|
stepper motor |
x 3 | |
|
Arduino_UNO_R3 |
x 1 | |
|
Arduino cnc shield |
x 1 | |
![]() |
A4988 Stepper Motor Driver Module |
x 4 | |
|
power source 12VDC 3+ Amps |
x 1 | |
|
Laser Neje 30 W |
x 1 | |
|
rods 8mm |
x 8 | |
|
Lienal Bearing |
x 8 | |
|
screw |
x 1 |
|
lightburn |
|
|
Laser GRBL |
|
![]() |
arduino IDEArduino
|
CNC_DIY_LASER_PLOTTER_VYNIL CUTTER
ABOUT THIS PROJECT
Summary
To develop a CNC need you to learn about code, IT, electricity, electronics, and get some mechanics skills. One method to build a CNC is described below, step by step.
After a paced process, and a lot of interruptions, you can watch operating the machine I built , in the following video:
CNC - Cutting and Engraving
CNC LaserModule Arriving from China
I took my first challenge with a mini CNC DIY, this machine partially worked; I didn't get the stage of install the Z axe. The idea was to built it as cheap as possible, in this video you can watch the results:
Mini CNC - First attempt
"I had a dream"
As you can see at the end of the previous video, I was preparing the next prototype, but it was a "portable concept"; later on when I finished the testing and assembly of this draft prototype I change my mind for a static and "as simple as possible" concept.
Portable concept with stepper motors-Attempt-"I had a dream"
Height calibration-Alignment
Portable concepts
STEP 0:
The concept, the scope of work limits and boundaries
The concept, goal and roadmap for this project was established as follows:
To built, at minimal cost one CNC with enough working area and focused to be a tool for craftsmen, artists and/or Hobbysts. All these using open source software and with the possibility to switch from plotter to laser and to router. I discard early the idea to implement the feature of 3D printer.3D printer is one new and future project challneging I want to develop.
One tip to start and really finish this project is to go in a slow pace, increase your patience, learn from other builders, and try to keep calm. You need to take this activity as a craftman.
So let start to explain the step by step of this project taking into account this mindmap:
CNC build MindMap
Step 1:
Design and built your machine frame
Design your frame and adjust the mechanical parts to the dimensions of the machine you want. I bought, and cut a wood as the base of the machine. Taking care of support the ends of X and Y axis without mechanicals errors or instabilities, so wight of wood and width are important.
Wood base and steel rods draft location
Wood Base and linear bolts
One X axe assembly and test of linear bearings alignment
With the portable model, I had learnt that stepper motors transfer to the belts high forces alongside of the steel rods, so we need to be sure that each end of the each steel rod is fixed and immobilized.
Other aspect to take into account is that the bearings need to be perfectly aligned and move freely, so you need to calibrate the the distance between each steel rod, this distance should be the same in all the route with low error tolerance, otherwise the motors will be producing continuously miss-alignment due to differential friction in each steel rod.
Step 2:
Install motors, pulley and Belts
Establish strategy to install motors, pulley and belts. I used nema 17 motors and 6 mm width pulley and belts GT2 type . These elements should be installed in the position more efficient you consider. I aligned the pulleys at the same height of the steel rod, it works for me.
Motor pulleys installed almost at the same height of the steel rods centerline
Pulleys aligned at almost at the same height of the steel rods
Step 3:
Mechanical calibration of X and Y axis
In this case the design was oriented to use X and X' clone motor , one Y axe motor and one interchangeable Z axe motor. For this purpose I installed the nema 17 motors and configure the Clone for the X axe in the CNC shield.
At this moment and for weeks I focused in calibrate and test only X and Y axis.
It was a way to have a minor number of variable to be adjusting step by step.
Step 4:
CNC shield, Arduino Board, Drives, Software, Power source
In this step appears the CNC shield, Arduino, Drives, CNC softwares and Power Source
to Install the CNC shield in the Arduino
It is neccesary previously to upload to the arduino this software:
https://github.com/Protoneer/GRBL-Arduino-Library/blob/master/examples/GRBLtoArduino/GRBLtoArduino.ino
to Install the jumpers to work with micro stepping-this is a MUST in LASER mode
picture
to Install the drivers and heat dissipators in the CNC shield
pictures
to Calibrate the drivers
Drivers Calibration procedure by "el profe Garcia"
This is a key factor of successful of this project, you need to learn and apply properly these procedures.
I learnt a lot watching, again and again ,the videos from "el profe garcia", please check these videos :
CNC videos by "el profe Garcia"
Take care at this time you can cause damages in your Arduino UNO CNC shield and drives if you have the motors or the external power source connected to your Arduino UNO CNC shield during this process
External Power source to feed the motors
The machine will have 4 motors-Nema 17, each motor are going to use 0.3Amps- 0.4 Amps, so you need to size properly this power source- I choose one 12V- 3A- 120VAC/60HZ and until today I haven't had any problem.
Power Source utilized in Tests Phase-12V-3A Output
When you need to switch to a semi pro router for wood the NEMA17 motors are limited, so you will need NEMA23 heavy duty motors high torque and possibly screws no belts . However this machine can work with a mototool but you need to monitor temperature of the step motors. In this case the power source need to be upgraded to supply the amperes and voltage required for the new configuration.
Step 5:
Calibrate the stepper motors parameters
This is an assay and error iteration process- you need to enjoy and try to have fun identifying the behavior of the motors and machine. There are recommendations for the value of these parameter values but it is important to test as much as possible.
Be prepared to feel the happiness when your machine run by first time, and be prepared to have your machine death by weeks without any explanation-esoteric explanations are not valid always there are technical reasons for the fail state. In the last event you need to use methods to isolated, tracking and find fails in any machine.
LaserGRBL_Sofware GUI
Motor Parameters-LaserGRBL write into Arduino GRBL
PWM option activated to control the LASER
Be sure , because if you do not calibrate the drivers in a good way, you will be frustrated in this project- do not go ahead if you are no 100% sure you can confirm this procedures was done right.
Be careful the motor's coils connections are one main source of fails of your machine, you need to be 100% sure the wiring is right and the sequence are going to produce the right output.
You need to install 3 jumpers if you want micro stepping- for laser and to use LASERGRBL software, or Lightburn this is a basic condition.
You need to install previously this software
GRBL to Arduino software -uploaded to arduino
Universal G code sender platform or LASERGRBL software- installed and running in your computer
Once you have these components you need to test and try parameters, please see this video:
Step Motors Parameters configuration
The idea is to understand what is happening for each configuration and search for the best parameter of your machine-I really enjoy for days testing parameters.
Step 6:
CNC X,Y tests
We are ready to use with limitations our CNC, I recommend this path to test X and Y axis with markers.
At this moment the machine builder are going to find a lot of mechanics deficiencies that turn into challenges to face, this is a way to learn how to solve these issues and I -as a builder- started to love more and more this machine.
Step 7:
CNC X, Y,Z tests
Step 8:
Emergency STOP Button and End Stop Switches
Over the test the machine some times going over the limits and parts , as a consequence the motors are suffering these forced and wrong operations. To prevent damages and people injuries we need to install
Limit switches - for each axe
Emergency Stop Button
Others- fusibles/Interlocks/Current limitation
Tests are performed with pens or markers, however when you install a laser, a mototool or a spindle, risks of serious injuries are shifted. So please check carefully, at this point of the project, all the protections and interlocks you need to consider for install,test and operate properly.
In the case of use laser your risks of personal injuries and accidents are high so the path could be:
1- Pencils
2- Markers
3- Mototools
4- Laser
To working and testing with Laser you need a very serious risk assessment and googles, if you don't have skills to do that I recommend STOP here and request for help.
Step 9:
To redesign and build the CNC's own parts-
For this step you need better a laser with 90W of power, because the mechanical system for routing wood is weakness. Nema 17 motors have low torque and routing process need good power to work properly in different materials.
In this case we have a laser of 30W and wood thickness admited to cut is 3mm-5 mm afer variois passes. However with a good laser diode, the list of parts you can built to revamp the machines are:
-Motor support
-X axis sliders (2)
-Z axe
-Box for controls
-Chain for cables
-Box for power
-CNC Frame in wood light, expanded and collapsible
Step 10:
Results as plotter, Laser, Router
Lizards
My Products with CNC Laser Cutter-Designed by VAGA- Artists team
Red Lizard
Red & Green Lizards
Dinosauries 3D
Animals for wall decoration:
Drawings working as plotter:
Metal Engraving:
Step 11:
Lesson learnt and new machine design
This project is like to open a door for new initiatives, so when you reach this point you will be thinking in a lot of ideas for this machine.
Project budget is low and acceptable for a DIY CNC. You will have the temptation to spend more and more money in accessories &parts.
We are Pangeatech MakersCol - From Colombia LATAM
Thanks.
/* Thanks for supporting Open-Hard/Soft-ware and thanks for all of the contributors to this project. For extra info on GRBL please have a look at my blog : http://blog.protoneer.co.nz/tag/grbl/ Grbl is free software: you can redistribute it and/or modify it under the terms of the GNU General Public License as published by the Free Software Foundation, either version 3 of the License, or (at your option) any later version. Grbl is distributed in the hope that it will be useful, but WITHOUT ANY WARRANTY; without even the implied warranty of MERCHANTABILITY or FITNESS FOR A PARTICULAR PURPOSE. See the GNU General Public License for more details. http://www.gnu.org/licenses/ */ /* Supported hardware: Arduino Duemilanove Arduino Uno Arduino Mega 2560 (Limited Testing) */ #include <grblmain.h> void setup(){ startGrbl(); } void loop(){}
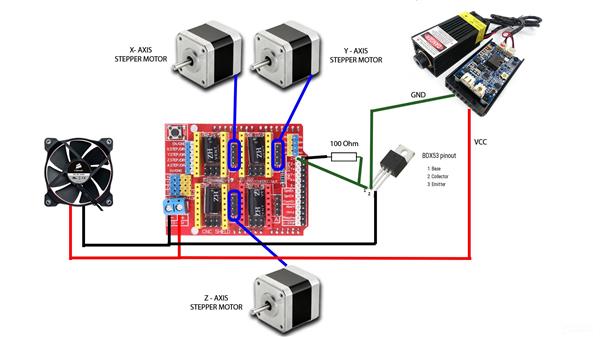
CNC_DIY_LASER_PLOTTER_VYNIL CUTTER
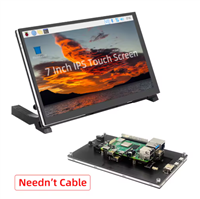
Raspberry Pi 5 7 Inch Touch Screen IPS 1024x600 HD LCD HDMI-compatible Display for RPI 4B 3B+ OPI 5 AIDA64 PC Secondary Screen(Without Speaker)
BUY NOW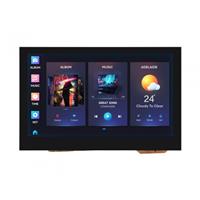
ESP32-S3 4.3inch Capacitive Touch Display Development Board, 800×480, 5-point Touch, 32-bit LX7 Dual-core Processor
BUY NOW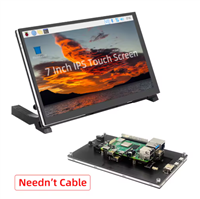
Raspberry Pi 5 7 Inch Touch Screen IPS 1024x600 HD LCD HDMI-compatible Display for RPI 4B 3B+ OPI 5 AIDA64 PC Secondary Screen(Without Speaker)
BUY NOW- Comments(0)
- Likes(1)

-
Engineer Aug 09,2024
- 0 USER VOTES
- YOUR VOTE 0.00 0.00
- 1
- 2
- 3
- 4
- 5
- 6
- 7
- 8
- 9
- 10
- 1
- 2
- 3
- 4
- 5
- 6
- 7
- 8
- 9
- 10
- 1
- 2
- 3
- 4
- 5
- 6
- 7
- 8
- 9
- 10
- 1
- 2
- 3
- 4
- 5
- 6
- 7
- 8
- 9
- 10
More by Bolaños Hernando
-
Robot Arm to implement CV projects StoryFour years ago I was looking for a good robot arm, this year I have time and decided to replica...
-
MINI ROBOT ARM MINI ROBOT ARM - YouTubeIdea based on Tutorials shared by Mr. Pinaut for :software -schematics -inst...
-
Bluetooth Controlled LEGO Toy Car MotivationMy motivation was my kids. I want to share time and have fun with them teaching them some ...
-
Integrated HOME Irrigation System Motivation:Since I left the university, 24 years ago, I haven't had the chance to update my knowledg...
-
Rubik's Cube Solver Robot DIY - V.3.0 Scope of the projectThe idea was to build a Rubik's cube solver robot, as simple as possible, easy t...
-
Rubik's Cube Solver Robot v1 The drivers to develop my project were:Rubik′s cube is a "best seller" category toy, more than 350 m...
-
How to built a Hybrid Bike Computer Hybrid Bike ComputerThis PCB is a Cheap solution to track your training preformanceBased o esp32 , r...
-
My nunchuck adapter (PCB) for my Galagino Retro console_Running on a ESP32 device Galagino is an open source idea of hardware and software from Tiil Harbaum (https://github.com/harba...
-
PCB DESIGN FOR BIKE COMPUTER DIY PCB DESIGN FOR A BIKE COMPUTER DIY - QBIKOThis PCB was designed to run a BIke computer based on ESP3...
-
How to build a Mecanum Wheels Robot with an Arduino Mega and a PCB Once I finished my first version of this robot I found it interesting to develop a PCB, mount and so...
-
How to build a Bike computer DIY-Heart Rate sensor comparison and selection This project is about a tutorial to evaluate 3 hear rate Sensor. In this way I will choose the bette...
-
How to build a Bike computer with a ESP32 -WROOM + 2 Reed Switches + 1 Cellular Phone(old with GPS and BTH) The complete tutorial explaining all the details for this project, can be watched in the next vide...
-
How to build a Table Tennis Robot - V2 Story: Once I finished my first protoype for a TTR , I recognize and learnt about a lot of improveme...
-
How to build a Mecanum Wheels Robot_V1 The storyHow to bulild a Robot usually is an assay and error process, you can see my first prototype...
-
How to use AI to program a 2DOF ROBOT- Arduino+ pyhton+opencv+chatgp+ps3eyecam The challenge was to obtanin a mix of code generated by chatgpt for pyhton, opencv, and arduino and ...
-
Node MCU based Wi Fi Servo Switch- DIY About:Regulations usually forbide to introduce pieces of equipment in the conecctions and wiring of ...
-
CNC_DIY_LASER_PLOTTER_VYNIL CUTTER ABOUT THIS PROJECTSummaryTo develop a CNC need you to learn about code, IT, electricity, electronics...
-
Arduino Based Table Tennis Robot V1 DIY AboutThis project is about a TTR(Table Tennis Robot) made at home with cardboard and wood, using som...
-
Robot Arm to implement CV projects StoryFour years ago I was looking for a good robot arm, this year I have time and decided to replica...
-
MINI ROBOT ARM MINI ROBOT ARM - YouTubeIdea based on Tutorials shared by Mr. Pinaut for :software -schematics -inst...
-
Bluetooth Controlled LEGO Toy Car MotivationMy motivation was my kids. I want to share time and have fun with them teaching them some ...
-
Integrated HOME Irrigation System Motivation:Since I left the university, 24 years ago, I haven't had the chance to update my knowledg...
-
Rubik's Cube Solver Robot DIY - V.3.0 Scope of the projectThe idea was to build a Rubik's cube solver robot, as simple as possible, easy t...
-
Rubik's Cube Solver Robot v1 The drivers to develop my project were:Rubik′s cube is a "best seller" category toy, more than 350 m...
-
How to built a Hybrid Bike Computer Hybrid Bike ComputerThis PCB is a Cheap solution to track your training preformanceBased o esp32 , r...
-
My nunchuck adapter (PCB) for my Galagino Retro console_Running on a ESP32 device Galagino is an open source idea of hardware and software from Tiil Harbaum (https://github.com/harba...
-
PCB DESIGN FOR BIKE COMPUTER DIY PCB DESIGN FOR A BIKE COMPUTER DIY - QBIKOThis PCB was designed to run a BIke computer based on ESP3...
-
How to build a Mecanum Wheels Robot with an Arduino Mega and a PCB Once I finished my first version of this robot I found it interesting to develop a PCB, mount and so...
-
How to build a Bike computer DIY-Heart Rate sensor comparison and selection This project is about a tutorial to evaluate 3 hear rate Sensor. In this way I will choose the bette...
-
How to build a Bike computer with a ESP32 -WROOM + 2 Reed Switches + 1 Cellular Phone(old with GPS and BTH) The complete tutorial explaining all the details for this project, can be watched in the next vide...
-
Modifying a Hotplate to a Reflow Solder Station
440 0 4 -
MPL3115A2 Barometric Pressure, Altitude, and Temperature Sensor
262 0 1 -
-
Nintendo 64DD Replacement Shell
270 0 1 -
V2 Commodore AMIGA USB-C Power Sink Delivery High Efficiency Supply Triple Output 5V ±12V OLED display ATARI compatible shark 100W
687 4 2 -
How to measure weight with Load Cell and HX711
525 0 3 -
-
Instrumentation Input, high impedance with 16 bit 1MSPS ADC for SPI
604 1 0