![]() |
KiCADKicad
|
|
![]() |
PlatformIOPlatformIO Labs
|
|
![]() |
arduino IDEArduino
|
[PROTOTYPE, THIS VERSION HAS PROBLEMS] Robot Control Module BYTE
V1 has been replaced with a new, working design! RCMByte V2
Here is information about how to use these boards
Find documentation for future versions of the boards here: https://github.com/RCMgames/RCM-Hardware-BYTE
Kicad source files for this unfinished prototype: https://github.com/RCMgames/RCM_hardware_documentation_and_user_guide/tree/v1/rcmbytekicad
Update
The boards kind of work! I plan to make some changes for a second version since the current designs can only accept up to 5.5 volts before the 3.3v regulator on the QT Py overheats.
-------------------------------------------------------------------------------
One project that I really enjoyed working on during the COVID-19 pandemic was making small robots that could be controlled over the internet so my friends could drive around my house.
I wanted to figure out a way to build lots of robot designs very quickly and cheaply, so I designed a Robot Control Module (RCM) that combines all the electronics a robot needs except for motors and batteries. Each of the old RCM boards could control up to 4 motors and 5 servos.
My friends and I made many robots using this old RCM design, and had some very fun competitions. The old boards were 5x8cm.
Recently, I started thinking about making a smaller RCM board. I was inspired when a class discussion in a project-based engineering class about building a very small but complicated robot got me thinking about whether I could miniaturize an RCM.
I wanted to find a microcontroller board that includes an esp32 chip instead of using an esp32 chip directly, in order to keep the project simpler and more likely to work – I didn’t want to have to design a circuit with an antenna. And the QT PY is about the same size as most plain esp32 modules are.
I found the Adafruit QT Py esp32 board that’s tiny and still has 13 GPIO pins.
That’s a large decrease from the 20 GPIO pins from the ESP32 boards used in the previous design. I didn’t want to reduce the number of motors and servos that can be connected.
The L293D h-bridge chips in the old design take a lot of pins, if I used a motor driver chip with a serial interface, I could save pins for controlling servos.
After looking at a few options I found the Trinamic TMC7300. https://www.analog.com/en/products/tmc7300.html
Each driver can control 2 motors, and up to 4 drivers can be controlled from just two pins from the QT Py – if I’m reading the datasheet correctly.
This means the new design can control 8 servos and 8 motors.
I got a breakout board for the TMC7300 so I can test software for controlling it, and it seems like a great chip, so far.
I followed the circuit diagram for the breakout board when adding the tmc7300 chip to the circuit diagram of my board.
TMC7300 motor drivers are only available in tiny surface mount QFN packages that I can’t solder by hand. I knew I would need to get a professionally assembled board. By using surface mount components I could shrink my design to a much smaller size than I’ve ever designed for before. Until now I’ve only used hand soldered through hole components.
The new board is almost a quarter the size (by area) compared to the older RCM boards, and yet can control twice the motors and servos. That’s the power of PCB assembly!
This page will be updated when I receive my first prototype batch of boards and can test whether my design works. I will also finish writing software for the boards once I have boards to test. For now, I can not guarantee functionality or promise any support.
Questions or feedback? Post here: https://github.com/orgs/RCMgames/discussions
Happy Roboting!
[PROTOTYPE, THIS VERSION HAS PROBLEMS] Robot Control Module BYTE
*PCBWay community is a sharing platform. We are not responsible for any design issues and parameter issues (board thickness, surface finish, etc.) you choose.
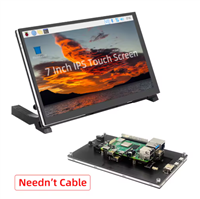
Raspberry Pi 5 7 Inch Touch Screen IPS 1024x600 HD LCD HDMI-compatible Display for RPI 4B 3B+ OPI 5 AIDA64 PC Secondary Screen(Without Speaker)
BUY NOW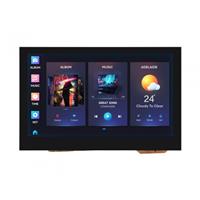
ESP32-S3 4.3inch Capacitive Touch Display Development Board, 800×480, 5-point Touch, 32-bit LX7 Dual-core Processor
BUY NOW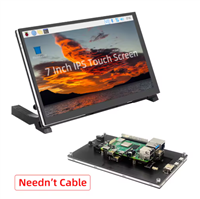
Raspberry Pi 5 7 Inch Touch Screen IPS 1024x600 HD LCD HDMI-compatible Display for RPI 4B 3B+ OPI 5 AIDA64 PC Secondary Screen(Without Speaker)
BUY NOW- Comments(5)
- Likes(0)
- 2 USER VOTES
- YOUR VOTE 0.00 0.00
- 1
- 2
- 3
- 4
- 5
- 6
- 7
- 8
- 9
- 10
- 1
- 2
- 3
- 4
- 5
- 6
- 7
- 8
- 9
- 10
- 1
- 2
- 3
- 4
- 5
- 6
- 7
- 8
- 9
- 10
- 1
- 2
- 3
- 4
- 5
- 6
- 7
- 8
- 9
- 10
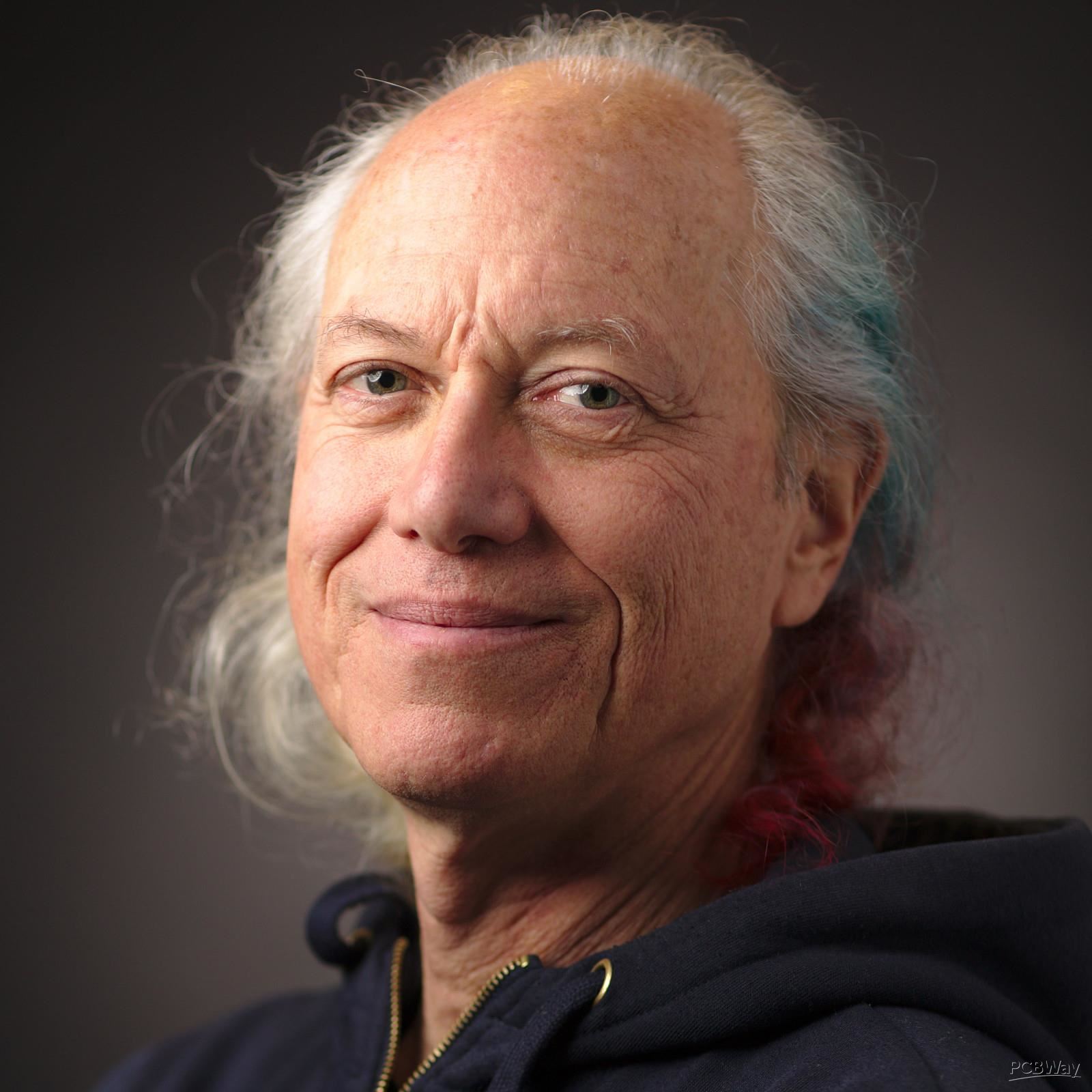
-
9design
-
7usability
-
8creativity
-
5content
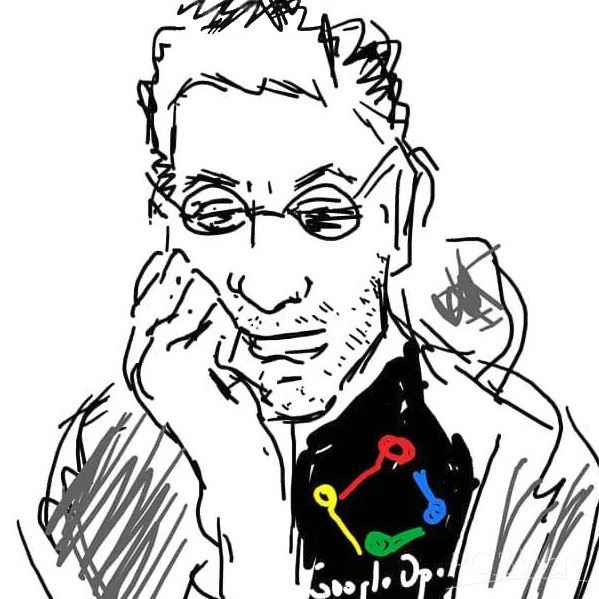
-
7design
-
7usability
-
7creativity
-
6content
More by Robot Control Modules
-
Cheap wifi connected Robot Control Module - RCM D1 v1.0 The goal of this project is to make the cheapest RCM board.* 1.75 by 1.575 inches, 44.45 by 40.0 mil...
-
RCMhardwareNibble-v1.8 https://github.com/RCMgames/RCM-Hardware-Nibble/The RCM Nibble is the smallest board in my series of...
-
I2C 8 channel quadrature encoder reader - ByteSizedEncoderDecoder - v1.1 Reads 8 quadrature encoders1.0x0.85 inches, 25.4x21.59 millimetersI2C (Qwiic Compatible)powered by a...
-
Robot-Control-Module-V4 V1.3 Documentation, KiCAD, Arduino software libraries, and more are all on GitHub: https://github.com/RCM...
-
Byte Sized Encoder Decoder (v1.0) This project has been replaced by a newer version with improved silkscreen and files so PCBWay can d...
-
[PROTOTYPE, THIS VERSION HAS PROBLEMS] Robot Control Module BYTE V1 has been replaced with a new, working design! RCMByte V2Here is information about how to use thes...
-
RCMHardwareByte-v2.3 https://github.com/RCMgames/RCM-Hardware-BYTEThe RCM BYTE is the most powerful board in my series of...
-
Cheap wifi connected Robot Control Module - RCM D1 v1.0 The goal of this project is to make the cheapest RCM board.* 1.75 by 1.575 inches, 44.45 by 40.0 mil...
-
RCMhardwareNibble-v1.8 https://github.com/RCMgames/RCM-Hardware-Nibble/The RCM Nibble is the smallest board in my series of...
-
I2C 8 channel quadrature encoder reader - ByteSizedEncoderDecoder - v1.1 Reads 8 quadrature encoders1.0x0.85 inches, 25.4x21.59 millimetersI2C (Qwiic Compatible)powered by a...
-
Robot-Control-Module-V4 V1.3 Documentation, KiCAD, Arduino software libraries, and more are all on GitHub: https://github.com/RCM...
-
Byte Sized Encoder Decoder (v1.0) This project has been replaced by a newer version with improved silkscreen and files so PCBWay can d...
-
[PROTOTYPE, THIS VERSION HAS PROBLEMS] Robot Control Module BYTE V1 has been replaced with a new, working design! RCMByte V2Here is information about how to use thes...
-
RCMHardwareByte-v2.3 https://github.com/RCMgames/RCM-Hardware-BYTEThe RCM BYTE is the most powerful board in my series of...
-
Cheap wifi connected Robot Control Module - RCM D1 v1.0 The goal of this project is to make the cheapest RCM board.* 1.75 by 1.575 inches, 44.45 by 40.0 mil...
-
RCMhardwareNibble-v1.8 https://github.com/RCMgames/RCM-Hardware-Nibble/The RCM Nibble is the smallest board in my series of...
-
I2C 8 channel quadrature encoder reader - ByteSizedEncoderDecoder - v1.1 Reads 8 quadrature encoders1.0x0.85 inches, 25.4x21.59 millimetersI2C (Qwiic Compatible)powered by a...
-
Robot-Control-Module-V4 V1.3 Documentation, KiCAD, Arduino software libraries, and more are all on GitHub: https://github.com/RCM...
-
Byte Sized Encoder Decoder (v1.0) This project has been replaced by a newer version with improved silkscreen and files so PCBWay can d...
-
-
-
Modifying a Hotplate to a Reflow Solder Station
622 1 5 -
MPL3115A2 Barometric Pressure, Altitude, and Temperature Sensor
349 0 1 -
-
Nintendo 64DD Replacement Shell
319 0 1 -
V2 Commodore AMIGA USB-C Power Sink Delivery High Efficiency Supply Triple Output 5V ±12V OLED display ATARI compatible shark 100W
835 4 2 -
How to measure weight with Load Cell and HX711
587 0 3
thanks, here's the Kicad source files (that still need work): https://github.com/RCMgames/RCM_hardware_documentation_and_user_guide/tree/v1/rcmbytekicad
thanks, here's the Kicad source files. https://github.com/RCMgames/RCM_hardware_documentation_and_user_guide/tree/v1/rcmbytekicad