LED COB Controller
LED COB Controller
COB LED lights, or Chip-on-Board LED lights, are a type of LED light that has all of the LED chips mounted on a single substrate. This makes them more efficient than traditional LED lights, which have individual LED chips mounted on a circuit board. COB LED lights also produce a more uniform light output, and they can be used in a wider variety of applications.
Here are some of the benefits of using LED COB lights:
are very efficient, and they can produce up to 100 lumens per watt. This means that they use less energy than traditional light bulbs, and they can save you money on your energy bills.
produce a more uniform light output than traditional LED lights. This means that they do not create hot spots or shadows, and they provide a more comfortable light to work under.
are very durable, and they can last for many years. They are not as susceptible to damage from heat or vibration as traditional light bulbs, and they can withstand harsh conditions.
can be used in a wide variety of applications, including indoor and outdoor lighting, commercial and residential lighting, and automotive lighting.
They can however be quite a pain to power in a traditional 110v/220v AC wired house or workshop, as some of them actually required DC current to work.
I have decided to use a pair of them to provide additional, dimmable light at my electronics workbench, a place where extra light is sometimes a very necessary commodity. The ability to dim the lights will definitely aid in many scenarios as well.
The Variable voltage Power module was designed specifically for this project
The project consists of two main parts, the first being the Variable Voltage Power Module, which I published a few days ago. The particular COB lights that I will be using, were scavenged from a battery-operated emergency light panel, which had some problems which were not economical to repair. The light modules themselves, however, looked good and were perfectly working as well.
The only issue was that they were 6v DC. So using straight 12v there was out of the question. 6V being an odd voltage in my lab, I designed the module above specifically to provide that.
LED COB Controller stacked on top of Variable Voltage Poser Module
The second part of the project consists of a simple Custom ESP-12E PCB. Why ESP12-E? Well, I have a lot of them lying in stock, and since I won’t need any advanced features, commonly found on the bigger ESP32s, I decided to design around something that I have in stock, rather than overcomplicate the design with a bigger more advanced chip. The project features a rotary encoder, to adjust light intensity, as well as push buttons to toggle the lights on or off…
All of this is of course controlled with ESPHome. This choice gives me the option of manual or fully automatic control from HomeAssistant. It also saves me a lot of coding, as everything usually just works.
What is on the PCB?
We shall focus mainly on LED COB Controller PCB.
In order to understand everything, please refer to the picture below:
LED COB controller without Power Module
The board consists of a few sections, which can be divided as follows:
ESP-12E (8266) supporting circuitry
The top area is mainly the supporting circuitry for the ESP-12E, which includes a 6-pin header to flash firmware, the classic ESP32/8266 Auto Flash/Reset circuit, and manual Flash and Reset switches. Note that the board DOES NOT contain any USB-to-Serial circuitry. I usually use those only once or twice, and update firmware OTA after that. Using an external USB-to-Serial adapter is thus sufficient for my purposes.
Power and LED Control circuitry
Power enters the board in the center, using header pins mounted on the bottom of the PCB. From left to right, these are 3.3v and then two variable voltage inputs. These all originate from the Variable voltage Power Module, mounted below the main PCB. The LED Control circuitry consists of two P-Channel Mosfets, the configuration of which was previously tested in another project, the “P-MOS MOSFET Driver Board“, also published a few weeks ago. The SI2301 P-Channel Logic Level MOSFET, used here is capable of switching up to 2.3A at 20v, and thus more than capable of handling the 300mA that the LED COB modules require.
Four cutouts are provided to access test points on the power module below, as well as the potentiometers used to set the voltage that will ultimately be sent to the LED COB Modules.
Wide copper traces connect the Mosfet’s to Screw Terminals for the LED Modules.
The Final part of the PCB is dedicated to control interfaces. A single 6-way screw terminal is provided at the bottom left corner, this is used to connect a rotary encoder, or give direct access to additional GPIO pins. On the Right hand side of the PCB, a series of header pins give access to additional 3.3v and ground connections, in addition to GPIO 4 and 5, which is usually used for I2C…
LED COB Controller stacked on top of Variable Voltage Poser Module
The Schematic
Configuration and Software
As mentioned above, this device was designed to be used with ESPHome. The configuration is thus a single YAML file and can be greatly customised to suit your exact needs…
With that in mind, I present here a VERY basic YAML file, that will toggle the LED lights on or off on pressing the encoder switch, as well as adjust the brightness by turning the encoder.
esphome:
name: led-cob-controller
friendly_name: LED_COB-Controller
esp8266:
board: nodemcuv2
restore_from_flash: True
# Enable logging
logger:
# Enable Home Assistant API
api:
encryption:
key: "<esphome generated>"
ota:
password: "<esphome generated>"
wifi:
ssid: !secret wifi_ssid
password: !secret wifi_password
# Enable fallback hotspot (captive portal) in case wifi connection fails
ap:
ssid: "Led-Cob-Controller"
password: "<your recovery password here>"
captive_portal:
# I suggest you only copy paste from here on downwards.
# Setup the default device in ESPHome, and when it is available,
# come back and add the commands below here
text_sensor:
- platform: wifi_info
ip_address:
name: IP Address
ssid:
name: SSID
bssid:
name: BSSID
mac_address:
name: Wifi MAC
scan_results:
name: WiFi Scan Results
sensor:
- platform: adc
pin: VCC
name: "ESP8266 Chip Voltage"
id: mcu_voltage
unit_of_measurement: "V"
device_class: "voltage"
accuracy_decimals: 2
update_interval: 60s
entity_category: "diagnostic"
- platform: wifi_signal
name: "WiFi Signal Sensor"
id: wifi_strength
device_class: "signal_strength"
unit_of_measurement: "dBm"
update_interval: 240s
entity_category: "diagnostic"
- platform: copy # Reports the WiFi signal strength in %
source_id: wifi_strength
name: "WiFi Signal Strength"
filters:
- lambda: return min(max(2 * (x + 100.0), 0.0), 100.0);
unit_of_measurement: "%"
entity_category: "diagnostic"
- platform: copy
source_id: rcbright
name: "LED Light Brightness"
unit_of_measurement: "%"
filters:
- lambda: return (x * 100);
- platform: rotary_encoder
name: "Brightness Control"
id: rcbright
min_value: 0.00
max_value: 100.00
publish_initial_value: True
restore_mode: RESTORE_DEFAULT_ZERO
pin_a:
number: GPIO13
inverted: True
mode:
input: True
pullup: True
pin_b:
number: GPIO2
inverted: True
mode:
input: True
pullup: True
resolution: 1
accuracy_decimals: 2
filters:
- lambda: return x / 100 ;
on_clockwise:
- light.control:
id: led_light1
brightness: !lambda |-
// output value must be in range 0 - 1.0
return id(rcbright).state ; // /100.0;
- light.control:
id: led_light2
brightness: !lambda |-
// output value must be in range 0 - 1.0
return id(rcbright).state ; // /100.0;
on_anticlockwise:
- light.control:
id: led_light1
brightness: !lambda |-
return id(rcbright).state ;
- light.control:
id: led_light2
brightness: !lambda |-
// output value must be in range 0 - 1.0
return id(rcbright).state ; // /100.0;
binary_sensor:
- platform: gpio
pin: GPIO14
id: light_switch
name: "Light Switch"
device_class: light
on_click:
then:
- light.toggle: led_light1
- light.toggle: led_light2
light:
- platform: monochromatic
name: "LED1_LIGHT_TEST"
id: led_light1
output: output_component1
- platform: monochromatic
name: "LED2_LIGHT_TEST"
id: led_light2
output: output_component2
# Example output entry
output:
- platform: esp8266_pwm
id: output_component1
pin: GPIO12
- platform: esp8266_pwm
id: output_component2
pin: GPIO16
Assembly and Testing
This device does not need a stencil for assembly, but using one will definitely speed up things. I chose to do this build all by hand, from applying solder-paste, up to placing components.
Soldering was done on a hotplate, as usual, to reflow everything at the same time. TH components were then placed and hand-soldered.
Uploading the initial firmware, after adding the device to ESPHome was done with an external USB-to-UART converter. All further firmware changes were made via OTA.
The board performs well, with only slight heating of the LM317G variable voltage regulators on the power module when both LED COB modules are at 100% brightness. The current draw is within limits and seems to peak at about 600mA per COB…
Conclusion
This project took quite a while to move from idea to practical reality, mainly due to being busy with other more important stuff. In the end, I am happy that I sat down and did it, because it definitely will become a valuable tool in my work area.
esphome:
name: led-cob-controller
friendly_name: LED_COB-Controller
esp8266:
board: nodemcuv2
restore_from_flash: True
# Enable logging
logger:
# Enable Home Assistant API
api:
encryption:
key: "<esphome generated>"
ota:
password: "<esphome generated>"
wifi:
ssid: !secret wifi_ssid
password: !secret wifi_password
# Enable fallback hotspot (captive portal) in case wifi connection fails
ap:
ssid: "Led-Cob-Controller"
password: "<your recovery password here>"
captive_portal:
# I suggest you only copy paste from here on downwards.
# Setup the default device in ESPHome, and when it is available,
# come back and add the commands below here
text_sensor:
- platform: wifi_info
ip_address:
name: IP Address
ssid:
name: SSID
bssid:
name: BSSID
mac_address:
name: Wifi MAC
scan_results:
name: WiFi Scan Results
sensor:
- platform: adc
pin: VCC
name: "ESP8266 Chip Voltage"
id: mcu_voltage
unit_of_measurement: "V"
device_class: "voltage"
accuracy_decimals: 2
update_interval: 60s
entity_category: "diagnostic"
- platform: wifi_signal
name: "WiFi Signal Sensor"
id: wifi_strength
device_class: "signal_strength"
unit_of_measurement: "dBm"
update_interval: 240s
entity_category: "diagnostic"
- platform: copy # Reports the WiFi signal strength in %
source_id: wifi_strength
name: "WiFi Signal Strength"
filters:
- lambda: return min(max(2 * (x + 100.0), 0.0), 100.0);
unit_of_measurement: "%"
entity_category: "diagnostic"
- platform: copy
source_id: rcbright
name: "LED Light Brightness"
unit_of_measurement: "%"
filters:
- lambda: return (x * 100);
- platform: rotary_encoder
name: "Brightness Control"
id: rcbright
min_value: 0.00
max_value: 100.00
publish_initial_value: True
restore_mode: RESTORE_DEFAULT_ZERO
pin_a:
number: GPIO13
inverted: True
mode:
input: True
pullup: True
pin_b:
number: GPIO2
inverted: True
mode:
input: True
pullup: True
resolution: 1
accuracy_decimals: 2
filters:
- lambda: return x / 100 ;
on_clockwise:
- light.control:
id: led_light1
brightness: !lambda |-
// output value must be in range 0 - 1.0
return id(rcbright).state ; // /100.0;
- light.control:
id: led_light2
brightness: !lambda |-
// output value must be in range 0 - 1.0
return id(rcbright).state ; // /100.0;
on_anticlockwise:
- light.control:
id: led_light1
brightness: !lambda |-
return id(rcbright).state ;
- light.control:
id: led_light2
brightness: !lambda |-
// output value must be in range 0 - 1.0
return id(rcbright).state ; // /100.0;
binary_sensor:
- platform: gpio
pin: GPIO14
id: light_switch
name: "Light Switch"
device_class: light
on_click:
then:
- light.toggle: led_light1
- light.toggle: led_light2
light:
- platform: monochromatic
name: "LED1_LIGHT_TEST"
id: led_light1
output: output_component1
- platform: monochromatic
name: "LED2_LIGHT_TEST"
id: led_light2
output: output_component2
# Example output entry
output:
- platform: esp8266_pwm
id: output_component1
pin: GPIO12
- platform: esp8266_pwm
id: output_component2
pin: GPIO16
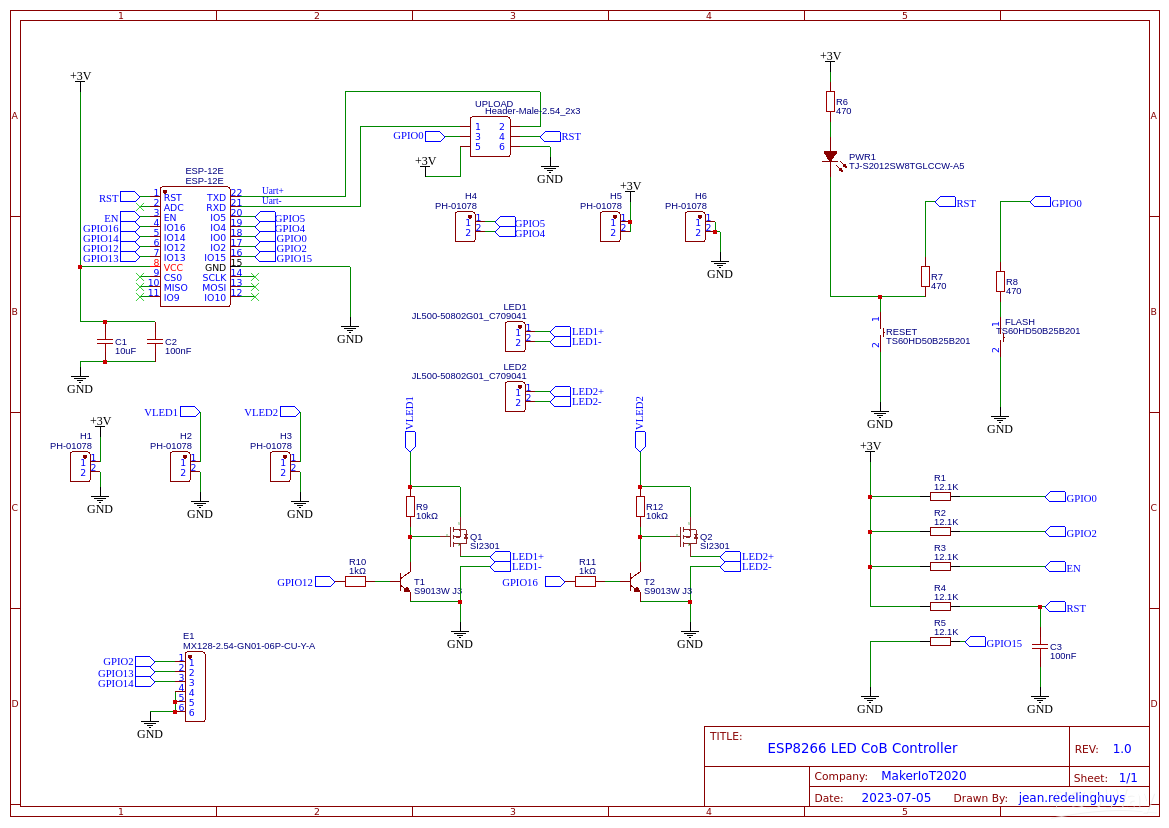
LED COB Controller
*PCBWay community is a sharing platform. We are not responsible for any design issues and parameter issues (board thickness, surface finish, etc.) you choose.
- Comments(0)
- Likes(1)
-
Engineer Oct 15,2023
- 0 USER VOTES
- YOUR VOTE 0.00 0.00
- 1
- 2
- 3
- 4
- 5
- 6
- 7
- 8
- 9
- 10
- 1
- 2
- 3
- 4
- 5
- 6
- 7
- 8
- 9
- 10
- 1
- 2
- 3
- 4
- 5
- 6
- 7
- 8
- 9
- 10
- 1
- 2
- 3
- 4
- 5
- 6
- 7
- 8
- 9
- 10
More by Jean Redelinghuys MakerIoT2020
-
PCB_MCP23008_2023-10-08 MCP23008 BreakoutI designed this breakout to assist me during prototyping my next version of the “RP...
-
PCB_XiaoRP2040-Mouse-REV2 Xiao RP2040 Joystick Mouse – revision 2.00Revision 1.0 of the ProjectOver the last few months, I hav...
-
Multi Purpose IO Card Multi-Purpose IO CardWhen we are working on a prototype, we always need access to pushbuttons, encod...
-
Variable Voltage Power Module Variable Voltage Power ModulePowering electronics projects are always challenging. This Variable vol...
-
I2C Matrix Keypad An I2C Matrix KeypadThe completed I2C Matrix KeypadIn a previous post this month I introduced my 4×4...
-
ESP32-S Development Board, in "Arduino Uno" form factor UPDATE 24/06/2023:This board now has a Hardware Revision 2.0 available. It is the same board but wit...
-
W307186ASC94_Gerber_PCB_USB-Ports USB Power Supply ModuleUSB Ports are quite handy to power all our day-to-day electronic devices, but...
-
Atmega 328P based PWM controller Card ATMega 328P Based PWM controller CardAs part of my recent ESP-12E I2C Base Board project, I designed...
-
W307186ASC71_Gerber_PCB_ESP-Now Remote Today we will look at the remote control unit for the Robotic Toy Car – Part 6.The project is close ...
-
W307186ASV69_Gerber_PCB_Robot-Car-MCU-Board Prototype In our last project, we started working on repurposing an old toy car. In this part, Robot Toy Car –...
-
W307186ASV62_Gerber_PCB_DUAL-H-Bridge by makeriot2020 on May 27, 2022Many of us have old toys laying around the house, they belong to ou...
-
CAN-BUS Breakout Breadboard Compatible CAN-BUS Breakout ModuleWhat is this:Some of us have already used the commonly ...
-
RA-02 Breakout with Level converters Breadboard and beginner-friendly RA-02 Breakout ModuleMost Makers and electronics enthusiasts may al...
-
ATMEGA328P Module with integrated LoRa and CAN Bus ATMEGA328P Module with integrated LoRa and CAN-BUSINTRODUCTIONIn my quest to perfect my LoRa telemet...
-
Sx127x-Ra-02-Test-Module with ATMEGA328P-AU SX127x LoRa/FSK/OOK Prototype Radio BoardI recently had a requirement to do some automation/telemetr...
-
USB-ASP Programmer ATMEGA8 Build your own USB-ASP Programmer CloneBymakeriot2020 FEB 21, 2022 Arduino, ASP programmerUsing mor...
-
ATTiny1616-LIGHT-Controller-with-CAN_B_PCB_ATTiny1616-LIGHT-Controller-with-C_2024-09-11 Assembly of the ATTiny1616 Can bus controller PCBThe Assembly of the ATTiny1616 Can Bus Controller P...
-
ATTiny1616QFN-CAN-Remote-Neopixel-Ligh_PCB_ATTiny1616QFN-CAN-Remote-Neopixel-2024-09-11_2024-09-11 NeoPixel CAN-Bus Module with local controlAs part of my current project to add NeoPixels to the cabi...
-
-
-
kmMiniSchield MIDI I/O - IN/OUT/THROUGH MIDI extension for kmMidiMini
121 0 0 -
DIY Laser Power Meter with Arduino
172 0 2 -
-
-
Box & Bolt, 3D Printed Cardboard Crafting Tools
162 0 2 -