![]() |
106CKR063MIllinois Capacitor
|
x 1 | |
![]() |
106CKR063MCDE / Illinois Capacitor
|
x 1 | |
![]() |
600L5R6AT200TAmerican Technical Ceramics
|
x 1 | |
![]() |
3-641213-3TE Connectivity AMP Connectors
|
x 1 |
Diy Powersuply For Arduino & Related Projects
When talking about power, the priority is usually to get more of it. As teenagers, we wanted the most powerful cars, cities always need more electrical power for their populations, armies need more military power, and the space race pushed the limits on building more powerful rockets. Printed circuit boards also need more power, but their priorities are a little different. The goal of a successful PCB design is to provide it with clean power.
The power supply you create on your PCB design needs to provide the rest of the circuitry with clean, uninterrupted power. You need to design the power supply so that it creates as little noise as possible, and the noise that it does create will be isolated from the rest of the design. You also must consider how the heat that the power supply will create will affect the circuit board, and design for it accordingly. Lastly, you also need to understand how your design will affect the manufacturing process of the board. Here are some power supply PCB design guidelines that can help.
PCB Design Considerations for Power Supply
Whatever the purpose of your printed circuit board is, it will need power to function. Typically, this is accomplished with an onboard power supply. Power supplies are broken up into two main groups according to their operation:
Linear power supplies are fairly simple and low cost to design onto a PCB. They are used in systems where the power requirements are lower.
Switch-mode power supplies (SMPS), on the other hand, are more efficient than linear power supplies, but they are also more complex and their switching noise can create EMI if care isn’t taken in their design.
SMPSs are further divided by type: isolated and non-isolated. Higher-input voltages require the use of transformer isolation. There are many isolated SMPS variations, depending on their function and power rating, including flyback, forward, push-pull, half bridge, and full bridge. Non-isolated SMPSs include the following types:
Buck: This SMPS steps down the voltage while stepping up the current.
Boost: This SMPS steps up the voltage while stepping down the current.
Buck-boost: This SMPS contains elements of both the buck and boost converters, and will either step down or step up the output voltage.
Whichever power supply type and configuration you end up using on your board, it must be designed to deliver clean power with as little noise as possible. To that end, there are some considerations that you should keep in mind when designing the power supply on your PCB:
Current: Your power supply will be dealing with high levels of current, so make sure that you use adequate trace widths and copper weight to handle it.
Noise: You should use the most compact packages possible, the tightest and most optimized component placement, the best grounding strategy, and the shortest routing to reduce the chance of noise creating EMI for the rest of the board.
Heat: A power supply will get hot, so make sure that you design your supply to dissipate heat as much as possible.
There’s a lot to consider there, so let’s look a little closer into how you can do this in the layout.
Power Supply PCB Design Guidelines for Place and Route
Here are some PCB layout guidelines that can help you to design a cleaner power supply:
Layer stackup: In a multi-layer board configuration, you should have a ground or power plane between the outer layer with the power supply components and routing, and the inner layer with sensitive signals. The plane will act as a shield to protect the sensitive signal traces from the noisy power components and routing on the outer layer.
Component placement: Keep the power supply parts close together to minimize their trace lengths and close to devices receiving the load. You also need to place the parts so that the power path is short and direct through them. In a buck converter, you would start with the input capacitor next to the IC that it is connected to on the same layer. The same is true with the inductor—it should also be close to the IC and on the same layer. Then, the output capacitor should be placed immediately after the inductor to minimize its routing. Once these main power components are placed, you can then place the remaining parts of the supply as close as possible.
Trace routing: Some designers will route as they place, while others will route after the placement is complete. Either way, your routing should complement your placement with short direct traces. Ensure you use wide enough traces for the current, and use 45 degree or rounded corners instead of right angles. Avoid using vias for power traces as they add inductance. Since the main power components are all on the same side of the board, this won’t be a problem. Also, avoid routing other signal traces under the power parts.
Grounding: You should create a separate ground for the power components, and a solid ground plane is preferred over routing it with traces. Not only will this provide optimal grounding for the power supply. but it will also isolate the noise of the current return paths on their own plane away from sensitive signal return paths on the common ground plane. Eventually, the two ground planes will be connected at a single point, which is often the ground via in the thermal pad under the power supply IC. This will connect the two planes together, as well as provide a way to dissipate heat from the power supply. In linear power supply designs, you should also create a void in the ground plane under high-gain devices.
Designing PCB Power Supplies for Successful Manufacturing
With these recommendations, you are on your way to designing a successful PCB power supply, but you still need the board to be manufactured. With the tight placement requirements of a power supply layout, you need to work ahead with your PCB contract manufacturer to ensure they can build what you are designing. If not, they should work with you to come up with a design strategy to satisfy both the electrical and manufacturing requirements of the board.
As you can see, choosing the right CM to build your boards is very important. At VSE, we have been working with design engineers for more than 30 years to design and build the best PCB power supply circuits possible. We also have the advantage of being able to help you through any UL or other certification requirements that your designs may need.
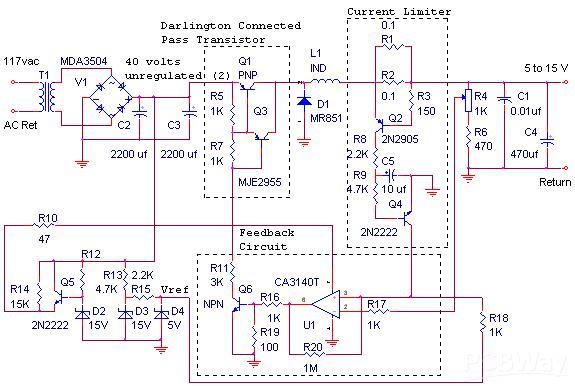
Diy Powersuply For Arduino & Related Projects
*PCBWay community is a sharing platform. We are not responsible for any design issues and parameter issues (board thickness, surface finish, etc.) you choose.
- Comments(0)
- Likes(1)
-
Zhuxuan Ma Apr 05,2022
- 0 USER VOTES
- YOUR VOTE 0.00 0.00
- 1
- 2
- 3
- 4
- 5
- 6
- 7
- 8
- 9
- 10
- 1
- 2
- 3
- 4
- 5
- 6
- 7
- 8
- 9
- 10
- 1
- 2
- 3
- 4
- 5
- 6
- 7
- 8
- 9
- 10
- 1
- 2
- 3
- 4
- 5
- 6
- 7
- 8
- 9
- 10
More by Sreeram.zeno
-
Esp12-F Cluster V1.0 The ESP8266 is a low-cost Wi-Fi microchip, with built-in TCP/IP networking software, and microcontro...
-
TB6612FNG Motor Driver The TB6612FNG Motor Driver can control up to two DC motors at a constant current of 1.2A (3.2A peak)...
-
Sunny Buddy Solar Charger v1.0 This is the Sunny Buddy, a maximum power point tracking (MPPT) solar charger for single-cell LiPo ba...
-
Diy 74HC4051 8 Channel Mux Breakout Pcb The 74HC4051; 74HCT4051 is a single-pole octal-throw analog switch (SP8T) suitable for use in analog...
-
Diy RFM97CW Breakout Pcb IntroductionLoRa? (standing for Long Range) is a LPWAN technology, characterized by a long range ass...
-
ProMicro-RP2040 Pcb The RP2040 is a 32-bit dual ARM Cortex-M0+ microcontroller integrated circuit by Raspberry Pi Founda...
-
Serial Basic CH340G Pcb A USB adapter is a type of protocol converter that is used for converting USB data signals to and fr...
-
Mp3 Shield For Arduino Hardware OverviewThe centerpiece of the MP3 Player Shield is a VS1053B Audio Codec IC. The VS1053B i...
-
MRK CAN Shield Arduino The CAN-BUS Shield provides your Arduino or Redboard with CAN-BUS capabilities and allows you to hac...
-
AVR ISP Programmer AVR is a family of microcontrollers developed since 1996 by Atmel, acquired by Microchip Technology ...
-
Diy Arduino mega Pcb The Arduino Mega 2560 is a microcontroller board based on the ATmega2560. It has 54 digital input/ou...
-
Max3232 Breakout Board MAX3232 IC is extensively used for serial communication in between Microcontroller and a computer fo...
-
Line Follower Pcb The Line Follower Array is a long board consisting of eight IR sensors that have been configured to ...
-
HMC6343 Accelerometer Module The HMC6343 is a solid-state compass module with tilt compensation from Honeywell. The HMC6343 has t...
-
RTK2 GPS Module For Arduino USBThe USB C connector makes it easy to connect the ZED-F9P to u-center for configuration and quick ...
-
Arduino Explora Pcb The Arduino Esplora is a microcontroller board derived from the Arduino Leonardo. The Esplora differ...
-
Diy Stepper Motor Easy Driver A motor controller is a device or group of devices that can coordinate in a predetermined manner the...
-
Diy Arduino Pro Mini The Arduino Pro Mini is a microcontroller board based on the ATmega168 . It has 14 digital input/out...
-
TEKTRONIX THS710,THS720,THS730 External Battery Charger with 3D Printed Case
28 1 0 -
-
Atomic Force Microscope - electronic part
96 0 0 -