|
STM32F334C8T6 |
x 1 | |
|
ESP32-PICO-D4 |
x 1 | |
|
IAUT150N10S5N035ATMA |
x 3 | |
|
LM5017SD/NOPB |
x 1 | |
|
NCP5183DR2G |
x 1 | |
|
TSV991ILT |
x 2 | |
|
SN65HVD231DR |
x 1 |
Solar charge controller with MPPT
Solar charge controller with MPPT
The charge controller is controlled using a specialized STM32F334C8T6 microcontroller with a high-resolution PWM controller (HRPWM) on board. The use of this device is possible, both as a debugging complex for studying algorithms for finding the maximum power point (TMM), as well as a complete device for working in an autonomous solar power plant with a capacity of up to 500W.
1) Features:
- Input voltage: 15...60V
- Output voltage: 12/24V or 2-6S Li-ion
- Output current: 20A
- Frequency: 100 kHz
- Efficiency: up to 96%
- Type battery: AGM, GEL, Li-ion, LiFePo4
- Interface: CAN, Wi-Fi
- Size: 136 x 70 x 26 mm
2) Used protection:
- Over current battery
- Over current input
- Over voltage battery
- Over voltage PV
- PV reverse polarity (max 100V)
- Over temperature
3) Documents:
When developing a charge controller, the main emphasis is on creating reliable hardware using the best components and on implementing the most efficient TMM search algorithms. There are no electrolytic capacitors in the controller, instead of them solid-state polymer capacitors with an increased service life are used, and the thermal modes of the device are optimized, which together will ensure a guaranteed service life of at least 10 years. This will increase the reliability of autonomous mini-power plants and reduce equipment maintenance costs.
The charge controller is made on a single 4-layer printed circuit board (PCB) 1.6 mm thick of FR-4 material and a copper thickness of 1 Oz or 35 μm. When changing the thickness of the board, you need to adjust the case of the device!
All source materials for the project are distributed under the MIT license.
Solar charge controller with MPPT
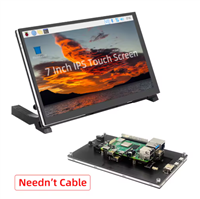
Raspberry Pi 5 7 Inch Touch Screen IPS 1024x600 HD LCD HDMI-compatible Display for RPI 4B 3B+ OPI 5 AIDA64 PC Secondary Screen(Without Speaker)
BUY NOW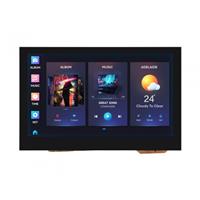
ESP32-S3 4.3inch Capacitive Touch Display Development Board, 800×480, 5-point Touch, 32-bit LX7 Dual-core Processor
BUY NOW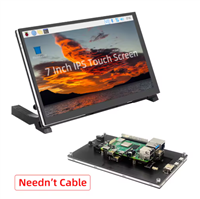
Raspberry Pi 5 7 Inch Touch Screen IPS 1024x600 HD LCD HDMI-compatible Display for RPI 4B 3B+ OPI 5 AIDA64 PC Secondary Screen(Without Speaker)
BUY NOW- Comments(7)
- Likes(22)
-
Engineer Nov 20,2024
-
Engineer Aug 23,2023
-
Repkon Makina Feb 27,2023
-
Dylan Krul Jan 27,2023
-
Engineer Jan 26,2023
-
Catur Sujatmiko Purnomo Aug 07,2022
-
Derek B Apr 22,2022
-
Uğur Yıldız Feb 17,2022
-
Dmitry Mar 27,2021
-
Engineer Jan 08,2021
-
Engineer Dec 19,2020
-
Datta Nagare Dec 14,2020
-
Marhaunichy Maryan Iosifovich Jun 29,2020
-
Sam Catchpole-Smith Jun 27,2020
-
El Mexicano Jun 23,2020
-
jordanyte May 15,2020
-
Kapacita LuBos May 09,2020
-
Sergey Evdokimenko May 08,2020
-
Oleg Oleg Apr 28,2020
-
Engineer Apr 25,2020
-
Lisss Apr 21,2020
-
Ilya Apr 20,2020
- 12 USER VOTES
- YOUR VOTE 0.00 0.00
- 1
- 2
- 3
- 4
- 5
- 6
- 7
- 8
- 9
- 10
- 1
- 2
- 3
- 4
- 5
- 6
- 7
- 8
- 9
- 10
- 1
- 2
- 3
- 4
- 5
- 6
- 7
- 8
- 9
- 10
- 1
- 2
- 3
- 4
- 5
- 6
- 7
- 8
- 9
- 10

-
1design
-
2usability
-
3creativity
-
4content

-
8design
-
8usability
-
8creativity
-
8content

-
10design
-
10usability
-
10creativity
-
10content

-
10design
-
10usability
-
8creativity
-
8content

-
10design
-
10usability
-
10creativity
-
9content
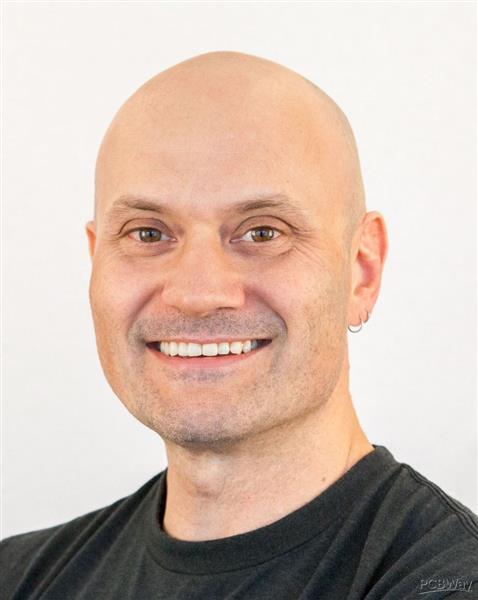
-
10design
-
8usability
-
7creativity
-
8content
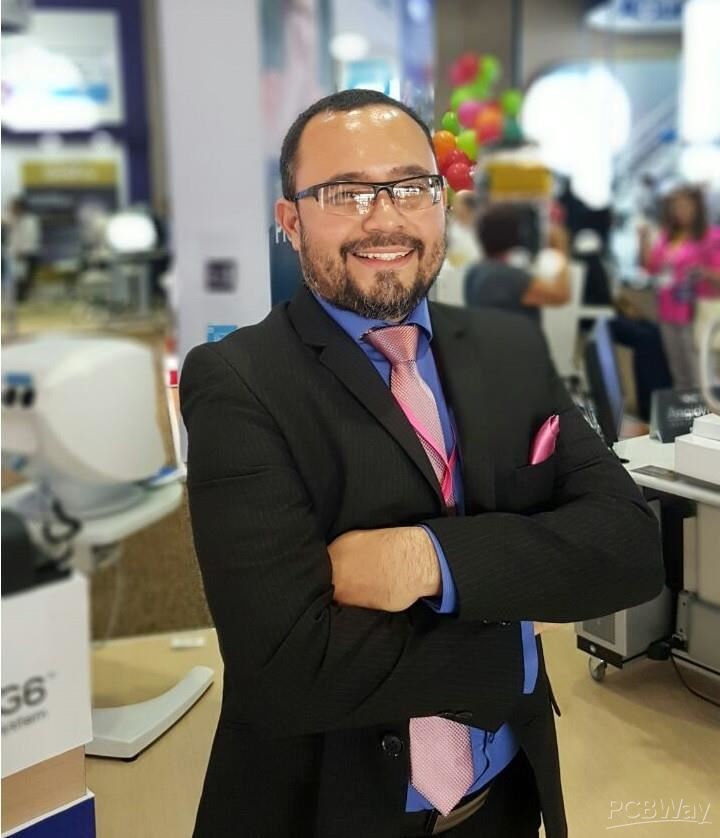
-
7design
-
7usability
-
6creativity
-
6content
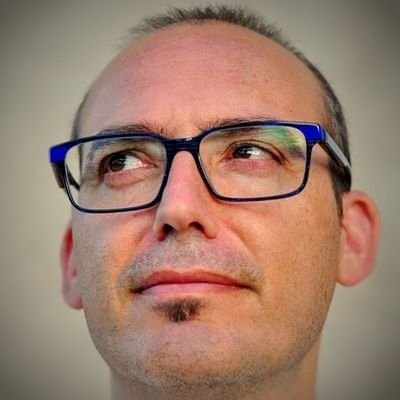
-
8design
-
10usability
-
9creativity
-
8content
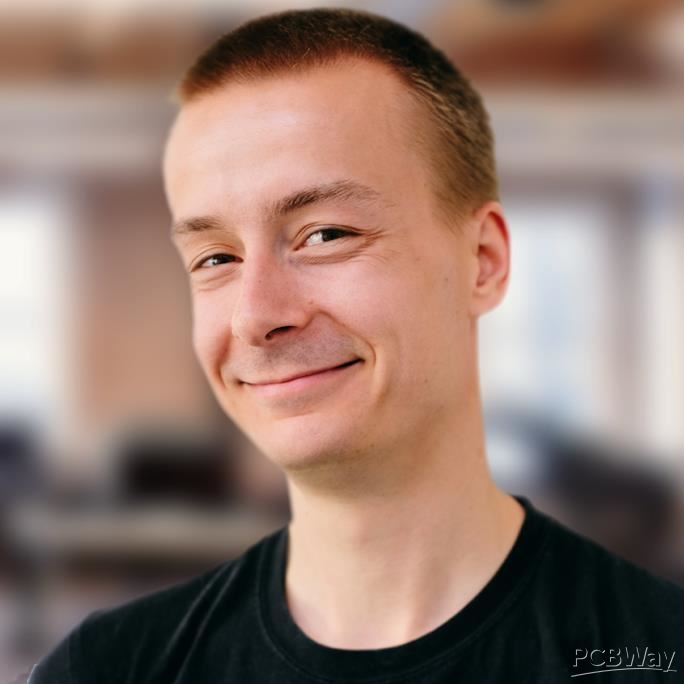
-
9design
-
10usability
-
6creativity
-
8content
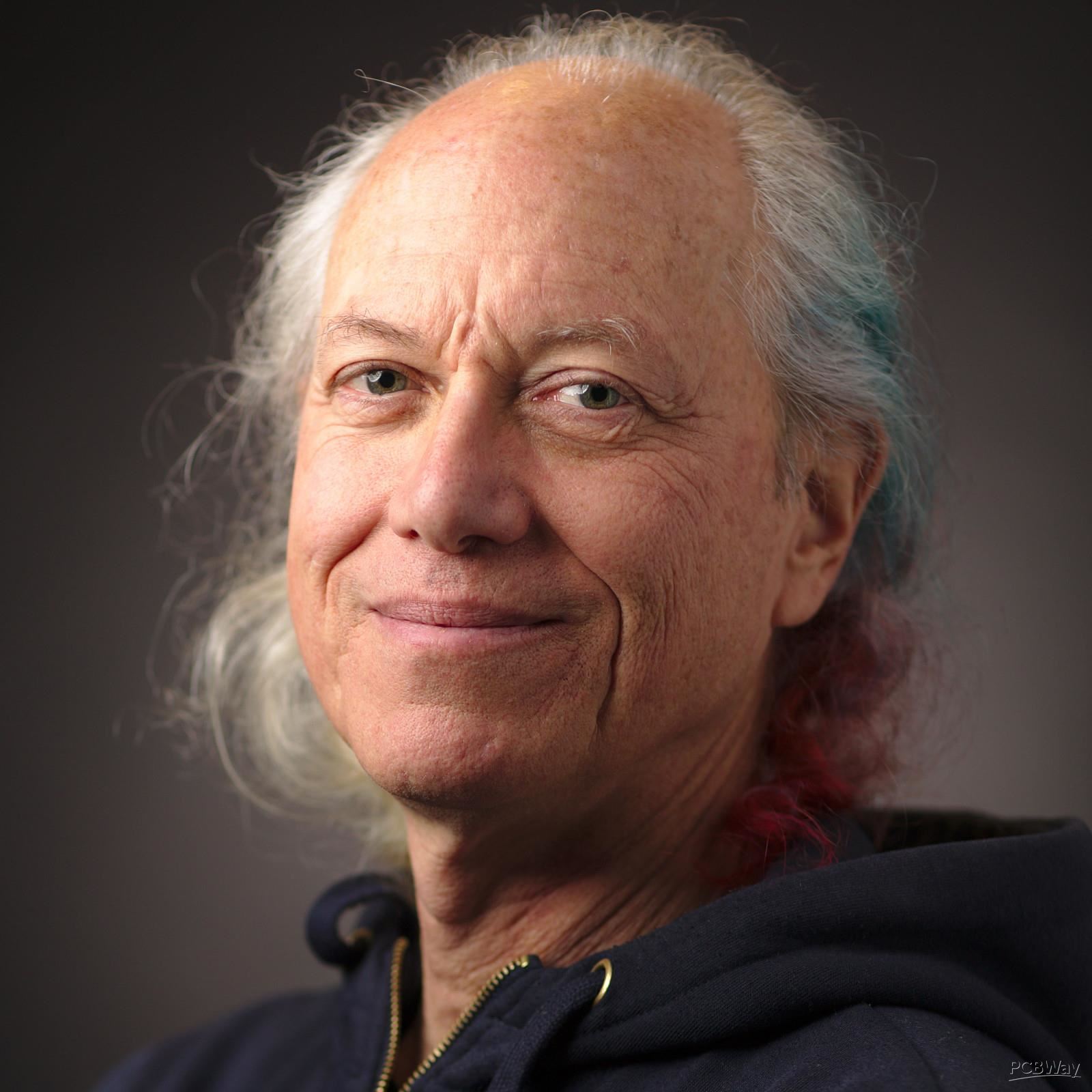
-
8design
-
6usability
-
7creativity
-
5content
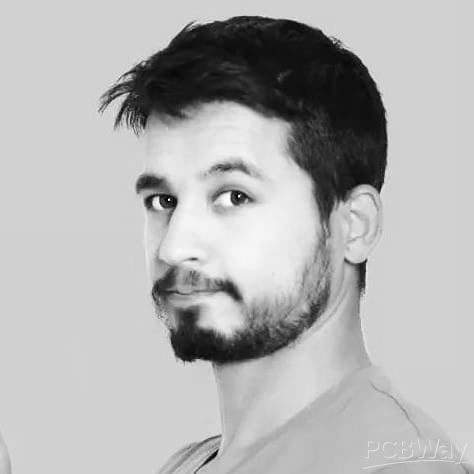
-
9design
-
9usability
-
8creativity
-
9content
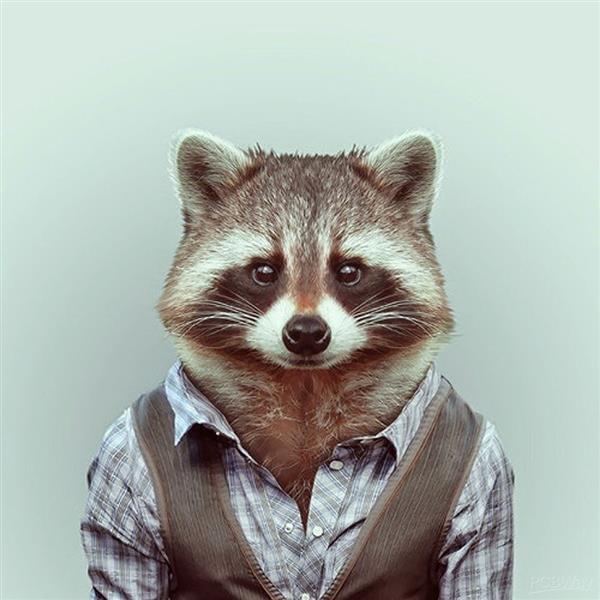
-
10design
-
10usability
-
10creativity
-
10content
More by Ilya
-
Commodore 64 1541-II Floppy Disk Drive C64 Power Supply Unit USB-C 5V 12V DIN connector 5.25
149 1 2 -
Easy to print simple stacking organizer with drawers
82 0 0 -
-
-
-
Modifying a Hotplate to a Reflow Solder Station
1126 1 6 -
MPL3115A2 Barometric Pressure, Altitude, and Temperature Sensor
632 0 1 -
-
Nintendo 64DD Replacement Shell
489 0 2 -
V2 Commodore AMIGA USB-C Power Sink Delivery High Efficiency Supply Triple Output 5V ±12V OLED display ATARI compatible shark 100W
1424 4 3
Hi! Yes, controller have algorithm charge for lead-acid, AGM, GEL, li-ion, LiFePo4, LTO.