![]() |
PIC16F1503T-I/SLMicrochip Technology
|
x 1 | |
![]() |
UJC-HP-3-SMT-TRCUI Devices
|
x 1 | |
![]() |
NR10050T150MTaiyo Yuden
|
x 1 | |
![]() |
IRLML6344TRPBFInfineon / IR
|
x 1 | |
![]() |
CMS01Toshiba
|
x 1 |
![]() |
KiCADKicad
|
|
![]() |
MPLAB X IDEMicrochip Technology
|
HOWICO: USB-powered Foam-cutter/Sealer controller
Features
- Replacing C/AA batteries with HOWICO allows Hot Wire Foam Cutters to cut foams faster or cut other materials (e.g. polypropylene). Similarly, Handy Heat Sealers can seal speedy or weld thicker films.
- The size of HOWICO is compatible with one C battery or two AA batteries.
- Powered from USB PD power banks or chargers, no need for disposable batteries
- One-button heater power control and indicators with three LEDs
- The initial state is the Lowest power mode (equivalent to C/AA batteries). Each time you click the button, the heater power mode steps up (up to the Highest power mode). When you press the button for at least 3 seconds, the power mode turns to Lowest.
- PIC16F1503 MCU controls the heater power in the programmed range.
- You can modify the program: power control range, button commands, indicators patterns, etc.
- You can also make your hot wire cutters at home with HOWICO.
Hot Wire Foam Cutters
with one C battery
Replacing with HOWICO
You can also make your hot wire cutters at home with HOWICO.
Handy Heat Sealers
with two AA batteries
with HOWICO
Let's make HOWICO
How designed and works HOWICO
Form factor
- 45mm x 25mm board size makes HOWICO fit battery holders for one C or two AA batteries.
- Right-angle pin headers with additionally bending make mate with battery holder terminals.
- The gouged shape of the board allows the tip of the USB cable to fit into the battery holder.
Electric power and its control
Using the USB Type-C connector and suitable USB PD power banks or chargers, we can consume up to 5V 3A: 15W power. It is strong enough for C Battery-powered foam cutters or AA battery-powered sealers. (Our targets need no more electric power, although many USB PD power sources can supply 9V 3A: 27W or more)
If we connect the 5V power supply to the heater of the cutter or sealer directly, the current and power will be too large. So we control the power with pulse width modulation(PWM).
Determining the power control circuit
We use a field-effect transistor (FET) for the principal switching device of PWM.
When the FET turns on, the current from the power supply flows through the heater and the FET. In this case, because of the low resistance of the heater, the current quickly rises and becomes too large.
By inserting an inductor into the current path, it suppresses the current rising rate.
In addition, by adding a diode between the FET's drain and the heater's high-side, when the FET turns off, the current flows the inductor and the heater bypath into the diode path and continues. This movement helps reduce electrical and acoustic noise. In the absence of the bypass device, the inductance causes the FET drain voltage rasing very high, damaging the FET.
Parts and their specification selection
Microcontroller Unit (MCU)
5 V power supply capable: No regulators needs and higher output voltage than 3.3 V operated one.
With PWM (as a hardware peripheral)
One Input for a switch
Outputs for LED indicators
We select PIC16F1503.
FET
Continuous Drain Current: ID: >3 A
Gate-to-Source Voltage: VGS to gate on: < 4 V
Static Drain-to-Source On-Resistance: RDS(ON): <100 mOhms: It needs well lower than the resistance of the heater (about 1 Ohm)
Maximum Power Dissipation (PD): It needs well higher than the actual power dissipation (the product of the current and the on-resistance).
We select IRLML6344TRPbF.
Serial resister to the FET gate
It is a trade-off between gate driver current and switching speed.
The FET gate is a capacitive load for the gate driver (MCU's PWM output). Therefore, a serial resistor is needed to limit the current.
On the other hand, the switching transition time is proportional to the time constant (product of the series resistance and the gate capacitance), and a longer transition time causes higher switching loss.
The MCU port's output current needs to meet the recommendation and ratings.
We select 270 ohms: the output current of the gate driver port has a margin for the recommended value of 25mA, including the pull-down resistor described later.
Pull-down resistor for the FET gate
We should pull down the PWM output port (FET gate) to avoid turning on the FET before configuring the port.
We select 1 k ohms that the voltage division between the pull-down resistor and the port's internal pull-up is below the Gate Threshold Voltage of the FET gate.
Inductor
Rated Current -Saturation Current: >3 A
Rated Current -Temperature Rise Current: >3 A
DC Resistance: < 100 mA: It needs well lower than the resistance of the heater (about 1 Ohm)
Inductance: Larger inductance is better after satisfying the above conditions
We select NR10050T150M: 15 uH
Diode
Average forward current: IF(AV): >2 A
(Because the diode current flow during the off-time of the FET, its average current will be lower than the FET's one)
Peak forward voltage: VFM: < 0.5 V: Lower VFM is better: We select Schottky Barrier Diode CMS01.
Determining PWM frequency
Higher PWM frequencies smooth the current with inductance. On the other hand, it increases the ratio of switching transition time to the period, then the switching loss (heat generation) increases, and power control accuracy decreases. In the current HOWICO design, 80 kHz is a good trade-off.
Circuit work waveforms of HOWICO
With a lower PWM duty ratio (30%), the peak voltage drop by the heater is lower. It indicates that the inductor is correctly suppressing the current rising rate.
With a higher PWM duty ratio(80%), the voltage drop by the heater is higher. It indicates that the PWM duty ratio controls the heater power properly.
The fluctuation of the power supply voltage becomes higher when the PWM duty ratio is high. It is due to the followability of the power bank and the voltage drop of the USB cable.
HOWICO: USB-powered Foam-cutter/Sealer controller
*PCBWay community is a sharing platform. We are not responsible for any design issues and parameter issues (board thickness, surface finish, etc.) you choose.
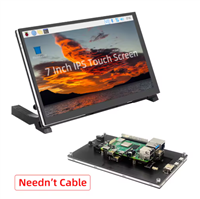
Raspberry Pi 5 7 Inch Touch Screen IPS 1024x600 HD LCD HDMI-compatible Display for RPI 4B 3B+ OPI 5 AIDA64 PC Secondary Screen(Without Speaker)
BUY NOW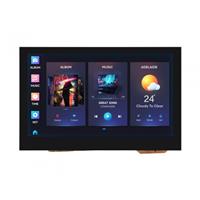
ESP32-S3 4.3inch Capacitive Touch Display Development Board, 800×480, 5-point Touch, 32-bit LX7 Dual-core Processor
BUY NOW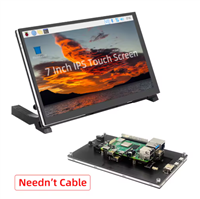
Raspberry Pi 5 7 Inch Touch Screen IPS 1024x600 HD LCD HDMI-compatible Display for RPI 4B 3B+ OPI 5 AIDA64 PC Secondary Screen(Without Speaker)
BUY NOW- Comments(0)
- Likes(1)

-
Nachtele Sep 15,2021
- 1 USER VOTES
- YOUR VOTE 0.00 0.00
- 1
- 2
- 3
- 4
- 5
- 6
- 7
- 8
- 9
- 10
- 1
- 2
- 3
- 4
- 5
- 6
- 7
- 8
- 9
- 10
- 1
- 2
- 3
- 4
- 5
- 6
- 7
- 8
- 9
- 10
- 1
- 2
- 3
- 4
- 5
- 6
- 7
- 8
- 9
- 10
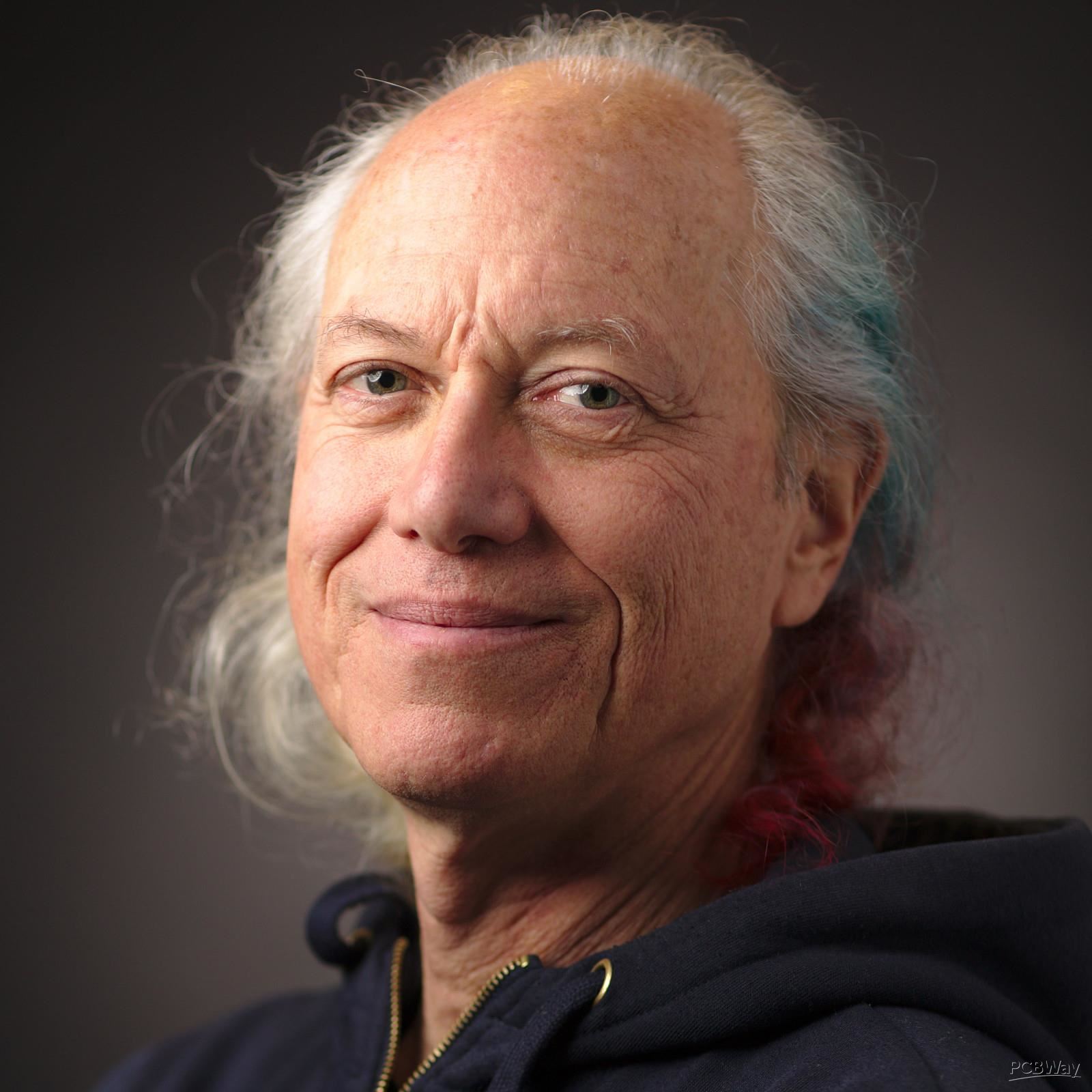
-
9design
-
9usability
-
9creativity
-
8content
More by Nachtele
-
-
-
Modifying a Hotplate to a Reflow Solder Station
944 1 6 -
MPL3115A2 Barometric Pressure, Altitude, and Temperature Sensor
477 0 1 -
-
Nintendo 64DD Replacement Shell
410 0 2 -
V2 Commodore AMIGA USB-C Power Sink Delivery High Efficiency Supply Triple Output 5V ±12V OLED display ATARI compatible shark 100W
1182 4 2 -
How to measure weight with Load Cell and HX711
731 0 3