![]() |
KiCADKicad
|
|
![]() |
FreeCad |
|
|
GRBL firmware |
Thor ControlPCB
ControlPCB is the board used in the Thor project to control the stepper motors that drive the robotic arm.
This board is based on RAMPS 1.4 and acts as a shield for an Arduino Mega, supporting up to 8 stepper drivers (A4988 and compatible). It also supports up to 8 endstops (1 per motor) and a pwm output to control the robot tool. It also has 5V and 12V auxiliary rails.
You can check the BOM here and you can find the source files of this board in its GitHub repository.
Thor is an Open Source and printable robot arm with six degrees of freedom. Its configuration (yaw-roll-roll-yaw-roll-yaw) is the same used by most of the manipulator robots on the market. In its extended position, Thor is about 625mm high and can lift loads up to 750 grams.
The main purpose of this project was to design a robot that could be used in universities and schools to teach robotics.With this in mind, the design had to be affordable and accessible. Releasing the source files and doing so under an open source licence was the best option: anyone could study any element of the robot in depth and, moreover, modify or adapt it to their needs.
The cost of the whole materials is under 350€. Being so affordable, I think almost every school/university/maker could make good use of at least one!
In terms of licenses, I wanted this project to be Open Source because I want anyone to have the opportunity to study, modify and improve it.
Thor has been developed using only open source tools: FreeCAD for the 3D modeling, KiCAD for the PCB design and GBRL as firmware for the control electronics. In this way, access to knowledge can be guaranteed to anyone, anywhere, without any economic cost. There is not a single reason for not hacking Thor!
If you want to know more about this project, visit the Thor Website, where you will find documentation, manuals and a forum to solve all your doubts.
Hope you like it!
ángel LM
Thor ControlPCB
*PCBWay community is a sharing platform. We are not responsible for any design issues and parameter issues (board thickness, surface finish, etc.) you choose.
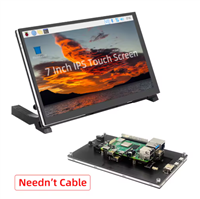
Raspberry Pi 5 7 Inch Touch Screen IPS 1024x600 HD LCD HDMI-compatible Display for RPI 4B 3B+ OPI 5 AIDA64 PC Secondary Screen(Without Speaker)
BUY NOW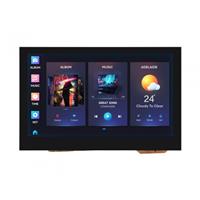
ESP32-S3 4.3inch Capacitive Touch Display Development Board, 800×480, 5-point Touch, 32-bit LX7 Dual-core Processor
BUY NOW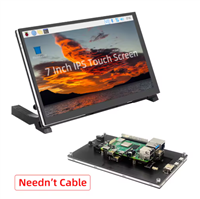
Raspberry Pi 5 7 Inch Touch Screen IPS 1024x600 HD LCD HDMI-compatible Display for RPI 4B 3B+ OPI 5 AIDA64 PC Secondary Screen(Without Speaker)
BUY NOW- Comments(8)
- Likes(12)
- 6 USER VOTES
- YOUR VOTE 0.00 0.00
- 1
- 2
- 3
- 4
- 5
- 6
- 7
- 8
- 9
- 10
- 1
- 2
- 3
- 4
- 5
- 6
- 7
- 8
- 9
- 10
- 1
- 2
- 3
- 4
- 5
- 6
- 7
- 8
- 9
- 10
- 1
- 2
- 3
- 4
- 5
- 6
- 7
- 8
- 9
- 10

-
10design
-
10usability
-
10creativity
-
10content
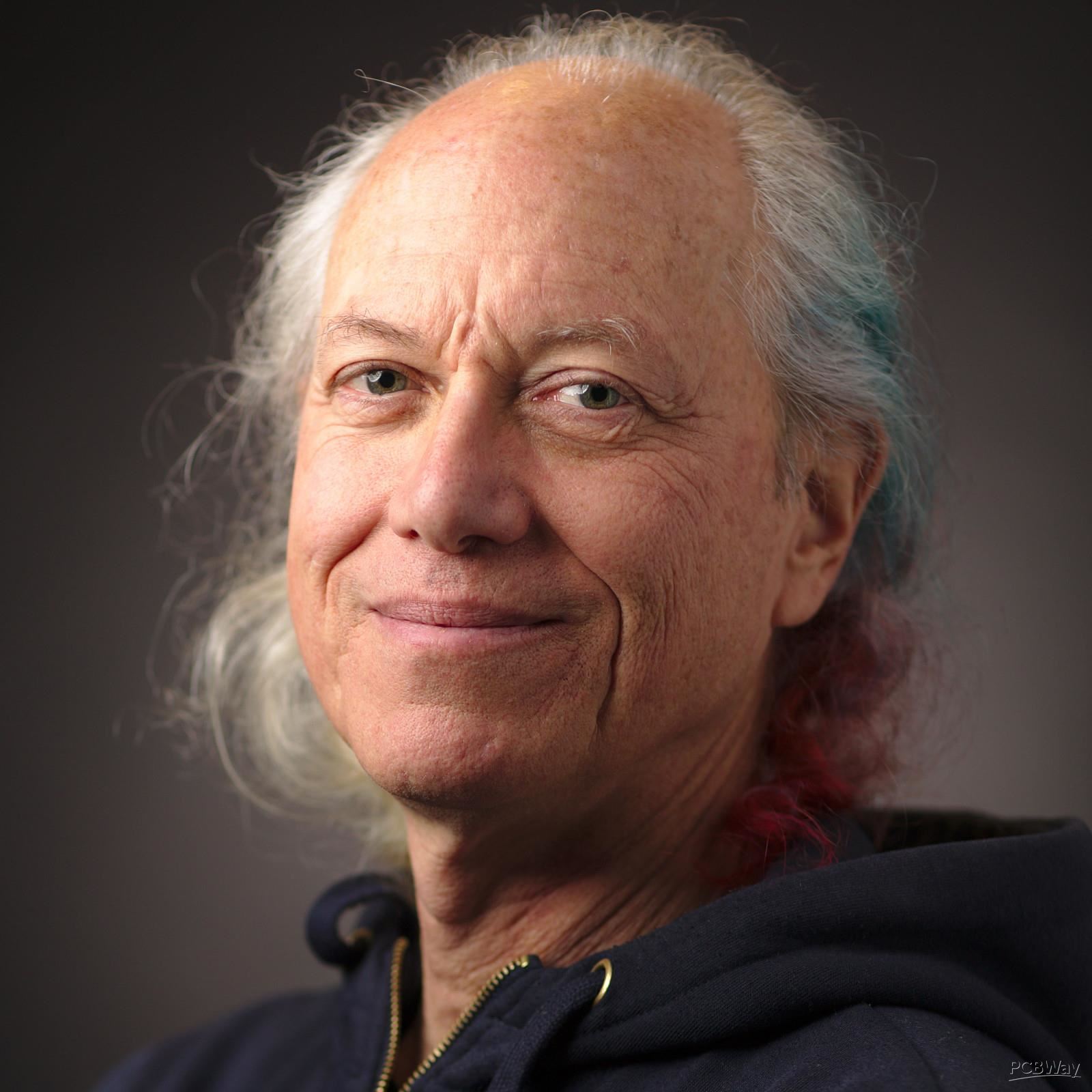
-
9design
-
9usability
-
9creativity
-
10content

-
10design
-
10usability
-
10creativity
-
10content

-
8design
-
9usability
-
7creativity
-
10content

-
9design
-
10usability
-
10creativity
-
10content

-
10design
-
10usability
-
10creativity
-
10content
More by Angel LM
-
-
Commodore 64 1541-II 1581 Floppy Disk Drive C64 Power Supply Unit USB-C 5V 12V DIN connector 5.25
171 1 3 -
Easy to print simple stacking organizer with drawers
88 0 0 -
-
-
-
Modifying a Hotplate to a Reflow Solder Station
1141 1 6 -
MPL3115A2 Barometric Pressure, Altitude, and Temperature Sensor
641 0 1 -
-
Nintendo 64DD Replacement Shell
497 0 2 -
V2 Commodore AMIGA USB-C Power Sink Delivery High Efficiency Supply Triple Output 5V ±12V OLED display ATARI compatible shark 100W
1446 4 3
my question too!!!
Our assembled board is shown in the picture below for your reference.
PDIG1 should be a 2x18 Male header. As it can be seen in the photos, the pins should be mounted on the back layer, and soldered on the front layer.
Special attention should be paid to one of the pins, which should be unsoldered and a wire soldered in its place. The pin in question can be seen in the Wiring Diagram, marked in red and is the one that connects to pin 7 of the Arduino Mega.
Thanks for your feedback. we get it.