor:
- The core component, a DC motor, has specifications like rated voltage, current, speed, and torque. The motor’s performance characteristics are governed by equations that relate these parameters.
2. Power Supply:
- A DC power source provides the necessary voltage and current to the motor. This can be a battery or a power converter (AC to DC).
3. Controller:
- The controller manages the motor’s operation. It can be a simple on/off switch or a more sophisticated pulse-width modulation (PWM) controller. PWM controllers adjust the duty cycle of the voltage applied to the motor, effectively controlling its speed and torque.
4. Feedback Mechanism:
- To ensure accurate control, feedback systems like encoders or tachometers measure the motor’s speed and position. These sensors provide real-time data to the controller, enabling closed-loop control.
5. Driver Circuit:
- The driver circuit amplifies the control signals from the controller to the levels required by the motor. It typically includes transistors or MOSFETs capable of handling high current and voltage.
Control Strategies
The control strategy is essential for achieving the desired performance. Common control strategies include:
1. Open-Loop Control:
- Simple but less accurate, it involves directly setting the voltage or current without feedback.
2. Closed-Loop Control:
- More complex but precise, it uses feedback to adjust the input to the motor. Common closed-loop control methods include:
- Proportional-Integral-Derivative (PID) Control:
- PID controllers adjust the motor input based on the difference between the desired and actual performance.
- State-Space Control:
- Uses state variables for more sophisticated control, suitable for systems with multiple inputs and outputs.
Simulation and Implementation
1. Simulation Tools:
- Tools like MATLAB/Simulink are commonly used to simulate the motor drive model. These simulations allow for testing different control strategies and tuning parameters without physical hardware.
2. Implementation:
- Once the model is validated through simulation, it can be implemented using microcontrollers (like Arduino, PIC, or STM32) or dedicated motor driver ICs. The hardware setup includes connecting the motor to the driver circuit, interfacing sensors for feedback, and programming the controller.
3. Testing and Validation:
- The implemented system is tested under various load conditions and operating scenarios to ensure it meets the desired specifications. Fine-tuning may be required based on the test results.
Applications
DC motor drive models are used in a wide range of applications, from household appliances to industrial automation. They are essential in robotics, electric vehicles, conveyor systems, and any application requiring precise motor control.
Conclusion
Creating a motor drive model using a DC motor involves a comprehensive understanding of electrical and mechanical principles, control theory, and practical implementation skills. By simulating and then implementing the model, one can achieve precise control over the motor’s performance, enabling its use in various sophisticated applications. The project encompasses both theoretical modeling and practical engineering, providing a robust platform for learning and innovation in motor control systems.
Motor drive model
*PCBWay community is a sharing platform. We are not responsible for any design issues and parameter issues (board thickness, surface finish, etc.) you choose.
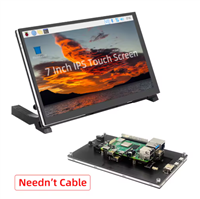
Raspberry Pi 5 7 Inch Touch Screen IPS 1024x600 HD LCD HDMI-compatible Display for RPI 4B 3B+ OPI 5 AIDA64 PC Secondary Screen(Without Speaker)
BUY NOW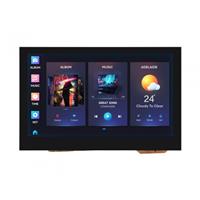
ESP32-S3 4.3inch Capacitive Touch Display Development Board, 800×480, 5-point Touch, 32-bit LX7 Dual-core Processor
BUY NOW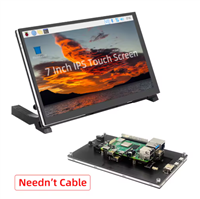
Raspberry Pi 5 7 Inch Touch Screen IPS 1024x600 HD LCD HDMI-compatible Display for RPI 4B 3B+ OPI 5 AIDA64 PC Secondary Screen(Without Speaker)
BUY NOW- Comments(0)
- Likes(0)

- 0 USER VOTES
- YOUR VOTE 0.00 0.00
- 1
- 2
- 3
- 4
- 5
- 6
- 7
- 8
- 9
- 10
- 1
- 2
- 3
- 4
- 5
- 6
- 7
- 8
- 9
- 10
- 1
- 2
- 3
- 4
- 5
- 6
- 7
- 8
- 9
- 10
- 1
- 2
- 3
- 4
- 5
- 6
- 7
- 8
- 9
- 10
More by Engineer
-
-
Commodore 64 1541-II 1581 Floppy Disk Drive C64 Power Supply Unit USB-C 5V 12V DIN connector 5.25
340 1 3 -
Easy to print simple stacking organizer with drawers
121 0 0 -
-
-
-
-
-
-
Modifying a Hotplate to a Reflow Solder Station
1228 1 6 -
MPL3115A2 Barometric Pressure, Altitude, and Temperature Sensor
705 0 1 -