Diy Usb Powersupply
Universal Serial Bus (USB) is an industry standard that establishes specifications for cables, connectors and protocols for connection, communication and power supply (interfacing) between computers, peripherals and other computers.
A broad variety of USB hardware exists, including 14 different connector types, of which USB-C is the most recent.
First released in 1996, the USB standards are maintained by the USB Implementers Forum (USB-IF). The four generations of USB are: USB 1.x, USB 2.0, USB 3.x, and USB4
USB was designed to standardize the connection of peripherals to personal computers, both to communicate with and to supply electric power. It has largely replaced interfaces such as serial ports and parallel ports, and has become commonplace on a wide range of devices. Examples of peripherals that are connected via USB include computer keyboards and mice, video cameras, printers, portable media players, mobile (portable) digital telephones, disk drives, and network adapters.
USB connectors have been increasingly replacing other types as charging cables of portable devices.
Objectives
The Universal Serial Bus was developed to simplify and improve the interface between personal computers and peripheral devices, such as cell phones, computer accessories, and monitors, when compared with previously existing standard or ad hoc proprietary interfaces.
From the computer user's perspective, the USB interface improves ease of use in several ways:
The USB interface is self-configuring, eliminating the need for the user to adjust the device's settings for speed or data format, or configure interrupts, input/output addresses, or direct memory access channels.
USB connectors are standardized at the host, so any peripheral can use most available receptacles.
USB takes full advantage of the additional processing power that can be economically put into peripheral devices so that they can manage themselves. As such, USB devices often do not have user-adjustable interface settings.
The USB interface is hot-swappable (devices can be exchanged without rebooting the host computer).
Small devices can be powered directly from the USB interface, eliminating the need for additional power supply cables.
Because use of the USB logo is only permitted after compliance testing, the user can have confidence that a USB device will work as expected without extensive interaction with settings and configuration.
The USB interface defines protocols for recovery from common errors, improving reliability over previous interfaces.
Installing a device that relies on the USB standard requires minimal operator action. When a user plugs a device into a port on a running computer, it either entirely automatically configures using existing device drivers, or the system prompts the user to locate a driver, which it then installs and configures automatically.
The USB standard also provides multiple benefits for hardware manufacturers and software developers, specifically in the relative ease of implementation:
The USB standard eliminates the requirement to develop proprietary interfaces to new peripherals.
The wide range of transfer speeds available from a USB interface suits devices ranging from keyboards and mice up to streaming video interfaces.
A USB interface can be designed to provide the best available latency for time-critical functions or can be set up to do background transfers of bulk data with little impact on system resources.
The USB interface is generalized with no signal lines dedicated to only one function of one device.
Limitations
As with all standards, USB possesses multiple limitations to its design:
USB cables are limited in length, as the standard was intended for peripherals on the same table-top, not between rooms or buildings. However, a USB port can be connected to a gateway that accesses distant devices.
USB data transfer rates are slower than those of other interconnects such as 100 Gigabit Ethernet.
USB has a strict tree network topology and master/slave protocol for addressing peripheral devices; those devices cannot interact with one another except via the host, and two hosts cannot communicate over their USB ports directly. Some extension to this limitation is possible through USB On-The-Go in, Dual-Role-Devices and protocol bridge.
A host cannot broadcast signals to all peripherals at once—each must be addressed individually.
While converters exist between certain legacy interfaces and USB, they may not provide a full implementation of the legacy hardware. For example, a USB-to-parallel-port converter may work well with a printer, but not with a scanner that requires bidirectional use of the data pins.
For a product developer, using USB requires the implementation of a complex protocol and implies an "intelligent" controller in the peripheral device. Developers of USB devices intended for public sale generally must obtain a USB ID, which requires that they pay a fee to the USB Implementers Forum (USB-IF). Developers of products that use the USB specification must sign an agreement with the USB-IF. Use of the USB logos on the product requires annual fees and membership in the organization.
USB 1.x
Released in January 1996, USB 1.0 specified signaling rates of 1.5 Mbit/s (Low Bandwidth or Low Speed) and 12 Mbit/s (Full Speed).[15] It did not allow for extension cables or pass-through monitors, due to timing and power limitations. Few USB devices made it to the market until USB 1.1 was released in August 1998. USB 1.1 was the earliest revision that was widely adopted and led to what Microsoft designated the "Legacy-free PC".
Neither USB 1.0 nor 1.1 specified a design for any connector smaller than the standard type A or type B. Though many designs for a miniaturised type B connector appeared on many peripherals, conformity to the USB 1.x standard was hampered by treating peripherals that had miniature connectors as though they had a tethered connection (that is: no plug or receptacle at the peripheral end). There was no known miniature type A connector until USB 2.0 (revision 1.01) introduced one.
USB 2.0
The Hi-Speed USB logo
A USB 2.0 PCI expansion card
USB 2.0 was released in April 2000, adding a higher maximum signaling rate of 480 Mbit/s (maximum theoretical data throughput 53 MByte/s[19]) named High Speed or High Bandwidth, in addition to the USB 1.x Full Speed signaling rate of 12 Mbit/s (maximum theoretical data throughput 1.2 MByte/s[20]).
Modifications to the USB specification have been made via engineering change notices (ECNs). The most important of these ECNs are included into the USB 2.0 specification package available from USB.org:[21]
Mini-A and Mini-B Connector
Micro-USB Cables and Connectors Specification 1.01
InterChip USB Supplement
On-The-Go Supplement 1.3 USB On-The-Go makes it possible for two USB devices to communicate with each other without requiring a separate USB host
Battery Charging Specification 1.1 Added support for dedicated chargers, host chargers behaviour for devices with dead batteries
Battery Charging Specification 1.2:[22] with increased current of 1.5 A on charging ports for unconfigured devices, allowing High Speed communication while having a current up to 1.5 A
Link Power Management Addendum ECN, which adds a sleep power state
USB 2.0 VBUS Max Limit, increased the maximum allowable V_BUS voltage from 5.25V to 5.50V to align with the USB Type-C Spec, which was released simultaneously.
USB 3.x
Main article: USB 3.0
The SuperSpeed USB logo
The USB 3.0 specification was released on 12 November 2008, with its management transferring from USB 3.0 Promoter Group to the USB Implementers Forum (USB-IF), and announced on 17 November 2008 at the SuperSpeed USB Developers Conference.[23]
USB 3.0 adds a SuperSpeed transfer mode, with associated backward compatible plugs, receptacles, and cables. SuperSpeed plugs and receptacles are identified with a distinct logo and blue inserts in standard format receptacles.
The SuperSpeed bus provides for a transfer mode at a nominal rate of 5.0 Gbit/s, in addition to the three existing transfer modes. Its efficiency is dependent on a number of factors including physical symbol encoding and link level overhead. At a 5 Gbit/s signaling rate with 8b/10b encoding, each byte needs 10 bits to transmit, so the raw throughput is 500 MB/s. When flow control, packet framing and protocol overhead are considered, it is realistic for 400 MB/s (3.2 Gbit/s) or more to transmit to an application.[24]:?4–19? Communication is full-duplex in SuperSpeed transfer mode; earlier modes are half-duplex, arbitrated by the host.[25]
Low-power and high-power devices remain operational with this standard, but devices using SuperSpeed can take advantage of increased available current of between 150 mA and 900 mA, respectively.[24]:?9–9?
USB-A 3.1 Gen 1 (formerly known as USB 3.0; later renamed USB 3.2 Gen 1x1) ports
USB 3.1, released in July 2013 has two variants. The first one preserves USB 3.0's SuperSpeed transfer mode and is labeled USB 3.1 Gen 1, and the second version introduces a new SuperSpeed+ transfer mode under the label of USB 3.1 Gen 2. SuperSpeed+ doubles the maximum data signaling rate to 10 Gbit/s, while reducing line encoding overhead to just 3% by changing the encoding scheme to 128b/132b.
USB 3.2, released in September 2017,[29] preserves existing USB 3.1 SuperSpeed and SuperSpeed+ data modes but introduces two new SuperSpeed+ transfer modes over the USB-C connector with data rates of 10 and 20 Gbit/s (1.25 and 2.5 GB/s). The increase in bandwidth is a result of multi-lane operation over existing wires that were intended for flip-flop capabilities of the USB-C connector.[30]
USB 3.0 also introduced the UASP protocol, which provides generally faster transfer speeds than the BOT (Bulk-Only-Transfer) protocol.
Naming scheme
Starting with the USB 3.2 standard, USB-IF introduced a new naming scheme.[31] To help companies with branding of the different transfer modes, USB-IF recommended branding the 5, 10, and 20 Gbit/s transfer modes as SuperSpeed USB 5Gbps, SuperSpeed USB 10Gbps, and SuperSpeed USB 20Gbps, respectively.
USB4
Main article: USB4
The certified USB4 40Gbps logo
The USB4 specification was released on 29 August 2019 by the USB Implementers Forum.
USB4 is based on the Thunderbolt 3 protocol.[34] It supports 40 Gbit/s throughput, is compatible with Thunderbolt 3, and backward compatible with USB 3.2 and USB 2.0.[35][36] The architecture defines a method to share a single high-speed link with multiple end device types dynamically that best serves the transfer of data by type and application.
The USB4 specification states that the following technologies shall be supported by USB4
Large sporadic transfers using all remaining available bandwidth, but with no guarantees on bandwidth or latency (e.g., file transfers)
When a host starts a data transfer, it sends a TOKEN packet containing an endpoint specified with a tuple of (device_address,
endpoint_number).
If the transfer is from the host to the endpoint, the host sends an OUT packet (a specialization of a TOKEN packet) with the desired device address and endpoint number. If the data transfer is from the device to the host, the host sends an IN packet instead. If the destination endpoint is a uni-directional endpoint whose manufacturer's designated direction does not match the TOKEN packet (e.g. the manufacturer's designated direction is IN while the TOKEN packet is an OUT packet), the TOKEN packet is ignored. Otherwise, it is accepted and the data transaction can start. A bi-directional endpoint, on the other hand, accepts both IN and OUT packets.
Two USB 3.0 Standard-A receptacles (left) and two USB 2.0 Standard-A receptacles (right) on a computer's front panel
Endpoints are grouped into interfaces and each interface is associated with a single device function. An exception to this is endpoint zero, which is used for device configuration and is not associated with any interface. A single device function composed of independently controlled interfaces is called a composite device. A composite device only has a single device address because the host only assigns a device address to a function.
When a USB device is first connected to a USB host, the USB device enumeration process is started. The enumeration starts by sending a reset signal to the USB device. The data rate of the USB device is determined during the reset signaling. After reset, the USB device's information is read by the host and the device is assigned a unique 7-bit address. If the device is supported by the host, the device drivers needed for communicating with the device are loaded and the device is set to a configured state. If the USB host is restarted, the enumeration process is repeated for all connected devices.
The host controller directs traffic flow to devices, so no USB device can transfer any data on the bus without an explicit request from the host controller. In USB 2.0, the host controller polls the bus for traffic, usually in a round-robin fashion. The throughput of each USB port is determined by the slower speed of either the USB port or the USB device connected to the port.
High-speed USB 2.0 hubs contain devices called transaction translators that convert between high-speed USB 2.0 buses and full and low speed buses. There may be one translator per hub or per port.
Because there are two separate controllers in each USB 3.0 host, USB 3.0 devices transmit and receive at USB 3.0 data rates regardless of USB 2.0 or earlier devices connected to that host. Operating data rates for earlier devices are set in the legacy manner.
usb power supply
A power supply is an electrical device that supplies electric power to an electrical load. The main purpose of a power supply is to convert electric current from a source to the correct voltage, current, and frequency to power the load. As a result, power supplies are sometimes referred to as electric power converters. Some power supplies are separate standalone pieces of equipment, while others are built into the load appliances that they power. Examples of the latter include power supplies found in desktop computers and consumer electronics devices. Other functions that power supplies may perform include limiting the current drawn by the load to safe levels, shutting off the current in the event of an electrical fault, power conditioning to prevent electronic noise or voltage surges on the input from reaching the load, power-factor correction, and storing energy so it can continue to power the load in the event of a temporary interruption in the source power (uninterruptible power supply).
All power supplies have a power input connection, which receives energy in the form of electric current from a source, and one or more power output or rail connections that deliver current to the load. The source power may come from the electric power grid, such as an electrical outlet, energy storage devices such as batteries or fuel cells, generators or alternators, solar power converters, or another power supply. The input and output are usually hardwired circuit connections, though some power supplies employ wireless energy transfer to power their loads without wired connections. Some power supplies have other types of inputs and outputs as well, for functions such as external monitoring and control.
A rackmount, adjustable regulated DC power supply
Functional
Power supplies are categorized in various ways, including by functional features. For example, a regulated power supply is one that maintains constant output voltage or current despite variations in load current or input voltage. Conversely, the output of an unregulated power supply can change significantly when its input voltage or load current changes. Adjustable power supplies allow the output voltage or current to be programmed by mechanical controls (e.g., knobs on the power supply front panel), or by means of a control input, or both. An adjustable regulated power supply is one that is both adjustable and regulated. An isolated power supply has a power output that is electrically independent of its power input; this is in contrast to other power supplies that share a common connection between power input and output.
Packaging
Electronic bench power supply unit with "banana connector" output
Power supplies are packaged in different ways and classified accordingly. A bench power supply is a stand-alone desktop unit used in applications such as circuit test and development. Open frame power supplies have only a partial mechanical enclosure, sometimes consisting of only a mounting base; these are typically built into machinery or other equipment. Rack mount power supplies are designed to be secured into standard electronic equipment racks. An integrated power supply is one that shares a common printed circuit board with its load. An external power supply, AC adapter or power brick, is a power supply located in the load's AC power cord that plugs into a wall outlet; a wall wart is an external supply integrated with the outlet plug itself. These are popular in consumer electronics because of their safety; the hazardous 120 or 240 volt main current is transformed down to a safer voltage before it enters the appliance body.
Power conversion method
Power supplies can be broadly divided into linear and switching types. Linear power converters process the input power directly, with all active power conversion components operating in their linear operating regions. In switching power converters, the input power is converted to AC or to DC pulses before processing, by components that operate predominantly in non-linear modes (e.g., transistors that spend most of their time in cutoff or saturation). Power is "lost" (converted to heat) when components operate in their linear regions and, consequently, switching converters are usually more efficient than linear converters because their components spend less time in linear operating regions.
DC power supplies
An AC-to-DC power supply operates on an AC input voltage and generates a DC output voltage. Depending on application requirements the output voltage may contain large or negligible amounts AC frequency components known as ripple voltage, related to AC input voltage frequency and the power supply's operation. A DC power supply operating on DC input voltage is called a DC-to-DC converter. This section focuses mostly on the AC-to-DC variant.
Linear power supply
In a linear power supply the AC input voltage passes through a power transformer and is then rectified and filtered to obtain a DC voltage. The filtering reduces the amplitude of AC mains frequency present in the rectifier output and can be as simple as a single capacitor or more complex such as a pi filter. The electric load's tolerance of ripple dictates the minimum amount of filtering that must be provided by the power supply. In some applications, ripple can be entirely ignored. For example, in some battery charging applications, the power supply consists of just a transformer and a diode, with a simple resistor placed at the power supply output to limit the charging current.
Switched-mode power supply
In a switched-mode power supply (SMPS), the AC mains input is directly rectified and then filtered to obtain a DC voltage. The resulting DC voltage is then switched on and off at a high frequency by electronic switching circuitry, thus producing an AC current that will pass through a high-frequency transformer or inductor. Switching occurs at a very high frequency (typically 10 kHz — 1 MHz), thereby enabling the use of transformers and filter capacitors that are much smaller, lighter, and less expensive than those found in linear power supplies operating at mains frequency. After the inductor or transformer secondary, the high frequency AC is rectified and filtered to produce the DC output voltage. If the SMPS uses an adequately insulated high-frequency transformer, the output will be electrically isolated from the mains; this feature is often essential for safety.
Switched-mode power supplies are usually regulated, and to keep the output voltage constant, the power supply employs a feedback controller that monitors current drawn by the load. The switching duty cycle increases as power output requirements increase.
SMPSs often include safety features such as current limiting or a crowbar circuit to help protect the device and the user from harm.[1] In the event that an abnormal high-current power draw is detected, the switched-mode supply can assume this is a direct short and will shut itself down before damage is done. PC power supplies often provide a power good signal to the motherboard; the absence of this signal prevents operation when abnormal supply voltages are present.
Some SMPSs have an absolute limit on their minimum current output. They are only able to output above a certain power level and cannot function below that point. In a no-load condition the frequency of the power slicing circuit increases to great speed, causing the isolated transformer to act as a Tesla coil, causing damage due to the resulting very high voltage power spikes. Switched-mode supplies with protection circuits may briefly turn on but then shut down when no load has been detected. A very small low-power dummy load such as a ceramic power resistor or 10-watt light bulb can be attached to the supply to allow it to run with no primary load attached.
The switch-mode power supplies used in computers have historically had low power factors and have also been significant sources of line interference (due to induced power line harmonics and transients). In simple switch-mode power supplies, the input stage may distort the line voltage waveform, which can adversely affect other loads (and result in poor power quality for other utility customers), and cause unnecessary heating in wires and distribution equipment. Furthermore, customers incur higher electric bills when operating lower power factor loads. To circumvent these problems, some computer switch-mode power supplies perform power factor correction, and may employ input filters or additional switching stages to reduce line interference.
Capacitive (transformerless) power supply[edit]
A capacitive power supply (transformerless power supply) uses the reactance of a capacitor to reduce the mains voltage to a smaller AC voltage. Typically, the resulting reduced AC voltage is then rectified, filtered and regulated to produce a constant DC output voltage.
The output voltage is not isolated from the mains. Consequently, to avoid exposing people and equipment from hazardous high voltage, anything connected to the power supply must be reliably insulated.
The voltage reduction capacitor must withstand the full mains voltage, and it must also have enough capacitance to support maximum load current at the rated output voltage. Taken together, these constraints limit practical uses of this type of supply to low-power applications.
Linear regulator
The function of a linear voltage regulator is to convert a varying DC voltage to a constant, often specific, lower DC voltage. In addition, they often provide a current limiting function to protect the power supply and load from overcurrent (excessive, potentially destructive current).
A constant output voltage is required in many power supply applications, but the voltage provided by many energy sources will vary with changes in load impedance. Furthermore, when an unregulated DC power supply is the energy source, its output voltage will also vary with changing input voltage. To circumvent this, some power supplies use a linear voltage regulator to maintain the output voltage at a steady value, independent of fluctuations in input voltage and load impedance. Linear regulators can also reduce the magnitude of ripple and noise on the output voltage.
AC power supplies
An AC power supply typically takes the voltage from a wall outlet (mains supply) and uses a transformer to step up or step down the voltage to the desired voltage. Some filtering may take place as well. In some cases, the source voltage is the same as the output voltage; this is called an isolation transformer. Other AC power supply transformers do not provide mains isolation; these are called autotransformers; a variable output autotransformer is known as a variac. Other kinds of AC power supplies are designed to provide a nearly constant current, and output voltage may vary depending on impedance of the load. In cases when the power source is direct current, (like an automobile storage battery), an inverter and step-up transformer may be used to convert it to AC power.
Portable AC power may be provided by an alternator powered by a diesel or gasoline engine (for example, at a construction site, in an automobile or boat, or backup power generation for emergency services) whose current is passed to a regulator circuit to provide a constant voltage at the output. Some kinds of AC power conversion do not use a transformer. If the output voltage and input voltage are the same, and primary purpose of the device is to filter AC power, it may be called a line conditioner. If the device is designed to provide backup power, it may be called an uninterruptable power supply. A circuit may be designed with a voltage multiplier topology to directly step-up AC power; formerly, such an application was a vacuum tube AC/DC receiver.
In modern use, AC power supplies can be divided into single phase and three phase systems. AC power Supplies can also be used to change the frequency as well as the voltage, they are often used by manufacturers to check the suitability of their products for use in other countries. 230 V 50 Hz or 115 60 Hz or even 400 Hz for avionics testing.
Switch-mode mobile phone charger
An AC adapter is a power supply built into an AC mains power plug. AC adapters are also known by various other names such as "plug pack" or "plug-in adapter", or by slang terms such as "wall wart". AC adapters typically have a single AC or DC output that is conveyed over a hardwired cable to a connector, but some adapters have multiple outputs that may be conveyed over one or more cables. "Universal" AC adapters have interchangeable input connectors to accommodate different AC mains voltages.
Adapters with AC outputs may consist only of a passive transformer (plus a few diodes in DC-output adapters), or they may employ switch-mode circuitry. AC adapters consume power (and produce electric and magnetic fields) even when not connected to a load; for this reason they are sometimes known as "electricity vampires", and may be plugged into power strips to allow them to be conveniently turned on and off.
Programmable power supplies
A programmable power supply (PPS) is one that allows remote control of its operation through an analog input or digital interface such as RS232 or GPIB. Controlled properties may include voltage, current, and in the case of AC output power supplies, frequency. They are used in a wide variety of applications, including automated equipment testing, crystal growth monitoring, semiconductor fabrication, and x-ray generators.
Programmable power supplies typically employ an integral microcomputer to control and monitor power supply operation. Power supplies equipped with a computer interface may use proprietary communication protocols or standard protocols and device control languages such as SCPI.
Uninterruptible power supply
An uninterruptible power supply (UPS) takes its power from two or more sources simultaneously. It is usually powered directly from the AC mains, while simultaneously charging a storage battery. Should there be a dropout or failure of the mains, the battery instantly takes over so that the load never experiences an interruption. Instantly here should be defined as the speed of electricity within conductors which is somewhat near the speed of light. That definition is important because transmission of high speed data and communications service must have continuity/NO break of that service. Some manufacturers use a quasi standard of 4 milliseconds. However, with high speed data even 4 ms of time in transitioning from one source to another is not fast enough. The transition must be made in a break before make method. The UPS meeting that requirement is referred to as a True UPS or a Hybrid UPS. How much time the UPS will provide is most often based on batteries and in conjunction with generators. That time can range from a quasi minimum 5 to 15 minutes to hours or even days. In many computer installations, it is only enough time on batteries to give the operators time to shut down the system in an orderly way. Other UPS schemes may use an internal combustion engine or turbine to supply power during a utility power outage and the amount of battery time is then dependent upon how long it takes the generator to be on line and the criticality of the equipment served. Such a scheme is found in hospitals, data centers, call centers, cell sites and telephone central offices.
High-voltage power supply
A 30 kV high-voltage power supply with Federal Standard connector, used in electron microscopes
A high-voltage power supply is one that outputs hundreds or thousands of volts. A special output connector is used that prevents arcing, insulation breakdown and accidental human contact. Federal Standard connectors are typically used for applications above 20 kV, though other types of connectors (e.g., SHV connector) may be used at lower voltages. Some high-voltage power supplies provide an analog input or digital communication interface that can be used to control the output voltage. High-voltage power supplies are commonly used to accelerate and manipulate electron and ion beams in equipment such as x-ray generators, electron microscopes, and focused ion beam columns, and in a variety of other applications, including electrophoresis and electrostatics.
High-voltage power supplies typically apply the bulk of their input energy to a power inverter, which in turn drives a voltage multiplier or a high turns ratio, high-voltage transformer, or both (usually a transformer followed by a multiplier) to produce high voltage. The high voltage is passed out of the power supply through the special connector and is also applied to a voltage divider that converts it to a low-voltage metering signal compatible with low-voltage circuitry. The metering signal is used by a closed-loop controller that regulates the high voltage by controlling inverter input power, and it may also be conveyed out of the power supply to allow external circuitry to monitor the high-voltage output.
Bipolar power supply
A bipolar power supply (Kepco BOP 6-125MG)
A bipolar power supply operates in all four quadrants of the voltage/current Cartesian plane, meaning that it will generate positive and negative voltages and currents as required to maintain regulation.[3] When its output is controlled by a low-level analog signal, it is effectively a low-bandwidth operational amplifier with high output power and seamless zero-crossings. This type of power supply is commonly used to power magnetic devices in scientific applications.[example needed]
Specification[edit]
The suitability of a particular power supply for an application is determined by various attributes of the power supply, which are typically listed in the power supply's specification. Commonly specified attributes for a power supply include:
Input voltage type (AC or DC) and range
Efficiency of power conversion
The amount of voltage and current it can supply to its load
How stable its output voltage or current is under varying line and load conditions
How long it can supply energy without refueling or recharging (applies to power supplies that employ portable energy sources)
Operating and storage temperature ranges
Commonly-used abbreviations used in power supply specifications:
SCP - Short circuit protection
OPP - Overpower (overload) protection
OCP - Overcurrent protection
OTP - Overtemperature protection
OVP - Overvoltage protection
UVP - Undervoltage protection
Thermal management
The power supply of an electrical system tends to generate heat. The higher the efficiency, the more heat is pulled away from the unit. There are many ways to manage the heat of a power supply unit. The types of cooling generally fall into two categories -- convection and conduction. Common convection methods for cooling electronic power supplies include natural air flow, forced air flow, or other liquid flow over the unit. Common conduction cooling methods include heat sinks, cold plates, and thermal compounds.
Overload protection
Power supplies often have protection from short circuit or overload that could damage the supply or cause a fire. Fuses and circuit breakers are two commonly used mechanisms for overload protection.
A fuse contains a short piece of wire which melts if too much current flows. This effectively disconnects the power supply from its load, and the equipment stops working until the problem that caused the overload is identified and the fuse is replaced. Some power supplies use a very thin wire link soldered in place as a fuse. Fuses in power supply units may be replaceable by the end user, but fuses in consumer equipment may require tools to access and change.
A circuit breaker contains an element that heats, bends and triggers a spring which shuts the circuit down. Once the element cools, and the problem is identified the breaker can be reset and the power restored.
Some PSUs use a thermal cutout buried in the transformer rather than a fuse. The advantage is it allows greater current to be drawn for limited time than the unit can supply continuously. Some such cutouts are self resetting, some are single use only.
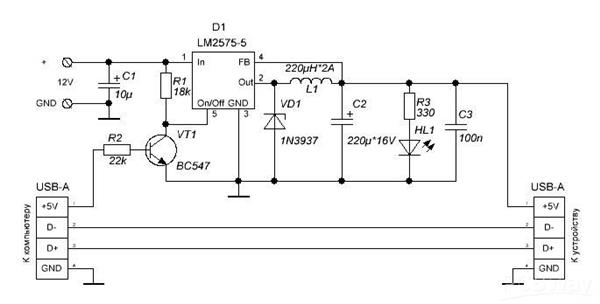
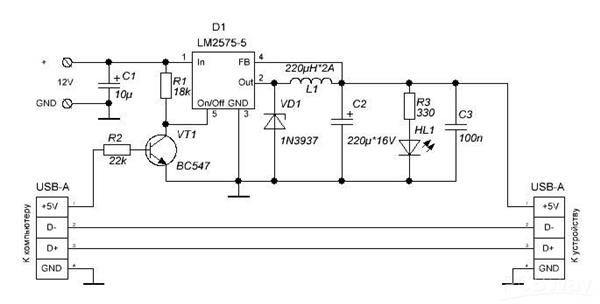
Diy Usb Powersupply
*PCBWay community is a sharing platform. We are not responsible for any design issues and parameter issues (board thickness, surface finish, etc.) you choose.
- Comments(0)
- Likes(0)
- 0 USER VOTES
- YOUR VOTE 0.00 0.00
- 1
- 2
- 3
- 4
- 5
- 6
- 7
- 8
- 9
- 10
- 1
- 2
- 3
- 4
- 5
- 6
- 7
- 8
- 9
- 10
- 1
- 2
- 3
- 4
- 5
- 6
- 7
- 8
- 9
- 10
- 1
- 2
- 3
- 4
- 5
- 6
- 7
- 8
- 9
- 10
More by Sreeram.zeno
-
Esp12-F Cluster V1.0 The ESP8266 is a low-cost Wi-Fi microchip, with built-in TCP/IP networking software, and microcontro...
-
TB6612FNG Motor Driver The TB6612FNG Motor Driver can control up to two DC motors at a constant current of 1.2A (3.2A peak)...
-
Sunny Buddy Solar Charger v1.0 This is the Sunny Buddy, a maximum power point tracking (MPPT) solar charger for single-cell LiPo ba...
-
Diy 74HC4051 8 Channel Mux Breakout Pcb The 74HC4051; 74HCT4051 is a single-pole octal-throw analog switch (SP8T) suitable for use in analog...
-
Diy RFM97CW Breakout Pcb IntroductionLoRa? (standing for Long Range) is a LPWAN technology, characterized by a long range ass...
-
ProMicro-RP2040 Pcb The RP2040 is a 32-bit dual ARM Cortex-M0+ microcontroller integrated circuit by Raspberry Pi Founda...
-
Serial Basic CH340G Pcb A USB adapter is a type of protocol converter that is used for converting USB data signals to and fr...
-
Mp3 Shield For Arduino Hardware OverviewThe centerpiece of the MP3 Player Shield is a VS1053B Audio Codec IC. The VS1053B i...
-
MRK CAN Shield Arduino The CAN-BUS Shield provides your Arduino or Redboard with CAN-BUS capabilities and allows you to hac...
-
AVR ISP Programmer AVR is a family of microcontrollers developed since 1996 by Atmel, acquired by Microchip Technology ...
-
Diy Arduino mega Pcb The Arduino Mega 2560 is a microcontroller board based on the ATmega2560. It has 54 digital input/ou...
-
Max3232 Breakout Board MAX3232 IC is extensively used for serial communication in between Microcontroller and a computer fo...
-
Line Follower Pcb The Line Follower Array is a long board consisting of eight IR sensors that have been configured to ...
-
HMC6343 Accelerometer Module The HMC6343 is a solid-state compass module with tilt compensation from Honeywell. The HMC6343 has t...
-
RTK2 GPS Module For Arduino USBThe USB C connector makes it easy to connect the ZED-F9P to u-center for configuration and quick ...
-
Arduino Explora Pcb The Arduino Esplora is a microcontroller board derived from the Arduino Leonardo. The Esplora differ...
-
Diy Stepper Motor Easy Driver A motor controller is a device or group of devices that can coordinate in a predetermined manner the...
-
Diy Arduino Pro Mini The Arduino Pro Mini is a microcontroller board based on the ATmega168 . It has 14 digital input/out...
-
TEKTRONIX THS710,THS720,THS730 External Battery Charger with 3D Printed Case
46 1 0 -