Power supply 22V 2,5A Atmega8 Control Board
This is control board No. 1, you need a second board to assemble the device.
A good, reliable and easy to use bench power supply unit is probably the most important and most used device in every electronic lab.
A proper electronically stabilized bench power supply unit is an important but also expensive device. Using a microcontroller based design we can build a power supply which has a lot of extra features, is easy to build and very affordable.
The basic electrical design idea
A common misconception about a digital power supply is that people assume everything to be digital and don't understand how this could possibly work with a circuit based on a microcontroller. We want a clean and stable analog voltage as output and for this we use analog components. Only analog components are fast enough to remove ripples due to load changes or any remaining 50/60Hz noise.
The emitter voltage on a transistor is related to the voltage on the base and not the input voltage on the collector. The main current flows however from C to E. This simple circuit produces a clean DC voltage. It removes noise coming in through the collector pin and controls load changes on the emitter side.
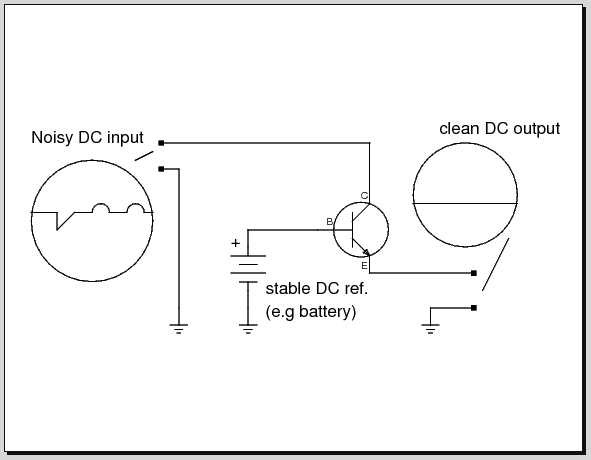
In other words our digital power supply has a completely analog control system for fast respose to load and voltage changes and we overlay a second digital control system for the more fancy features that a bench top power supply needs. Let's remove the battery from that circuit and build the simplest possible electronically stabilized power supply. It consists of 2 basic parts: a transistor and a reference voltage generated with a Z-diode.
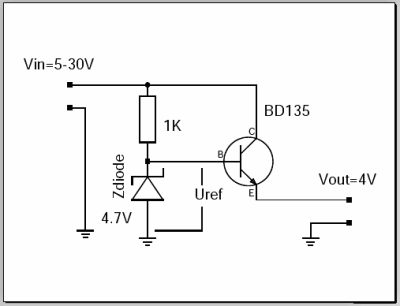
The output voltage of this circuit is Uref - 0.7V. The 0.7V is approximately the voltage drop between B and E on the transistor. The Z-diode and the resistor generate a reference voltage which is stable, even if the input fluctuates and is noisy. The transistor is needed to handle higher currents than the Z-diode and resistor alone can provide. In this configuration the transistor just amplifies the current. The current which the resistor and Z-diode need to provide is the output current divided by hfe (hef is a number which you can lookup in the datasheet of the transistor).
What are the problems with this circuit?
The transistor will die when there is a short circuit on the output.
It provides only a fixed output voltage.
These are quite severe limitations which make this circuit unusable but this circuit is still the basic building block of all electronically regulated power supplies.
To overcome those problems you need some "intelligence" which will regulate the current on the output and a variable reference voltage. That's all (... and this makes the circuit much more complex).
For the last few decades people have used operational amplifiers to provide this intelligence. Operational amplifiers can basically be used as analog calculators to add, subtract, multiply or logically "or" voltages and currents.
Today microcontrollers are so fast that all this can easily be done in software. The beauty is that you get as a side effect a voltmeter and an amperemeter for free. The control loop in the microcontrollers has to know voltage and current values anyhow. You just need to display them. What we need from the microcontroller are:
A AD-converter to measure voltage and current all the time
A DA-converter to drive our power transistor (provide the reference voltage)
The problem is that the DA-converter needs to be very fast. If there is a short circuit detected on the output then we must immediately reduce the voltage on the basis of the transistor otherwise it will die. Fast means within milliseconds (as fast as an operational amplifier).
The ATmega8 has an AD-converter which is more than fast enough but it has at first glance no DA-converter. It is possible to use pulse width modulation (PWM) and an analog low pass filter to get an DA-converter but PWM alone is much too slow to implement the short circuit protection in software. How to build a fast DA-converter?
The R-2R ladder
There are many ways to build a digital to analog converter but we need a fast and cheap one which can easily interface to our microcontroller. There is a DA-converter circuit known as "R-2R ladder". It consists of resistors and switches only. There are two types of resistors. One with the value R and one with twice the value of R.
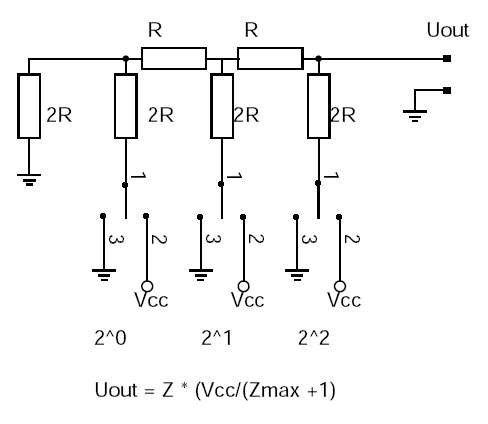
The above shows a 3 bit R2R-DA-converter. The control logic moves the switches between GND and Vcc. A digital "one" connects the switch to Vcc and a digital "zero" to GND. What does this circuit do? It provides voltages in steps of Vcc/8. In general the output voltage is Z * (Vcc/(Zmax+1) where Z is the digital number. In the case of a 3 bit AD converter this is: 0-7.
The inner resistance of the circuit as seen from the output is R.
Instead of using separate switches we can connect the R-2R ladder to the microcontroller output lines.
Generating a variable DC signal with PWM (pulse width modulation)
Puls width modulation is a method where you generate pulses and run them thru a low pass filter with a cut off frequency much lower than the pulse frequency. This results in a DC signal and the voltage depends on the width of those pulses.
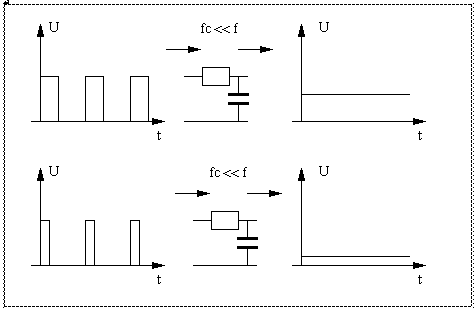
Using PWM to generate a variable DC voltage.
The atmega8 provides in hardware 16bit PWM. That is: you could theoretically have a 16bit DAC with just very few components. In order get a true DC signal out of a PWM signal one has to average it out using a filter and that can be a problem at high resolutions. The more accuracy you have the lower the frequency of the PWM signal. This again means you need big capacitors and the response time is very slow. The first and second generation of the digital DC power supply had a 10bit R2R-ladder DAC. That is: the output could be set in 1024 step. If you run the atmega at 8MHz and use a 10bit PWM DAC then the PWM signal pulses have a frequency of 8MHz/1024=7.8KHz. To get a somewhat good DC signal out of this you need to filter it with a second order low pass filter of 700Hz or less.
You can imagine what happens if you use 16bit PWM. 8MHz/65536=122Hz. One would need a 12Hz low pass.
Combining R2R-ladder and PWM
It is possible to combine the idea of the PWM and the R2R-ladder. In this design we will use a 7bit R2R-ladder combined with a 5bit PWM signal. With a 8MHz system clock and 5bit resolution we will get a 250KHz signal. 250KHz can even be converted with small capacitors into a DC signal.
The original version of the tuxgraphics digital DC power supply had a 10bit DAC based on the R2R ladder. In this new design we use R2R-ladder and PWM with a total resolution of 12bit.
Oversampling
At the expense of some processing time one can increase the resolution of an analog to digital converter (ADC). This is called oversampling.
Four fold oversampling results in double resolution. That is: 4 consecutive samples can be used to get twice as many steps on the ADC. The theory behind oversampling is explained in the PDF document which you can find at the end of this article. We use oversampling for the voltage control loop. For the current control loop we use the original resolution of the ADC as fast response times are here more important than resolution.
A more detailed design
So here is now a more detailed design of the above circuit.
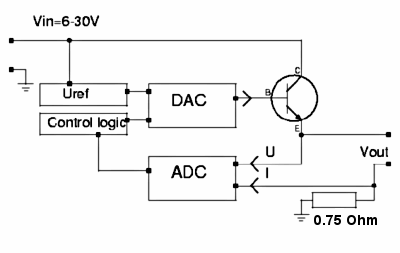
A few technical details are still missing:
The DAC (digital to analog converter) can not provide the current to drive the power transistor
The microcontroller operates at 5V so the maximum output of the DAC is 5V which means that the maximum output voltage behind the power transistor will be 5-0.7=4.3V .
To fix this we must add amplifiers for current and voltage.
Adding an amplifier stage to the DAC
When adding amplifiers we must keep in mind that those must work with large signals. Most amplifier designs (e.g for audio) are done under the assumption that the signals will be small compared to the supply voltage. So forget all the classic books about transistor amplifier design.
We could use operational amplifiers but those would require extra positive and negative supply voltages which we want to avoid.
There is also the additional requirement that the amplifier must go from zero voltage to a stable state without oscillating. In words there must not be any short oscillation or output peek when you switch on the power supply.
The below circuit shows an amplifier stage which is suitable for this purpose.
We start with the power transistor. We use a BD245 (Q1). According to the datasheet this transistor has a hfe=20 at 3A output. It will therefore draw about 150mA on the basis. To amplify the current we use a configuration known as "Darlington transistor". For this we put a medium power transistor in front. Those have typically a hfe value of 50-100. This will reduce the current needed to less than 3mA (150mA / 50). 3mA are manageable with small signal transistors like BC547/BC557. Those small signal transistors are then very good for building a voltage amplifier.
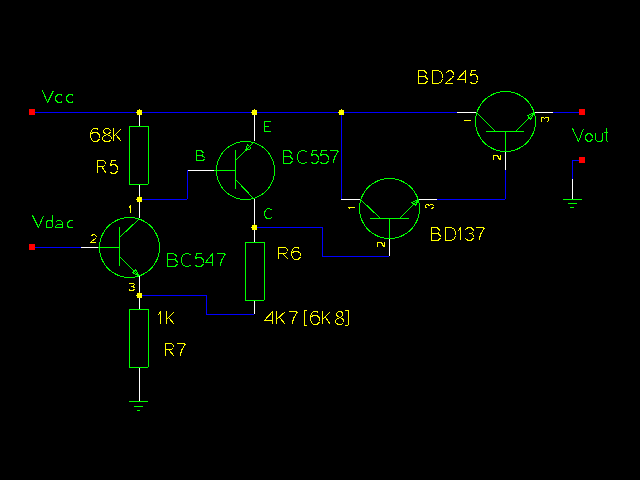
For 30V output we must at least amplify the 5V from the DAC by a factor of 6. For this we combine a PNP and an NPN transistor as shown above. The voltage amplification factor of this circuit is:
Vampl= (R6 + R7)/R7
The power supply shall be available in 2 version: Max 30 output and max 22V output. A combination of 1K and 6.8K gives a factor of 7.8 which is good for the 30V version and has some room for possible losses due to higher currents (our formula is linear. The reality is non-linear). For the 22V version we use 1K and 4.7K.
The inner resistance of the circuit as seen on the Basis of BC547 is:
Rin=hfe1 * S1 * R7 * R5 = 100 * 50 * 1K * 47K = 235 MOhm - hfe is about 100 to 200 for a BC547 transistor - S is the slope of the amplification curve of a transistor and is about 50 [unit=1/Ohm]
This is more than high enough for the connection to our DAC which has a inner resistance of 5K.
The inner equivalent output resistance is:
Rout= (R6 + R7) / (S1 + S2 * R5 * R7) = about 2 Ohm
Low enough to drive the following transistor Q2.
R5 ties the basis of BC557 to the emitter which means "off" for the transistor until the DAC and BC547 come up. R7 and R6 tie the Basis of Q2 initially to ground which shuts the output darlington stage down.
In other words every component in this amplifier stage is initially off. This means we will not get from those transistors any oscillations or output peeks at power on or power off. A very important point. I have seen expensive industrial power supplies which produced a voltage peek at power off. Such a power supply is definitely to be avoided as it can easily kill sensitive circuits.
Power sources
You can either use a transformer, rectifier and big capacitors or you can try to get a 32/24V laptop power supply. I went for the later option. Those laptop power supply "bricks" are sometimes sold very cheap (over stock) and some of them provide 70W at 24V or even 32V DC.
Most people will probably go for a transformer because those are very easy to get.
22V 2.5A version: you need a 18V 3A transformer, a rectifier and a 2200uF or 3300uF capacitor. (reason: 18 * 1.4 = 25V) 30V 2A version: you need a 24V 2.5A transformer, a rectifier and a 2200uF or 3300uF capacitor. (reason: 24 * 1.4 = 33.6V) It does not harm to buy a transformer which can provide more ampere. A power diodes bridge with 4 diodes which are specified for a low voltage drop (e.g BYV29-500) gives a good rectifier.
You can also use a "heavier" transformer.
Check your circuit for proper insulation. Make sure that it is not possible to touch any part that may carry 110V/230V even when the case is open. Connect all metal parts of the chassis to earth (not to GND of the circuit).
Transformers and laptop power supply bricks
If you want to use two or more power supplies in a chain to get positive and negative voltages for your circuit then it is important that the transformer is really insulated. Be careful with laptop power supply bricks. They are nice and small but some of them may connect the minus pin on the output to the earth pin on the input. This will then cause a short ciruit via the earth wire if you use two power supplies in a chain.
Other voltages and current limits
The two provided configurations are 22V 2.5A and 30V 2A. If you want to build a version with other (lower) output voltages or current limits then just edit the hardware_settings.h file.
Example: To build a 18V 2.5A version you just edit the hardware_settings.h file and change the maximum output voltage to 18V.
You can then use a 20V 2.5A power source.
Example: To build a 18V 1.5A version you just edit the hardware_settings.h file and change the maximum output voltage to 18V and the max. current to 1.5A.
You can then use a 20V 1.5A power source.
Testing
The last component to solder to the board should be the microcontroller. Before you insert it I would recommend to do some basic hardware tests:
Test1: Connect some power supply (at least 10V) to the power input of the circuit and check that you get 5V DC behind the voltage regulator.
Test2: Measure the output voltage. It should be 0V (or near zero, e.g 0.15V, and it will go to zero if you put a "load" of 2K to 5K on the output.)
Test3: Solder the microcontroller to the board and load the LCD test software by running the commands in the directory of the unpacked digitaldcpower tar.gz package.
make test_lcd.hex make load_test_lcd
You should see "LCD works" on the display.
Now you can load the final software.
A word of warning for further testing with the final software: Be careful with short circuits until you have tested the current limitation function. A save way to test the current limitation is to use a low Ohm resistor, e.g a car bulb.
Set a low current limit, e.g 30mA at 10V. You should see the voltage go down immediately to almost zero once you connect the bulb on the output. There is still a fault in the circuit if it does not go down. The car bulb will protect the power supply circuit even if there is a fault as it is not a full short circuit.
The software
This section will give you insights as to how the software works and you can use the knowledge to do modifications. However be aware that the short circuit protection is also only software. If you make a mistake somewhere then this protection may not work. If you cause then a short circuit on the output your hardware may go off in a cloud of smoke. To avoid this you should use a 12V car bulb (see above) to test the short circuit protection.
Now a bit about the software structure. First look at the main program (file main.c, download at the end of this article) you will see that there are only a few lines of initialization code executed at power on and then the software enters an endless loop.
There are really 2 endless loops in this software. One is the main loop ("while(1){ ...}" in file main.c) and the other one is the periodic interrupt from the Analog the Digital Converter (function "ISR(ADC_vect){...}" in file analog.c). During initialization the interrupt is configured to execute every 104μ Sec. All functions and code that is executed runs in the context of one of those tasks (task the name for a process or thread of execution in a real time OS, so I use this word here even if there is no OS).
![[priorities]](http://www.tuxgraphics.org/common/images2/article10051/tasks.gif)
The interrupt task can stop the execution of the main loop at any time. It will then execute without being interrupted and then execution continues again in the main loop at the place where it was interrupted. This has two consequences:
The code in the interrupt must not be too long as it must finish before the next interrupt comes. What counts here are the amount of instructions in machine code. A mathematical formula, which can be written as just one line of C-code may result in hundreds of lines of machine code.
Variables that you share between interrupt code and code in the main task may suddenly change in the middle of execution.
All this means that complex things like updating of the display, checking of push buttons, conversion of ampere and volt values to internal units etc ... must be done in the main task. In the interrupt we execute only things that are time critical: Current and voltage control, overload protection and setting of the DAC. To avoid complex mathematics all calculations in the interrupt are done in ADC units. That is the same units that the ADC produces (integer values from 0...1023 for current and 0..2047 for voltages).
This is the basic idea of the software. I will also explain what you find in which files and then you should be able to understand the code (given that you are familiar with C).
Software: Which file contains what
main.c -- this file contains the main program. All initialization is done from here.here. The main loop is also implemented here. analog.c -- the analog to digital converter and everything that runs in the context of the interrupt task can be found here. dac.c -- the digital to analog converter. Initialized from ddcp.c but used only from analog.c kbd.c -- the keyboard code lcd.c -- the LCD driver. This is a special version which will not need the RW pin of the display. It uses instead an internal timer which should be long enough for the display to finish its task.
Loading and using the software
To load the software into a microcontroller you need a programmer such as the avrusb500. You can download the ziped software archives at the end of the article.
Edit the file hardware_settings.h and adjust it according to the hardware. Here you can also do calibrations of voltmeter and amperemeter. The file is well commented.
gedit hardware_settings.h
Connect the programmer cable and power on the circuit. Then run:
make fuse This will set the clock frequency of the microcontroller to 8MHz. The software is designed for this frequency. make This will compile the software. make load This will load the software.
The buttons
The power supply has 4 button for local control of voltage and max. current. The 5-th button is to store the settings permanently in an eeprom such that it will come up with identical settings the next time you power it on.
![[buttons]](http://www.tuxgraphics.org/common/images2/article10051/buttons.gif)
The local control button pad.
With U+ you can increase the voltage and with U- you decrease it. When you hold the button then it will step and after a while "run" faster to make it easy to change the voltage in large steps. The I+ and I- buttons work the same way.
The display
This is how the display looks like:
![[display]](http://www.tuxgraphics.org/common/images2/article10051/display.png)
The fields in the LCD display area. The real measured values and the set values are always shown at the same time.
The arrow on the right indicates that currently the configured voltage is the limiting factor. Should a short circuit occur on the output or the connected device draws more current then the arrow will flip to the bottom line and indicate that the configured max. current has become the limiting factor.
Power supply 22V 2,5A Atmega8 Control Board
*PCBWay community is a sharing platform. We are not responsible for any design issues and parameter issues (board thickness, surface finish, etc.) you choose.
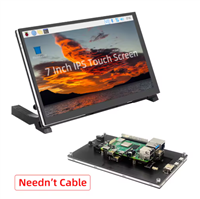
Raspberry Pi 5 7 Inch Touch Screen IPS 1024x600 HD LCD HDMI-compatible Display for RPI 4B 3B+ OPI 5 AIDA64 PC Secondary Screen(Without Speaker)
BUY NOW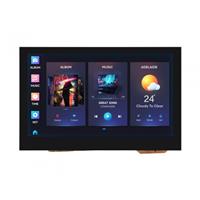
ESP32-S3 4.3inch Capacitive Touch Display Development Board, 800×480, 5-point Touch, 32-bit LX7 Dual-core Processor
BUY NOW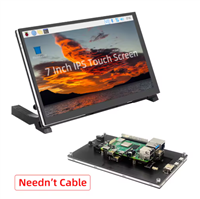
Raspberry Pi 5 7 Inch Touch Screen IPS 1024x600 HD LCD HDMI-compatible Display for RPI 4B 3B+ OPI 5 AIDA64 PC Secondary Screen(Without Speaker)
BUY NOW- Comments(0)
- Likes(7)

-
Zoran Nikolic Jan 30,2024
-
Kayumov Marsel Kavievich Dec 26,2020
-
VA Aug 09,2020
-
NOEL benoit Sep 18,2019
-
Valerii Drobot Sep 06,2019
-
Engineer Feb 27,2019
-
Visalom Gheorghe Jan 04,2019
- 5 USER VOTES
- YOUR VOTE 0.00 0.00
- 1
- 2
- 3
- 4
- 5
- 6
- 7
- 8
- 9
- 10
- 1
- 2
- 3
- 4
- 5
- 6
- 7
- 8
- 9
- 10
- 1
- 2
- 3
- 4
- 5
- 6
- 7
- 8
- 9
- 10
- 1
- 2
- 3
- 4
- 5
- 6
- 7
- 8
- 9
- 10

-
1design
-
2usability
-
3creativity
-
10content

-
1design
-
1usability
-
1creativity
-
1content

-
10design
-
10usability
-
10creativity
-
10content

-
10design
-
10usability
-
10creativity
-
10content

-
10design
-
9usability
-
8creativity
-
1content
More by Vasiliy Semerenko
-
RTL-SDR resiver Не просто очередная беглая статья о модификации тюнера, а подробный мануал о том, как это делается, ...
-
GSM Control and Alarm Sustem Sim300DZ, Sim900D Устройство управления и контроля на протяжении длительного времени пользуется большой популярностью ...
-
ESR_LCFv3_miron63 Ссылка на форум
-
Soldering station ### DESCRIPTION### TECHNICAL DETAILS / COMPONENTS### LEARN / TOPIC / BUILD INSTRUCTIONS
-
PROEKT ### DESCRIPTION### TECHNICAL DETAILS / COMPONENTS### LEARN / TOPIC / BUILD INSTRUCTIONS
-
Solderind station ### DESCRIPTION### TECHNICAL DETAILS / COMPONENTS### LEARN / TOPIC / BUILD INSTRUCTIONS
-
USB Осциллограф клон instrustar isds205A плата от ZuuM, Clon 205 oscill https://youЧастота сигнала 12мГцДва каналаСуть такова, я уже писал о выборе цифрового осциллографа т...
-
CW KEYER ps/2 attiny2313, Christmas2019 Для многих радиолюбителей стало привычным делом, работая телеграфом, использовать для генерации кода...
-
CW Coder Ps/2 ### DESCRIPTION### TECHNICAL DETAILS / COMPONENTS### LEARN / TOPIC / BUILD INSTRUCTIONS
-
Power supply 22V 2,5A Main Board This is the control board number 2, you need a second board to assemble the device.A good, reliable ...
-
Power supply 22V 2,5A Atmega8 Control Board This is control board No. 1, you need a second board to assemble the device.A good, reliable and eas...
-
RTL-SDR resiver Не просто очередная беглая статья о модификации тюнера, а подробный мануал о том, как это делается, ...
-
GSM Control and Alarm Sustem Sim300DZ, Sim900D Устройство управления и контроля на протяжении длительного времени пользуется большой популярностью ...
-
ESR_LCFv3_miron63 Ссылка на форум
-
Soldering station ### DESCRIPTION### TECHNICAL DETAILS / COMPONENTS### LEARN / TOPIC / BUILD INSTRUCTIONS
-
PROEKT ### DESCRIPTION### TECHNICAL DETAILS / COMPONENTS### LEARN / TOPIC / BUILD INSTRUCTIONS
-
Solderind station ### DESCRIPTION### TECHNICAL DETAILS / COMPONENTS### LEARN / TOPIC / BUILD INSTRUCTIONS
-
USB Осциллограф клон instrustar isds205A плата от ZuuM, Clon 205 oscill https://youЧастота сигнала 12мГцДва каналаСуть такова, я уже писал о выборе цифрового осциллографа т...
-
CW KEYER ps/2 attiny2313, Christmas2019 Для многих радиолюбителей стало привычным делом, работая телеграфом, использовать для генерации кода...
-
CW Coder Ps/2 ### DESCRIPTION### TECHNICAL DETAILS / COMPONENTS### LEARN / TOPIC / BUILD INSTRUCTIONS
-
Power supply 22V 2,5A Main Board This is the control board number 2, you need a second board to assemble the device.A good, reliable ...
-
Power supply 22V 2,5A Atmega8 Control Board This is control board No. 1, you need a second board to assemble the device.A good, reliable and eas...
-
RTL-SDR resiver Не просто очередная беглая статья о модификации тюнера, а подробный мануал о том, как это делается, ...
-
-
-
Modifying a Hotplate to a Reflow Solder Station
687 1 5 -
MPL3115A2 Barometric Pressure, Altitude, and Temperature Sensor
370 0 1 -
-
Nintendo 64DD Replacement Shell
332 0 2 -
V2 Commodore AMIGA USB-C Power Sink Delivery High Efficiency Supply Triple Output 5V ±12V OLED display ATARI compatible shark 100W
901 4 2 -
How to measure weight with Load Cell and HX711
607 0 3